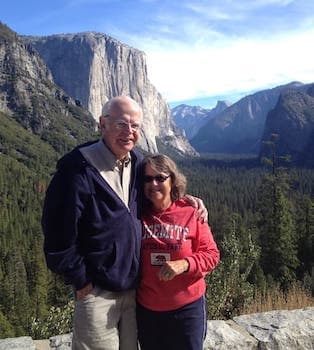
Curated with aloha by
Ted Mooney, P.E. RET
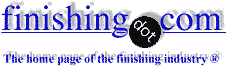
The authoritative public forum
for Metal Finishing 1989-2025
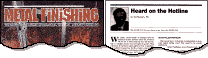
-----
Coating for aluminum heat sink

Q. I have an aluminum heat sink used in a cleanroom environment and therefore the surface needs to sealed to prevent oxidation and contamination to sensitive materials. Will a chromate coating have sufficient thermal conductivity to ensure good heat transfer? And is chromate a sacrificial coating or will it resist oxidation even if scratched? If the answer to these questions is 'no' than what would be the best coating to use?
Jim SbrognaSemiconductor Equipment Engineer - Natick , Massachusetts
2004
A. Heat sinks can be anodized. Chromate coatings will not cause thermal conductivity problems, but they are electrically conductive, which could be a problem or not. Chromate is not a sacrificial coating but it is "self healing" so it is helpful even in an environment where scratching is possible.
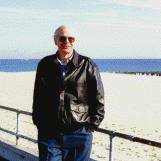
Ted Mooney, P.E.
Striving to live Aloha
finishing.com - Pine Beach, New Jersey
2004
A. In addition to all the accurate advice Ted sent to you, you may need also to know that bare unpainted chromate conversion coatings are limited to a surface temperature of 140 °F, above which the coatings disintegrate. Absolutely not suitable for a very hot sink.
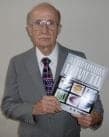
Robert H Probert
Robert H Probert Technical Services

Garner, North Carolina
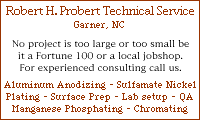
2004
A. The coating of choice for heat sinks has been electroless nickel forever. Corrosion resistant, conductive, both thermal and electrical. Even looks good.
Dan Weaver- Toccoa, Georgia
2004
Treatment &
Finishing of
Aluminium and
Its Alloys"
by Wernick, Pinner
& Sheasby
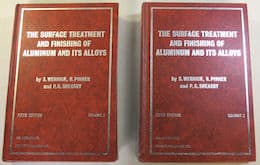
(note: this book is two volumes)
on eBay or
AbeBooks
or Amazon
(affil links)
A. Anodizing should be fine. Aluminum oxide is tough, proven, and is thermally a good conductor due to lattice phonon effects.
Dale Woika- Bellefonte, Pennsylvania, USA
2004
A. Electroless nickel is the best coating if you want maximum heat transfer. Anodize coatings are dielectric and have poor heat transfer characteristics. They are very corrosion resistant as is electroless nickel.
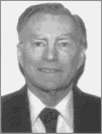
Don Baudrand
Consultant - Poulsbo, Washington
(Don is co-author of "Plating on Plastics" [on Amazon or AbeBooks affil links]
and "Plating ABS Plastics" [on Amazon or eBay or AbeBooks affil links])
2004
Q. Sir, if I want to increase heat transfer capacity of heat sink, electroless nickel coating will be okay, or you can suggest any other coating?
Hemant Jakhwal- Udaipur, Rajasthan, India
April 8, 2011
Q. Hi
I have a sealed aluminium case (with chromate conversion coating CL3) containing a PCB that can reach temperatures up to 110 °C (230 °F). The case has a finned area on the outer-upper face, and the PCB is fixed to A LOT of stumps or columns on the inner upper-face through copper-plated brass bolts. During some thermal tests I have discovered that the heat transfer between PCB and the case is quite bad, I guess that the conversion acts like a heat barrier. The question is: is there any other conversion/plating/anything that can improve this heat transfer while keeping the corrosion protection? I contacted a metal finishing service and they told me that nickel would do the job better, but I'm not quite sure about that since they have similar thermal conductivity... Any ideas?
Thank you in advance!
- Madrid, Spain
February 14, 2013
A. (1) The chromate conversion coating is not interfering with the heat transfer, but
(2) if the chromate is bare, at that temperature you are completely dehydrating the chromate coating and destroying it.
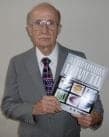
Robert H Probert
Robert H Probert Technical Services

