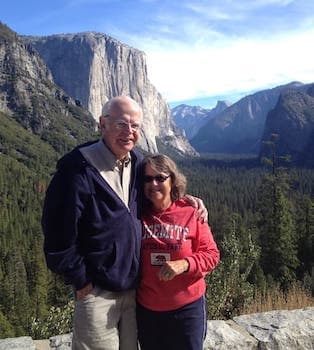
Curated with aloha by
Ted Mooney, P.E. RET
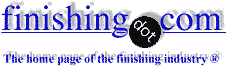
The authoritative public forum
for Metal Finishing 1989-2025
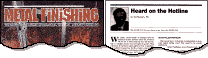
-----
Electroless Nickel in Saltwater Environment
2004
I have designed a piston type vacuum pump fabricated from 4%P electroless nickel plated 2024 aluminum. This pump can be exposed to salt water. The plating thickness is 12-15 um. The pump shaft runs on linear bearings with a high bearing load (2000 psi). The linear bearings run on the nickel surfaces, which is why I selected the low phos. The surfaces where the NBR O-rings run are self destructing after 90 days of service, mostly on units which are exposed to salt water. The bearing surfaces look fine for the most part.
Did I completely miss the mark in using EN for this environment? It has become apparent the coating must be completely intact or the aluminum corrodes quickly and the nickel flakes off. Is it reasonable to expect a coherent plating? Is EN used extensively in seawater environments?
I am in a quandary as whether to completely abandon the EN coating or to simply try a mid-phos plating and double the thickness. I would use mid-phos in an effort to find a balance between wear and corrosion resistance.
Doug Rushdesign engineer - Salt Lake City, Utah, USA
If the Aluminum has insufficient strength then it would be as sitting on a glass put on a bed. No matter how hard, it will surely break. If this is happening a thickness or hardness increase will not eliminate the problem.
Guillermo MarrufoMonterrey, NL, Mexico
2004
![]() |
2004
Guillermo is correct with his glass over a mattress analogy. However, a more important consideration is galvanic corrosion. The potential difference between EN and aluminum is about 450 mv in seawater. So unless you have a perfect coating, wherever aluminum is exposed to seawater a large battery is produced which rapidly corrodes the aluminum and undermines the coating. Perfect coatings usually are only produced on perfect substrates. EN will replicate any defects in the substrate. While EN is used in marine environments, it is more common on brass or steel substrates. ![]() Ron Duncan [deceased] - LaVergne, Tennessee It is our sad duty to note Ron's passing on Dec. 15, 2006. A brief obituary opens Episode 13 of our Podcast. I am quite certain the nickel aluminum does not deflect enough to crack the plating. The bottom line is that when an o-ring is reciprocating at 1 hz on a 12-15 µm 4% P electroless nickel plated bore and is exposed to salt water, the bore life is 3 months. Is it possible modify the nickel plating and achieve a minimum life of 2 years? If so, what modifications would you recommend? Doug Rushdesign engineer - Salt Lake City, Utah, USA 2004 |
If the aluminum is a casting, castings are porous. The pores must be filled prior to electroless nickel plating. This will stop the corrosion of the aluminum. High phosphorus electroless nickel is more protective in salt water that 4% P EN, and slightly more ductile. It is also softer and may wear somewhat faster than $%. therefore I suggest a two layer EN first Hi phos 1 mil or more followed by 4% P EN .8 to 1 mil.
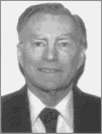
Don Baudrand
Consultant - Poulsbo, Washington
(Don is co-author of "Plating on Plastics" [on Amazon or AbeBooks affil links]
and "Plating ABS Plastics" [on Amazon or eBay or AbeBooks affil links])
2004
Thank you Ron. It seems that the electroless nickel should coat these flaws, and that steel would have a similar galvanic problem. But I am not one to ignore good advice from a knowledgable source. And you are correct, perfection is difficult to achieve. Now I'm off to face the challenges of hard anodizing 2024 and holding ± .0005 tolerances, and repeating all the qualification tests (fatigue testing in excess of 10 million cycles). Optimism is not a good trait in an engineer.
But one more question. What do you think about the possibililty of a duplex coating? High phos for corrosion resistance covered by low phos for wear resistance. Maybe the double coating will reduce the probability of flaws through the coating thickness. I know duplex coating are forbidden in the AMS spec. I am told that with careful process control it can work (i.e. not to much time between the two baths).
Doug Rushdesign engineer - Salt Lake City, Utah, USA
2004
I agree with Ron. But I still think the whole design would have to be reviewed. If the part is constantly exposed to a salt water environment and is a functional part, aluminum seems a bit like looking for trouble.
Guillermo MarrufoMonterrey, NL, Mexico
2004
Thanks Don. Apparently I didn't read down far enough before my last post. You were reading my mind. It looks like we have a consensus of 2.
Doug Rushdesign engineer - Salt Lake City, Utah, USA
2004
Q, A, or Comment on THIS thread -or- Start a NEW Thread