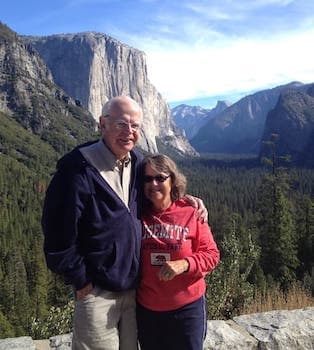
Curated with aloha by
Ted Mooney, P.E. RET
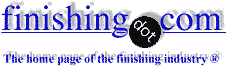
The authoritative public forum
for Metal Finishing 1989-2025
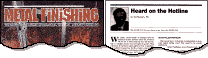
-----
SPRING BREAKING AFTER ZINC PLATING
I have designed a metal "L" shape leaf spring: SAE1060 steel 0.8mm thick. Heat treatment: 40-42 HRc Finish: zinc plating per qq-z-352 types 1 class 3 (hydrogen embattlement relief) After coating the springs are breaking in the bending corner of the"L" shape after a few seconds Or a few minutes of constant bending force. This dose not happens before the coating takes place. Can anyone advise what is the problem? Can I use any other coating or pasivasion process?
Pini shifris- TEL-AVIV , ISRAEL
1999
The hydrogen embrittlement relief is probably not being done correctly or is not being done soon enough. Try to get the springs into the oven immediately after plating and see if that fixes the problem.
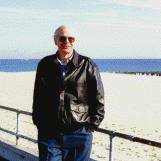
Ted Mooney, P.E.
Striving to live Aloha
finishing.com - Pine Beach, New Jersey
Also, keep your acid activation to an absolute minimum. Do not rack the springs where it requires any flexing to rack or derack. Minor flex before a proper bake may cause a failure.
James Watts- Navarre, Florida
1999
Try to eliminate as many attributes as possible. Combination of stress and hydrogen embrittlement can cause cracking. To eliminate the stress prebake you parts @ 375 °F for 3-4 hours. Is the part being electrocleaned? If so make sure that its anodic cleaning only, or try a mechanical clean (blast). The other area to evaluate is the plating process. Is the bath in compliance with the limitations for brighteners, are operators utilizing high current to try to meet production? The embrittlement bake after should be 375 °F for up to 24 hours and should be done ASAP after plating. Try the different combinations and good luck.
Tim Martinplating shop - Springfield, Massachusetts
1999
Q, A, or Comment on THIS thread -or- Start a NEW Thread