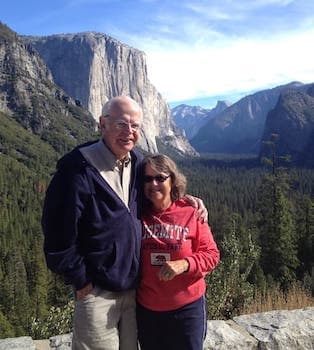
Curated with aloha by
Ted Mooney, P.E. RET
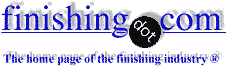
The authoritative public forum
for Metal Finishing 1989-2025
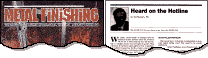
Thread 271/60
Hard chrome plating - coefficient of friction

Vijaya, did you ever figure out what caused the higher coefficient of friction? I seem to have the same issue.
G HENDERSON- Pennsylvania, USA
August 3, 2022
publicly reply to G HENDERSON
----
Ed. note: Other readers are encouraged to respond. Vijaya's posting was from 14 years ago, so his e-mail probably doesn't work.
⇩ Related postings, oldest first ⇩
Q. We have a problem with a hard chromium plated disc. While doing wear test of a hard chrome plated disc against a steel pin, we are getting high coefficient of friction value. But the coefficient of friction value is less while doing wear test of steel disc against the same pin. Also we are getting some black marks over the plated steel along the steel pin's path. Do let me know about the possible reasons for this behavior.
Thanks in advance.
Vijaya LakshmiDesign Engineer - Coimbatore, Tamil Nadu, I N D I A
2004
publicly reply to Vijaya Lakshmi
A. Dear Madam,
1. Ensure that there is no roughness on plated surface.
2. Ensure the parent material is lapped/honed before plating.
3. Is the pin blackened? In such case it can leave black marks on plated surface.
- Aurangabad, Maharashtra, India
publicly reply to S Sudhanshu
Q. Sir,
As you said
1. We are checking the surface roughness value before conducting the wear test and the Ra value is found to be 0.2 microns only. We don't find any roughness along the surface.
2. The parent material is always lapped before plating.
3. The pin surface is slightly blackened and I agree that this may line marks along path.
Even after conducting more trials on this, still we are getting high coefficient of friction value. A hardened steel pin of 55 HRC is tested against hard chrome plated steel disc. The value we are getting is about 0.6 - 0.7 which is much higher than the expected value. What should be the minimum porosity level in Hard chrome plating? Kindly let me know the reason for this kind of behavior and is there any other way of predicting the friction coefficient value. Thanks in advance.
Vijaya Lakshmi [returning]- Coimbatore, INDIA
2004
publicly reply to Vijaya Lakshmi
A. Hello,
The hardness of the substrate is an important factor. If the pin is digging into the substrate (high contact or hertz stress) due to its lower hardness, you may get high friction coefficient. Check the hardness of substrate before plating. It should also be noted that for steels having UTS more than 1000 MPa (and high hardness) they should be treated for hydrogen embrittlement just after plating by heating (See standard IS:1337-1993 Hard Chrome plating for engineering application.
Jishnu Dwivedi- Indore, India
publicly reply to Jishnu Dwivedi
Q. Hello sir,
My question is what is the coefficient of friction between chromium and rubber; and chromium and wool?
- Mumbai, Maharashtra, India
December 12, 2014
publicly reply to pritam tawele
A. Hello Pritam,
I doubt that any responder on this site knows this answer off the top of their head. You would have to narrow it down to static coefficient, or sliding coefficient. If it is sliding coefficient you are looking for, factors such as mating pressure of the 2 materials, speed of the sliding motion and the movement frequency. As far as static coefficients the same factors would apply as well as temperature and humidity. The density of the rubber would be a factor to consider as well. So in a nut shell it's going to be very difficult to get an exact answer.
Process Engineer - Phoenix, Arizona USA
publicly reply to Mark Baker
Q, A, or Comment on THIS thread -or- Start a NEW Thread