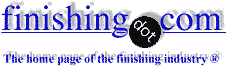
-----
Nickel Plate Repair
1999
Kollmorgen manufactures equipment used in a salt-water environment. Many parts are made of aluminum and nickel-plated (Electroless Nickel Plate per MIL-C-26074 [⇦ this spec on DLA] ) for corrosion resistance. The outside surfaces of the parts are painted; however, the mating flanges on these parts are machined to an RMS 32 finish and held to a 0.002î flatness requirement. An o-ring mates to this surface and the parts are pressurized (7 lbs. of dry nitrogen). The flanged surface is coated with DC-111 silicone grease for corrosion resistance. After the units have been in service for a varying amount of time, they are returned to Kollmorgen for repair, refurbishment, or upgrades. Many of the nickel-plated surface areas have been compromised, exposing bare aluminum. When salt water contacts the aluminum, it quickly corrodes. This degrades the surface finish of the parts, allowing the pressure boundary to be violated. Kollmorgen is looking for a method to patch these corroded areas. The task becomes difficult as we approach these issues:
- The material used needs to be electrically conductive.
- Due to the size of the pits in the returned parts, the material used will vary in thickness from 0.001î to 0.020î thick, and, if subsequent smoothing operations are required to ensure the flatness and surface finish requirements, may have a feathered edge.
- The material used to repair needs to adhere to the aluminum and often the surrounding nickel area.
- The material used needs to be resistant to corrosion due to salt water.
- Northampton, Massachusetts
Mashia- These parts must be very expensive to produce. What you are looking for reminds me of some automotive restoration type work that I used to do in the 70's. Some of the parts I used to get were in truly unbelievable condition, but the owner of the vehicle would lose thousands of dollars in value if reproduction parts were used. First of all, you must find a way to clean the exposed aluminum and then produce a conductive (platable) coating on this aluminum. There are several ways to achieve this, but protecting the geometry and finish of the rest of the part will be a consideration. After you have done this, nickel can be plated on using a "brush" plating process. The characteristics of this type of process, and the nickel layer that it produces, make it very suitable for the work you are considering. Nickel can be built up very fast. The nickel deposited is very ductile with very little stress in the deposit. The nickel so deposited can be ground, machined, brush finished, or polished, and can feather into an existing nickel deposit very nicely. Commercial equipment used for this type of restoration work usually consists of a lathe specially fitted for the process. It seems to me that flange faces are a good candidate for this type of work if you can properly mount the part. I have used this type of process with nickel and with copper. There is (or was) a company named Selectron, which sold the equipment and chemicals for this process, as well as supplying training and certification for same. As part of the certification process, the prospect must plate 0.001" thick nickel on a 1" square coupon in 30 sec., and bend the coupon 180 degrees without visible cracking. I hope this information helps. Patrick Marks
Patrick Marks- Chandler, Arizona
1999
Brush plating is a good way to repair these components, Brush plating has been used by the navy for years for repair of submarine components also subjected to the harsh environment of the ocean. This process can be used in house as the parts come in.
David Crocker- Valencia, California
1999
Q, A, or Comment on THIS thread -or- Start a NEW Thread