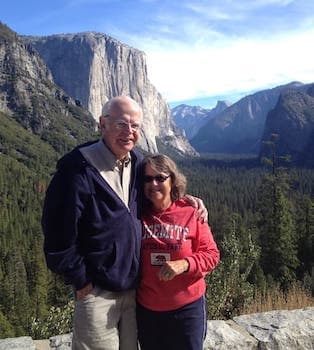
Curated with aloha by
Ted Mooney, P.E. RET
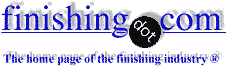
The authoritative public forum
for Metal Finishing 1989-2025
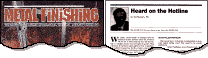
-----
Improve Booth
I am the responsible for the Department of Engineering and my actual task is improving the performance of the booth. We are in the auto industry, we make roof luggage for Opel (Astra, Corsa, etc.) and we started this activity in 1997. We are trying to improve maintenance plans and operations plans. If any one is in the same position, was or will be, please contact me.
Antonio Teixeira- Carregado - Portugal
1999
1999
Antonio!, The main functions of any booth is to contain oversprayed material and to recycle the powder material for re-use. Not all booths are designed or utilized to recycle the powder. Efficient recovery of over-sprayed material is one of the most important aspects of an electrostatic powder spray system.Air is pulsed from the inside of the filter periodically to keep the filter surface area clean of powder. The powder is forced off the filter or cartridge and drops to a collection device. I assume that you are having some form of problem related to one of these functions of the booth.Air movement is the primary tool in virtually all methods of collecting over-sprayed powder materials. Collection systems must address the following requirements:
Comfort and convenience to the worker during system operation
Ease and time of installation
Safety and insurance agency approval regulation, particularly in the areas of fire and explosion prevention
Minimize of operational noise levels for worker protection
Control of air movement in spray zones for control of application transfer efficiencies
Ease and time of color changes
Efficient separation of powder from air volumes
Containment of over-spray in order to limit worker exposure to limit worker exposure and minimize housekeeping efforts. The fan creates airflow through a powder booth. The face velocity or air rate of air coming across the opening of the booth is critically important in maintaining proper powder collection within the booth itself. The face velocity required to keep powder in the booth should be no less than 100 feet per minute. This can be measured with a face velocity meter. In any given opening, the average should be 100fpm or more. Anything less than 1100 fpm will enable powder to escape from these openings. The fan and cartridge area should be equipped with water manometer gauges to measure when the filters become blinded with powder fines and fail to draw adequately. You can then clean or install new filters. The calculation for figuring airflow required is:
Multiply each opening on the booth Height x Width Remember! Include "ALL" openings including the conveyor slot, automatic gun slot, access doors, and parts entrances and exits.
Add the total area and multiply this by the face velocity needed. Start with at least 120 fpm.
This will give you the cubic feet per minute the fan needs to provide. Example / Total opening area = 100 sq. ft. x 120 fpm = 12,000 cfm required. Per 14 guns The figure of 12,000 CFM is what the fan needs to produce to create sufficient average face velocity of 120 fpm. You should always start with more face velocity built into the system because as time goes on, the filters will become blinded and face velocity reduced. Never go over 150 fpm or the probability is that powder will be drawn into the collection hopper before it has a chance to be applied to a part. Try to eliminate large openings in any one area of the booth because it will tend to make a large airflow disturbance within the booth. Bob Utech
![]() Bob Utech Benson, Minnesota |
![]() Ed. note: Bob is the author of: "High Performance powder Coating" on eBay or AbeBooks or Amazon [affil links] |
2007
Mr. Eutech,
I purchased your book Guide To High Performance Powdercoating and I use it like a bible...I am dealing with a group that has had numerous coating issues as well as pretreatment issues.
I have been arguing for them to coat thru windows in the booth instead of standing inside the booth area. They have a side cartridge system for reclaim (if desired). They have two tub like containers that the painters are using for stools to sit on and have recently put linoleum, yes linoleum, down on the floor rather than re-sealing the silicone areas on the floor that were leaking out powder in the booth. I was beside myself on this one and I tried to make them understand interruption of air flow and contamination issues that go along with this drastic step that they have taken. Can you please address these issues for me...my words seem to fall on deaf ears or either they question my knowledge concerning the possibilities of their actions...I would certainly appreciate your input.
Thanks,
process analyst - Indianapolis, IN, USA
They have even talked to a vendor about buying new paint guns due to their issues of reject coatings. My argument has been to hold up on purchasing the new guns and spend the money to train the painters how to properly use what they have for now. Teach them about transfer efficiency, and how to accomplish that. They paint everything with the same settings, same nozzle, same pressures from a 10 lb large massive piece to a 12 gauge 2" piece. They go over the part as much as 5-6 passes with the gun 2" from the piece. They respray parts on the same settings! They have never been formerly trained on how to use the equipment. I would think that it would be better to spend the money to train one painter and have him come back and train the other rather than the new gun approach yet. I have dealt with powder coating & pretreatment from past employ for about 12 years. I just have never seen alot of the things I see them do, during all my years around powdercoating but I know alot of what they do are incorrect applications. Their pretreatment was pitiful when I began troubleshooting their area...maybe 30% spray power, at most, in each of their stages due to blocked nozzles and risers from years of neglect. They have been a hard group to turn around in their way of doing things. Only when they came down with a bad case of anerobic bacteria within the system...did I get their attention on cleaning up their system. Now paint area has been another issue with "old school" attitudes. Very frustrating.
