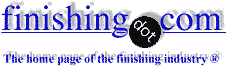
-----
Sodium orthophosphate analysis
Q. I want to analyse sodium orthophosphate in electroless nickel plating solution. I am looking for titration method for the analysis of sodium orthophosphate.
Chianglktechnical support officer - Singapore
2004
A. I've always preferred to rely on calculation of total hypo added (turnovers) and speed of reaction to decide when to dump the bath so I've never tried the following and cannot guarantee it'll work. Sample 2 mL of bath, add 20 mL H2O, + 20 mL Na HCO3 at 5%, + 50 mL Iodine soln. 0.1N. Store in dark 30 min. Add 20 mL acetic acid ⇦ on eBay or Amazon [affil links] . Titrate with 0.1N sodium thiosulphate ⇦ on eBay or Amazon [affil links] add starch when it turns yellow. Continue titrating until purple color from starch disappears. Calculation 5-(0.1 x mL thiosulphate) x 0.25 x 82 = Na Orthophosphite In my experience there are other more frequent causes for an EN bath that doesn't plate than excess ortho.
Guillermo MarrufoMonterrey, NL, Mexico
A. If orthophosphIte rather than orthophosphAte is what you are looking for, the method described by Mr. Marrufo or variations thereof should work. I occasionally used such a variation, based on R.T. Jones and E.H. Swift, Anal. Chem. 25, 1272 (1953). It involves adding the sample to a phosphate buffer solution of pH 7.3, adding excess 0.1 N iodine solution, stoppering the flask and keeping it in the dark for 1 hour, then adding a few ml of 6 M acetic acid and back-titrating with 0.1 N thiosulphate to the starch-iodine end-point. Hypophosphite, of course, does not interfere.
As for orthophosphAte, I'm afraid you are momentarily on your own... Ion chromatography is nice if you can get it.
- Yorktown Heights, New York
First of two simultaneous responses --
I thought the mis-spelling was due to Mr/Mrs Chianglk not familiar with it but rather ended up learning more. Thanks for the precision Emanuel. By the way, could you enlighten me a bit more about orthophosphate? How and how fast is it formed and what effects does it have in the plating bath? Also, how soluble is it?
Guillermo MarrufoMonterrey, NL, Mexico
Second of two simultaneous responses -- 2004
For orthophosphate analysis, a gravimetric precipitation as ammonium magnesium phosphate hexahydrate is given in Vogel's Quantitative Inorganic Analysis
[on
Amazon affil links], 4th Edn., pages 498-499. For a "spiked" calibration sample, add sufficient nitric acid to oxidize the known hypophosphite content to orthophosphate. As an alternative to weighing, the isolated precipitate can be re-dissolved and titrated by a method on p. 335. I don't know any plater doing these analyses.
Two indirect methods work reasonably well for orthophosphate concentration:
1) Hypophosphite usage. When forming Ni-8%P EN plating,
92% of the hypophosphite consumed creates orthophosphate. Hypo has a Formula Weight of 88; ortho's FW = 103. Thus, the wt. of ortho = 0.92 x (103/88) x weight of hypo used.
2) Specific gravity. Record the SG of the bath (samples cooled to 60 F) over the life of the bath. For a Ni source of NiSO4 producing an 8%P EN, per 1 gram of Ni used, 1.637 g SO4 + 1.1705 g sodium orthophosphate are produced. The hypo concentration is therefore 41.7% of the SG increase w.r.t. a new bath. The calculated result is very slightly high, probably due to pH adjustments and other bath additives.
These calculations are easily adjusted for EN's of lower or higher P content.
- Goleta, California

Rest in peace, Ken. Thank you for your hard work which the finishing world, and we at finishing.com, continue to benefit from.
Q, A, or Comment on THIS thread -or- Start a NEW Thread