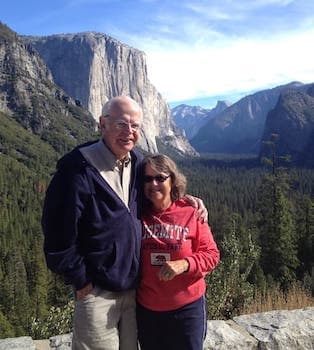
Curated with aloha by
Ted Mooney, P.E. RET
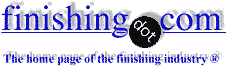
The authoritative public forum
for Metal Finishing 1989-2025
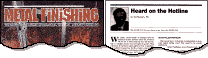
-----
Help us Please!
Hi, my name is Laura . I am a sophomore at UNCCharlotte. My engineering class has been assigned a team project to design an electroplating finishing facility for an urban hydroponics gardening center stations. We have to know what goes into chromium plating a luminare reflector and nickel plating an irrigation nozzle. We also have to know about anodizing structural supports. Is there anyway you could possibly send me some information on how the whole electroplating process works and mainly information on chromium plating.(That is my area of research). Thank you very much for your time,
Laura O [surname deleted for privacy by Editor]UNCCharlotte Engineering 1201 Team - Charlotte, North Carolina
1998
Dear Ms. Overcash:
I looked at your homepage, and compliment your school and team for a pretty cool way to undertake a project!
Let me start by saying that a real hydroponics gardening center would be EXTREMELY unlikely to establish a plating shop. Nearly all businesses, even manufacturing intensive businesses, now send their plating to jobshops. The problem is that in any enterprise that conducts plating operations, the environmental demands and threats from the agencies soon consume 100% of the attention of every executive, so it becomes difficult if not impossible to conduct any other business if you operate a plating department. Thus there has been a nearly 100% trend for captive shops to shut down their plating departments and farm the work out to plating jobshops. I may be overstating a slight bit, but the trend is overwhelming.
While a reflector could be chrome plated, I doubt that most are. Rather, they are usually 'bright dipped & anodized' aluminum because aluminum is a much better reflector than chromium. There is a strong trend to steer away from chromium when possible because the plating solution is carcinogenic, so I suggest you consider doing so.
You will need a few books; the Metal Finishing Guidebook and the Electroplating Engineering Handbook ⇦ this on eBay, AbeBooks, or Amazon [affil links] may be available from your school library; more info is on our booklist. Hopefully a reader from a local jobshop will invite your team to tour their facility (or if you're a good salesperson maybe you can call some plating shops and wrangle an invitation); visiting a shop is probably the best way you can really learn enough to start realistic planning in a realistic time frame.
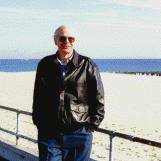
Ted Mooney, P.E.
Striving to live Aloha
finishing.com - Pine Beach, New Jersey
Hi Laura,
What Ted says is stated a bit strong, but is certainly true.
His sources referred to are about as good as it gets. For serious look at chrome, get Handbook of Hard Chromium Plating by Robert Guffie. It is a smaller book that is quite readable. If you like painful reading, there is Chromium Plating by Weiner and Walmsley.
I will not do your work for you, but I will offer to critically review your drafts if you would like.
James Watts- Navarre, Florida
1999
Dear Sir,
My name is Carly King. I am writing you in regards to an assignment that my fellow classmates and I were assigned, in our Intro. to Engineering class, here at UNCC. Our project is as followed.
1. Structural Supports will consist of extruded aluminum shapes with a nominal cross section of 2" square. Each growing station will use 130 feet of this material in pieces ranging from 24" to 72" in length.
Structural supports must be anodized to a total coating thickness of 0.002 inch.
2.Luminare Reflectors will consist of low-carbon sheet steel formed into the nominal shape of truncated cone with a base diameter of 16", an apex diameter of 4" and a height of 14". Each growing station will use 6 luminare reflector must be chromium plated to a minimum thickness of 0.0005 inch.
3.Irrigation Nozzles will consist of machined brass fittings one inch in diameter and one inch in length. Each growing station requires 24 irrigation nozzles. Each nozzle must be nickel plated to a nominal thickness of .001 inch.
Parts will be received from the fabricating facility with a light coating of oil or grease. Structural supports and irrigation nozzles may have small quantities of metal chips present as will as the surface coating.
The specified production levels should be achieved with operation using only one supervised eight hour daytime shift, five days of each week. It is permissible to operate across a longer period of time if appropriate provisions are made for autonomous operation. In estimating costs of operation, the annual total cost of compensation for personnel should be taken from the following:
- -Unskilled labor $60,000
- -Process engineer $160,000
- -Analytical chemist $140,000
- -Plating technician $90,000
1999
I hope your school isn't raising expectations a bit too high; and it's no wonder teachers think they're underpaid when they greatly overestimate the wages of others :-)
I'm a licensed P.E. with decades of experience, Carly -- can I land that $160,000 Process Engineer position, or even the Plating technician job, instead of working at about the Unskilled Labor wage here at finishing.com?
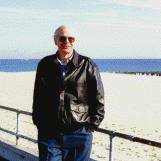
Ted Mooney, P.E.
Striving to live Aloha
finishing.com - Pine Beach, New Jersey
Q, A, or Comment on THIS thread -or- Start a NEW Thread