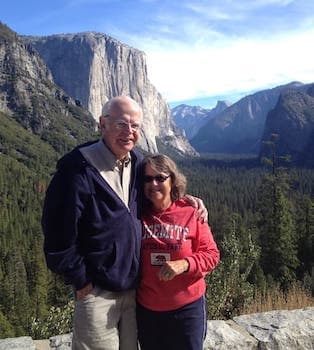
Curated with aloha by
Ted Mooney, P.E. RET
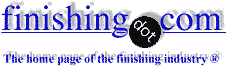
The authoritative public forum
for Metal Finishing 1989-2025
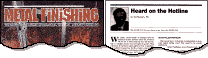
-----
Anodized parts have ghost-like stain
2004
I have ghost-like variation in color on the surfaces of my anodized aluminum 6061-t6 parts (cylindrical parts for fishing reels ± 4" diameter). the parts are lightly etched (2-3 mins) after which they are anodized and sealed, so the color is natural/clear with a semi-matte finish. but, there are some variations in the color, in particular a band of more shiny tone around the perimeter. a photo would have been good but it probably won't show the contrast that well. is the problem metallurgical or is it the platers fault.
2nd part of the question - the anodizing shop over-etched parts and now critical sizes are out of tolerance. is it 'normal' to expect the plating shop to cover the cost of machining and material. the actual cost of anodizing is probably only 10% of the total , but because it's the last process it's up to them to get it right. should I accept 5% scrap, 10%, 20% ? I'm concerned that if I impose a liability clause on them, they'll not want to take on the work. your thoughts?
kindest, michael
Michael Georgiadishobbyist/engineer - Durban, KZN, South Africa
Give us more info like: the exact prep cycle, what is the deox, how old is the deox, then what is the dissolved aluminum, voltage, temperature, then what happens between the anodizing tank and the dye tank. What is getting into the pores and interfering with the dye getting into the pores: floating oil, dissolved aluminum, other sulphates, etc?
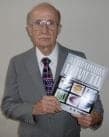
Robert H Probert
Robert H Probert Technical Services

Garner, North Carolina
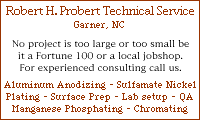
2004
2004
Robert,
With Michael being the end user, I doubt he'll be able to access any of the info you requested (also, he states the color is "clear/natural" so no dyes would be involved)
Michael,
Without actually seeing the flaw you describe,it sounds to me like its a metallurgical problem (I've whined enough about the quality/consistency of American Aluminum in this forum before. I work with a lot of aluminum manufactured in Japan, and believe me, they are kicking our butts) The subject of acceptable scrap rates, and liability is a pretty touchy one with metal finishers. We are often asked to coat parts that have value in the $1000s, for mere pennies. This is a subject that should be addressed with your particular vendor. Our policy has always been to replace the part (or the cost of the part) if we screw up. It also has been our policy to contact a customer PRIOR to reworking a job to ask about tight tolerances and such. However, I know of several coaters with a disclaimer saying that the coater will only be liable up to the total amount of the coating costs of that job. As far as scrap, and acceptable rates go..you really didn't give us enough info as to how many parts you coat. But I like to hold my scrap/rework rate at <1% (for all my jobs, not just one customer). There are many good, high quality coaters out there, and if you have consistent problems, I would suggest you find another vendor. I won't be able to give you, or your coater, any advice on how to correct the flaw you see in your part without actually seeing it, or a decent photograph. You didn't mention if the color variations were from batch-to-batch, or if they were color variations on each individual reel. Oh crap.. I just noticed you were writing from South Africa..please excuse my reference to American aluminum!
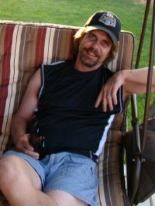
Marc Green
anodizer - Boise, Idaho
I am asking these questions of the jobbing shop. will post their reply. thanks for now
Michael Georgiadishobbyist - Durban, South Africa
2004
Marc thanks for your reply. The problem on the clear anodized parts is visible on a batch not a sigle reel. i.e. all the reels from that batch have that problem. I don't think the plater is going to tell me if they had floating oil or old deox. but they did agree to pay for the costs - good on them! They also agree to try to improve their process control and contact not rework. They said the reason for rework was because of the jigs used hence color did not take well. is this acceptable. I think they should have jigged properly or contacted me if problems perceived BEFORE doing the work. By the way I make about 20 units at a time. We don't have many vendors to choose from so I am a bit reluctant to change right now. I sent the scrap parts back so I cannot get a photo but if you imagine a 4" disc of clear anodized ali with a 'ring' of grey about 1/8" in width near to the edge. That what it looks like. It does not come off with scrubbing or light abrasion. Problem does not exist on black parts.
Michael Georgiadishobbyist - Durban, South Africa
2004
Dark grey around the edges? I have had a similar sounding "starbursting" effect on some of our parts we plate here in house.. the alloy was 2024 and the way we had racked was around the outside of the part, resulting in the perimeter of the parts plating almost .004 and the interior of the disks plating only .0025. I have come to the conclusion it was the style that we racked, and our attempt to "get the current to the part" had a bit of failure. we did purchase a better racking solution that eliminated the problem.
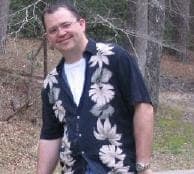
Ryan Cook
Toccoa, Georgia
2006
Q, A, or Comment on THIS thread -or- Start a NEW Thread