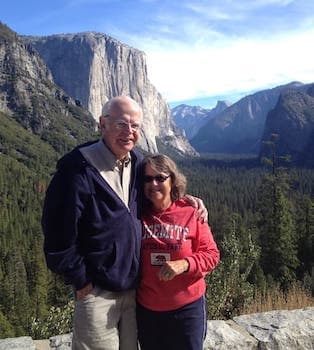
Curated with aloha by
Ted Mooney, P.E. RET
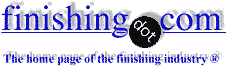
The authoritative public forum
for Metal Finishing 1989-2025
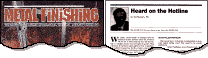
-----
Coatings for corrosion protection of fasteners
Q. I am an architect in Honolulu. We have a residential townhouse project under construction within 1/2 mile of the ocean, leeward of the prevailing wind. The contractor has submitted a substitution request to install the siding fasteners with Aericote ® 1000 coating, which provides 1000 hour salt spray corrosion protection. I am unfamiliar with the test standards for corrosion and do not have a feel for the amount of protection 1000 hours will provide. It appears to be substantial. The manufacturer claims the material is 10x more resistant to corrosion than ordinary galvanized fasteners. I am aware of a structure that was built over the ocean shoreline. The fasteners used were the galvanized nails. Rust damage appeared within the first year of construction. Do these fasteners, tested to 1000 hours of salt spray protection, appear to be appropriate for the intended use? Seems ok to me, but I'm just looking for some agreement from someone with experience in this area! .
Aloha, Mahalo,
architect - Honolulu, Hawaii, USA
2004
A. Aloha, Peter.
Salt spray testing is a QA measure to insure that a process hasn't gone South; it's not a performance scale against which to compare one type of coating to another. The applicator doing this Aericote ® 1000 process is supposed to be regularly demonstrating that they are still getting 1000 hours of salt spray resistance, as evidence that they are applying the coating correctly -- but that does not imply that the coating will last shorter or longer than another coating with a salt spray rating of 500 hours or 2000 hours.
There is no constant you can apply to convert hours of salt spray resistance into years of real-world corrosion resistance. For one thing, galvanized fasteners react with carbon dioxide in the air, over the years, to form adherent, glassy zinc carbonate skins which are almost impervious to ongoing corrosion. Galvanized coatings have lasted 75 to 100 years in the real world with zero maintenance -- but they perform poorly in salt spray chambers where this skin cannot form. Are there any new coatings with more real-world corrosion resistance than heavy hot-dip galvanized coatings? I doubt it, but there is no way to know until 75 or 100 years pass :-)
More bad news is that not only is the 10x comparison misleading for the above reason, but it is apparently a comparison with zinc electroplated fasteners with a 96-hour salt spray resistance, not hot dip galvanized fasteners. Galvanized coatings are applied by hot dipping and are much thicker and more corrosion resistant than electroplated coatings. I would lean towards guessing that those 'galvanized' nails you had trouble with were actually zinc electroplated (sometimes called 'electrogalvanized' as a euphemism to ride the coat tails of hot dip galvanizing).
An advantage of galvanized coatings compared to paint is that they are sacrificial coatings rather than barrier layer coatings. A scratch in a galvanized coating is of little consequence because the zinc will preferentially corrode to protect the exposed steel, whereas a scratch in a barrier layer paint coating means that the exposed steel will rust.
Now for the good news though. Specialty coatings like Aericote ® 1000 are not simple paints, but zinc-rich or aluminum-rich coatings that can provide sacrificial protection as well as the barrier layer protection. I am not specifically familiar with Aericote, but I would be open to accepting their claim that it is superior to galvanizing in a wet and salty environment (where galvanized coatings have difficulty building those glassy carbonate reaction products). Good luck!
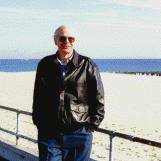
Ted Mooney, P.E.
Striving to live Aloha
finishing.com - Pine Beach, New Jersey
2003
Q. Thanks Ted for the insight. I am inclined to approve the substitution. It seems to be a win-win proposition for both the owner and the contractor. Is 1000 hours of salt spray testing on the high end of the testing spectrum for fasteners? What kind of items, equipment or conditions would typically need that type of protection?
Peter BH Maertensarchitecture - Honolulu, Hawaii USA
2004
A. 1000 hours salt spray is a lot, Peter. As I mentioned, zinc plating (with yellow chromate) is considered good for only 96 or 192 hours. And even galvanized coatings don't go beyond a few hundred hours. But again, please don't try to predict real world life from salt spray ratings! They make coatings which offer important galvanic protection (like galvanizing) look bad, and coatings which completely lack it (like paints) look good :-)
I think the better answer is that many of these zinc-rich and aluminum-rich specialty fastener coatings have seemed to prove themselves in the real world.
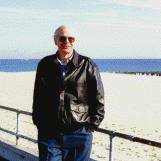
Ted Mooney, P.E.
Striving to live Aloha
finishing.com - Pine Beach, New Jersey
2003
Q. Where can I find a good compendium of corrosion protection ratings for different types of platings and coatings over steel fasteners. I'm an engineer designing new products and need to choose or spec the right fasteners for outdoor use.
Kevin Walters- Agawam, Massachusetts USA
April 15, 2013
A. Hi Kevin. It's a complicated issue, and depends whether you are talking about machine screws or deck fasteners, and what materials you are joining with the fasteners; machine screws are usually limited to metallic coatings because organic coatings are too weak, too thick, not sufficiently adherent, and clog the threads making accurate torquing difficult. But a brief intro on corrosion resistance would be:
Coatings can afford either barrier layer protection or cathodic protection (or both).
- Paints offer barrier layer protection: once there is a scratch, that area will rust.
- Zinc plating and galvanizing offer cathodic protection, i.e., they sacrifice themselves to protect the steel fastener. You can look up the "sea water series" and see that there are a few other metals like cadmium and aluminum that can offer cathodic protection to steel. You can also tailor alloy platings like zinc-cobalt, zinc-nickel, zinc-iron, and tin-zinc to both offer cathodic protection at carefully controlled potentials and to build tight adherent corrosion products to afford maximum protection; these will almost always be better than plain zinc electroplating.
- Most metal platings, like nickel plating, do not offer good corrosion protection because they are on the wrong side of the sea water series from steel. If the barrier is perforated (via porosity or a scratch) the corrosion of the underlying steel will be greatly accelerated by the steel trying to cathodically protect the coating. You may have seen decades-old cars in junkyards with bumpers of curling nickel chrome plating and no steel left, as the steel rusted away to sacrificially protect the plating.
- A zinc rich paint may provide a bit of both protections, as will zinc plating or galvanizing followed by paint.
If you can tell us what kind of products you are talking about, we may be able to be more specific. Good luck!
Regards,
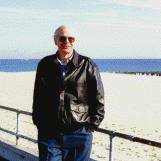
Ted Mooney, P.E.
Striving to live Aloha
finishing.com - Pine Beach, New Jersey
Q, A, or Comment on THIS thread -or- Start a NEW Thread