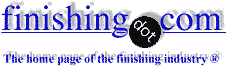
-----
Patchy Hard Coating of 2024
2004
Q. We are a machine shop currently starting up an anodizing department and have had a good deal of success with Type II & Type III anodizing of 6000 Series and 7000 Series Aluminum alloys. We have separate tanks for Type II (72 deg F) and Type III (32 deg F). The sulfuric acid concentration for both tanks is keep about 18 % with the type III tank having about 3 percent MAE additive. We have a Dynapower rectifier capable of both "voltage" and "synopsis" anodizing. The question I have relates to problems with 2024-T3. I am well aware that the copper content of 2024 tends to cause problems but I have had almost no luck in trying to develop an even oxide layer in our hard coat tank. I can achieve a uniform thickness of .0004" in our "Type II Tank" by ramping voltage slowly from 18 to 20 V over 20 minutes. Parts anodized in our type III tank do not develop an oxide layer consistently over the surface of the part. Typically, the surface of the part develops "pits" of thick coating (tan in color) with almost none on the rest of the same surface. As anodizing time proceeds, these pits become more numerous until they "fill in" the surface, yielding an overall patchy appearance with varing thickness.
I have made the following observations that might be clues to this problem.
-I am experimenting with a 76 sq in cube of 2024-T3 material
-When voltage anodizing, and slowly ramping the voltage, no current draw occurs until approx. 27 volts, then current spikes to the full current limit within seconds, (100's of amps if I let it)
-When constant current anodizing at 30 A/sq ft. Voltage climbs to about 30 V within a minute than settles down to about 27 V followed by a slow climb back to 30 V over 15 minutes
-Racks are titanium with titanium bolted connection
-Similar results (poor) were achieved by be with some actual parts made from the same material, but we had one of our better outside processors do the same parts with great success.
-6063 aluminum cathodes, (about 2 sq feet of cathode area, yes I know this is too much according to recommendations but I don't know what the effect of this is, can anyone tell me?)
-I've seen "burned" (destructive dissolution) parts and I wouldn't call these burned, but not sure.
-Results seem to be the same regardless of voltage vs current anodizing. Patchy appearance
Can anyone make any suggestions that would allow me to achieve a more uniform oxide layer? What variables should I be looking at? Thanks for any assistance, would be willing to pay a consultant who could solve this problem.
Joseph G.Finishing Engineer - Greenboro , North Carolina
A. Joe, you may want to try using aluminum racks. The current travels greater through the aluminum than titanium. We almost always use aluminum racks on any 2000 material. The task of hardcoating 2024 can be quite difficult, there are very few shops that will hard coat 2024 with out a disclosure agreement due to the difficulty.
Casey Weizel, PresidentForesight Finishing LLC

- Tempe, Arizona

2004
Joe, your prep process for 2024 must not include a caustic etch, and must include a desmut that contains fluoride/bromide (Sanchem 1000 in nitric acid works). You should not prep 2024 the same way as 6061. Also, the temp during anodization must be held at 32 °F: if the temperature rises, the hard coat will get a patchy gray appearance instead of the black color that is desirable.
Khara EdlerNew Jersey, USA
July 5, 2012
Q. We are running a 2024 part for black hardcoat.
Cleaner, rinse, desmut , rinse - Hardcoat.
After hardcoat and before dye we see areas that are coated lighter than the rest of the part - In the same spots on every part.
The dye does not take in these areas, but it is non-conductive so it is anodized. Has anyone every seen this before.
Bob Bramson- Kenilworth, New Jersey, USA
June 28, 2012
A. 18% by wt or volume? For heat treated 2024, take the free acid up to 220 gm/L.
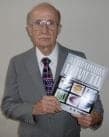
Robert H Probert
Robert H Probert Technical Services

Garner, North Carolina
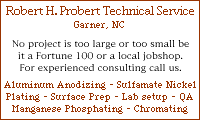
July 3, 2012
A. Hi Bob, Critical process step for 2024 is the desmut - it must remove surface oxidation without etching aluminum, and it should etch copper. If the desmut does not contain fluoride/bromide or the time in the desmut is insufficient, copper may be left on the surface. The fact that the anodizing does not take in the same spots on each part may be due to machining bringing copper inclusions to surface in a non-uniform pattern.
Another possible pattern issue could be residues that are left in a pattern resulting from the machining process. The anodizing pattern might result from poor cleaning of these areas. Caustic etch should be avoided for 2024, and this might lead to insufficient cleaning unless time in the soap, desmut time and desmut chemistry compensates.
To check for material patterns, try doing a conversion coat (Alodine) on the bare aluminum part and see if similar patterns appear. Chromate conversion is even more sensitive to copper than anodizing.
Non-uniform pattern may also be caused by tooling with too few connections or other geometrical issue affecting the current flow. Is the non-anodized area centered on a flat surface or on an edge. Check current density through tooling bolt cross section. Add more tooling bolts/clamps to see if pattern changes.
- New Jersey, USA
July 5, 2012
Q, A, or Comment on THIS thread -or- Start a NEW Thread