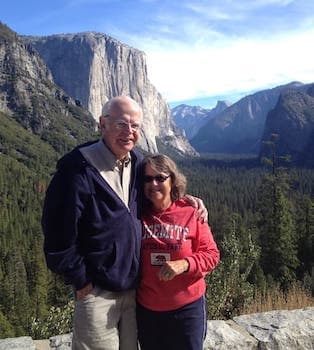
Curated with aloha by
Ted Mooney, P.E. RET
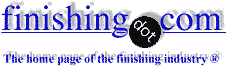
The authoritative public forum
for Metal Finishing 1989-2025
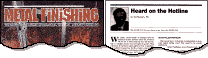
-----
Patches on cold rolled sheet
Q. I am working in a research organization who makes steel cold rolling oils. My job is to field test different newly developed rolling oils. Recently, I am facing a problem of sheet patches after cold rolling using water based rolling oil. The patches are not apparent at the time of cold rolling but when the CR coil is taken on rewinding line after say about 4 hours of rolling, during unwinding, sheet patches (yellow, brown or even black in color) are observed. The water used in making emulsion is de-mineralized and the patches were found to occur in fresh charge itself.
Any body who has faced a similar problem or who can give me some insight into this, may please contact.
rolling lubricant application engineer - Faridabad, Haryana, India
2004
A. THE PROBLEM YOU ARE TALKING ABOUT IS CALLED BLACK PATCH. THIS IS NOT OBSERVED WHILE ROLLING BUT AFTER DEGREASING WHICH IS DONE TO REMOVE EMULSION AFTER COLD ROLLING. ONE OF THE MAIN REASON FOR BLACK PATCH IS EMULSION CARRY-OVER.CHECK YOUR NOZZLES AND TRY TO STOP EMULSION CARRY-OVER AT THE TIME OF ROLLING.
RAJANIKANT MARU- JAMSHEDPUR, JHARKHAND, India
2004
Q. Have seen similar black patches in cold rolled steel. These patches disappear after continuous annealing line but remain after hood annealing. Has anyone been able to solve the problem? If so, how?
S D Lashkari- India
2004
A. Dear Mr Umesh Srivastava & Mr S D Lashkari,
The problems of black patches, which you are facing can be solved by using air knife to prevent the coolant carry over on the strip, Also you can increase the pressure of air wiper or knife which you are using.
- Hamirpur, India
2004
A. The black, brown patches are due to corrosion of Steel. By addition of anti oxidants into the emulsion the black patches will reduced or be eliminated.
S D Lashkari- Maharashtra, Mumbai, India
February 9, 2008
Q. In my company I am working on the rolling mill. The main problem that I face today is the black patches on angles and flat bars of stainless steel. These are hot rolled and then pickled in nitric acid+hydrofluoric acid for finishing. Black patches come after the pickling stage.
We grind out these patches. Most of the times, when these ground products are sent to pickling again the patches reappear.
In the furnace we use Light Diesel Oil.
If anybody is having idea about this problem, please let me know.
Thanks,
- MUMBAI, India
October 9, 2010
Q. Black patches come on the cold rolled strip at the customer's premises. The same is not seen at the time of inspection after skin pass mill. Only anti-rust oil is applied and the material is packed in vci paper and metal clad immediately. Heavy patches develop as quickly as 15-20 days.
Anybody who has faced this problem can suggest some ideas?
- BOKARO, JHARKHAND, India
July 24, 2013
Q. We have a pickling line of 40 meter length. We use 20% HCl at 65-70 °C, followed by rinsing by cold water, and then by hot demineralised water rinsing, and then followed by air knife to blow off moisture, and finally coiling. We pickle AISI 1062 to AISI 1080 grades of carbon steel. The problem we are facing is: pickling appears to be good at 14 mpm speed, but when we rub top surface with finger, we feel a little soot. Chloride content of Rinse water is 50 ppm.
When we take these coils for rolling, it sometimes generates white patches on top surface only after single pass of cold rolling. What could this be? Is it due to dirt or hydrogen embrittlement? We are not clear.
Steel - Surat, Gujarat, India
September 25, 2017
Q, A, or Comment on THIS thread -or- Start a NEW Thread