Cindy Lynch- Indianapolis, IN, USA
2007
2007
Cindy,
You are not going to win this battle. It will take direct guidance from the main man to see change, and you are the new kid on the street. Three guesses who will be listened to the most.
I would start an immediate search for another position, even if it was less pay or more in the manual labor mode. You will grow old and frustrated in this company.
My blood pressure dropped over 20 points when I left my last position.
- Navarre, Florida
2007
Thank you for the response...I know you are probably right...It is hard to change old habits like a I am dealing with. The pretreat and paint are not the only aspects of my job...I also wear many other hats:
**Hazmat & MSDS Programs
**Backflow Certification
**Salt Spray & Coating Weight Testing
I am a certified welder and take care of their welder re-certs every year for their ISO program. I also create many of their forms and work instructions for ISO.
I am to the point of picking my battles and just walking away from any involvement with pretreat and paint (and leave them to their own demise). But then I should definitely be looking at another job
(under those terms) because we won't stay in business very long if we keep doing things the way we are doing them now. Outside of the headaches that seem to generate from the problems with that specific area; I enjoy my other duties and the people that I work with. I just know if we don't start seriously looking at how we are going to improve to compete with other business' we all may be looking for new jobs.
Thanks again for responding...advice well noted.
Cindy
- Indianapolis, IN, USA
2007
Cindy, I believe your doing what I would do in the same situation. In almost all situations other than batch booths, the paint applicator/operator should not be standing within the booth itself. One of the major reasons is because the amount of contamination being brought into the application/booth environment is prohibitive. Many companies take great pain in making sure they reduce debris and contamination into their finished product. Why bring in this contamination which is sure to add to your rejection rate? I also do not see why any employee should be sitting while applying powdercoat. It sets precedence that the work is not important.
I think before any equipment is purchased, the equipment you have needs to be operating at it's optimum and the painters need to be trained to operate and maintain the equipment. Thats where I usually come in.
From time to time, I find companies where management has purchased a paint system and doesn't understand that the system needs to be controlled. This includes pretreatment, guns, booth and painters. Without control of the processes, your rejection rates rise dramatically. New equipment may not produce any better product than you produce now, especially if the employees don't understand the theory of powdercoating and troubleshooting problems.
Remember, if your not attempting to be the best, your competition is!...Bob
![]() Bob Utech Benson, Minnesota |
![]() Ed. note: Bob is the author of: "High Performance powder Coating" on eBay or AbeBooks or Amazon [affil links] |
2007
Hi,Cindy Lynch
Today I have gone thr' your letter addressed to Mr.BOB UTECH.His book will certainly guide you in a way.
Reading to the malpractices adopted by the group you are dealing with are really horrible.
Around three years back I was in agreement to improve the conveyorized liquid paint shop having same attitudes (you have said in your letter).I then believed that every thing could be set right once the attitudes of painters,supervisors and maintenance team are changed.So I started to deal with every individual separately.Educated them and explained the importance of adopting standard practices(which ultimately were to result in reducing process time,fatigue,all consumption level like power,water,paint etc.)Sometimes I had to take spray gun in hand and train the painters for std.style of painting(optimizations of air,paint pressures,fan patterns).I also got involved maintenance team in every activity in paint shop.THIS TOOK ME ALMOST THREE MONTHS.After three months I started taking on everybody who I found culprit in not following and maintaining std. practices.Believe me I got OWNER and directors on the shop floor when needed and did not spared anybody.After six months, costing head rang me up and told me that operating cost of the paint shop has been drastically reduced.Productivity was increased by more than 33%.And of course quality product.This was the result.
So pleasedon't get upset. Deal with lowest member of the group and do not spare even owner if improvements are really needed.
I hope you will find the "matter" in the letter.
Regards.
- PUNE, MAHARASHTRA , INDIA
Thanks for the response. It looks like the group in place on that area has got the "go ahead" on the new paint gun/equipment...not necessarily the training. If I was going to go that far and spend that much money with a company...I believe I would have insisted the train one of my painters on painting technique (since they offer training) as part of the purchase package. I'd say, if they wanted the sale bad enough, they might consider it. Word is, they have realized a 10% improvement in savings...in what area I am not sure but can assume they are referring to savings in paint usage since they have finally started weighing powder to track usage...something that I have tried for 2 years to get them to do because they spray to waste on everything (including all day runs of the same color). We have reclaim abilities...they just don't do it to my amazement. With the equipment we have and some of the long color runs we have, we could realize a reclaim ratio of at least 85% as long as we were spraying smart but that is not even being considered. I have pretty much stepped aside and let that group run with it. Until management sees the benefit of any proposals I have made or the legitimacy in those proposals, I was just fighting a losing battle. The one guy was right...it was a battle I wasn't going to win...I don't seem to have the support needed for such a project. Thanks again for your input...I always appreciate it...its how I learn.
Cindy
- Indianapolis, IN, USA
2007
Q, A, or Comment on THIS thread -or- Start a NEW Thread