Garner, North Carolina
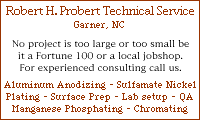
February 15, 2013
Q. I am working on a similar project. What would your recommendations be for the following.
Aluminum Heat Sink.
Completely submerged in salt and freshwater.
Best recommended protection for coating, while still maintaining thermal conductivity. For a high powered heat generating light. Temperatures around 230 °F
Avoiding corrosion. I know it can be anodized as one option, but I feel coating would be optimal.
Input would be greatly appreciated!
- Atlanta Georgia
March 27, 2014
A. Hi. As long as the coating will not be mechanically damaged, electroless nickel plating sounds ideal. But nickel is far more noble than aluminum, and will greatly accelerate the corrosion of the aluminum if the plating is porous, pinholed, or scratched and aluminum is exposed. Good luck.
Regards,
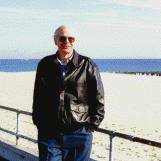
Ted Mooney, P.E.
Striving to live Aloha
finishing.com - Pine Beach, New Jersey
Tip: Readers want to learn from Your Situation 🙂
(little can be learned from abstract questions, so many readers skip them)
Q. Can anyone please tell me some disadvantages of aluminium coated heat sink for PCB. According to environmental effect.
Kushang Dankhara- Melbourne, VIC, Australia
September 24, 2015
September 2015
? Hi Kushang. Hopefully someone will fully understand your question and reply to it, but personally I would need you to offer more detail as I do not quite understand. Please try to be as specific as possible in describing your own situation. Thanks.
Regards,
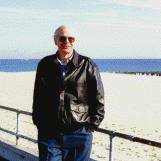
Ted Mooney, P.E.
Striving to live Aloha
finishing.com - Pine Beach, New Jersey
by Runge & Kaufman
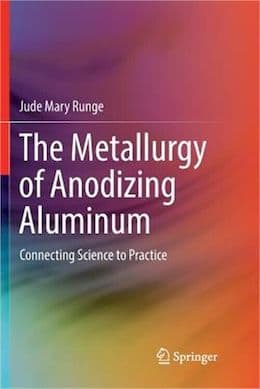
on AbeBooks
or eBay or
Amazon
(affil links)
A. If you truly mean aluminum coated, the drawback is the price of vapor deposition or the highly specialized electroplating from an organic media.
If you mean coated aluminum, the thickness of the coating will reduce the effectiveness of the heat sink giving up heat to the atmosphere.
Hexavalent chromium coating is a problem in many countries, but trivalent is available and is nearly as corrosion resistant but a bit more expensive.
Thin anodize is an option.
- Navarre, Florida
September 24, 2015
A. Hey, kushang, what particular application you were looking for you have not mentioned. For the cons you need to elaborate your Q's first.
Thank you.
Control Systems Engineer - Surat,Gujarat, INDIA.
October 25, 2016
If you would like to increase heat transfer, for a heatsink made of aluminum, with direct heaters beneath, we have a patent pending solution. Our current test results show 100-150% increase based on thickness of metal, and type. You can look up US patent US 9,265,092 which is for alufoils. Our solution for industrial coatings is based on this.
I realise this does not answer the issue regarding the surface, however it will help in terms of heat transfer.
- Copenhagen, Denmark
October 26, 2017
Q, A, or Comment on THIS thread -or- Start a NEW Thread