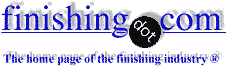
-----
Anodizing Automotive Brightwork Q&A's
2002
Q. 5252 H25 Aluminum one-side bright .040 thick is stamped and buffed, bright dip anodized, powder paint clearcoated. We are experiencing shiny (bright) speckles throughout the surface of the part which is not seen until the part is heated in our powder paint pre-treatment.
After clear-coat, the speckles (streaks of shiny slivers) are evident.
Dickey Thompson- Newberry, South Carolina
A. 1. Your aluminum alloy is about 4.5 % Magnesium. All inorganic salts of Magnesium are white. Anodizing only control oxidizes pure aluminum, and leaves the magnesium on the surface probably in your case as Magnesium sulphate, and Epson Salts are white.
2. The last time I saw white specs under clear powder paint in South Carolina, I stopped by the grocery store and picked up some distilled water and a squirt bottle. Then I sprayed the parts at the end of the line with pure water. Guess what, the white spots were gone. Then we learned that the local water authority had switched lakes and at the same time our D.I. unit went down -- the calcium and magnesium were coming thru and both make white salt.
3. Go to Section 4 of finishing.com and locate my paper on "White Spots". Let us hear from you.
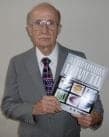
Robert H Probert
Robert H Probert Technical Services

Garner, North Carolina
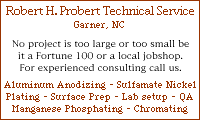
2002
Multiple threads merged: please forgive chronology errors and repetition 🙂
Q. I am a small job shop anodizer (approx. 1000-3000 parts per week). Generally speaking we have very few problems in the course of a year with our process. We do type II @ type III in the same tank, obviously under different conditions, and we get very good results. Why can't I get a bright clear finish on automotive trim. A typical situation is that a customer who is restoring a car will have the trim stripped of the old anodizing, repaired, and then mechanically repolished before bringing it to us. Even 10 minute coatings dull the piece enough that it's not as bright as it originally was. I've tried a 2 minute flash coating but it gets a rainbow appearance and I don't think that amount of coating will give it very much protection in the elements. How do the OEM's do it? Any tips or suggestions would be appreciated. Our anodizing solution is sulfuric 180 G/L with 2% additive Polished parts only get degrease and deoxize they still look shiny before going into anodizing tank. We use a mid temp seal.
Hope this info helps, thanks,
job shop anodizer - St. Albert, Alberta, Canada
2004
Treatment &
Finishing of
Aluminium and
Its Alloys"
by Wernick, Pinner
& Sheasby
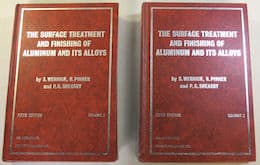
on eBay or Amazon
or AbeBooks
(affil link)
A. Based on the limited info, my suggestion is to try anodizing at a faster rate. Brightness decreases with time in the tank, and 10 minutes sounds excessive. Work near the upper current density limit given by the anodize additive vendor. Typically, anodic coatings of 0.3-0.5 mils (7.7-12.7 microns) are used for exterior trim. Less may be acceptable for a restorer who keeps things well waxed.
You may wish to begin by experimenting on bright anodizing alloys such as 5252, 5457, 5657 and 6463 in cold rolled or extruded condition (not annealed).
- Goleta, California

Rest in peace, Ken. Thank you for your hard work which the finishing world, and we at finishing.com, continue to benefit from.
2004
Bending and Anodizing Aluminum
Q. I am hot bending a piece of aluminium flat bar and wish to anodize it after this. Can you recommend a particular type of alloy which is suited to anodizing after this process?
David Irwinfurniture designer - Newcastle Upon Tyne, England
July 30, 2009
A. The type of aluminium you want to use for anodising is probably 5 or 6 series (i.e., 5052, 5252, 6061 or 6101. These alloys are inherently strong and ductile. Series 1 is generally classified as very soft, whilst 2 is very strong and hard. Series 3 is also strong and 4 is strong and fluid. Series 7 is very strong.
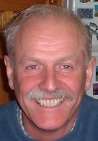
Trevor Crichton
R&D practical scientist
Chesham, Bucks, UK
August 19, 2009
For Bright Anodizing We Need 5252-H25 or Alternative
Q. We are an OEM metal stamping company, we have a few parts which call for 5252-H25 material and require a bright anodized finish. Our problem has been finding 5252-H25 in smaller quantities. We have tried 5052 but this generally leaves a dull finish compared to the original 5252-H25. Would anyone know of any alternative aluminum suitable for bright anodize? These are appearance parts and will require a mirror look.
Rick HumbertStamping Shop Manager - Morgantown, Kentucky USA
April 17, 2014
A. Far from my area of expertise, but have you tried any of the 3000 series? If I recall, that series brightens up quite well.
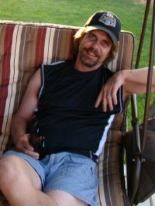
Marc Green
anodizer - Boise, Idaho
April 29, 2014
Clear anodizing of Porche 911 window frames
June 6, 2016Q. Early 1970s Porsche 911s had bight dipped and clear anodized aluminum window frames. As a plating (zinc and cadmium) restoration specialist, customers were asking me to do their frames. I have done over 100 hours of testing and the results are promising but not 100%.
I have worked with 3 professional anodizers, one of which does bright dip. Because I was able to get the de-anodized, bare aluminum frames polished to a mirror finish, their testing revealed that standard clear anodizing provided better results than bright dipping first. They said the bright dip dulled the finish slightly. Other anodizers have done similar testing with varying thicknesses of the anodized layer.
Please see this pic I have attached. From the left to right, there is .15 mil, .20 mil, factory original which is about .25 mil and a .28 mil.
What jumps out, especially in person, is the factory original, even though 40+ years old, is clearer and brighter. The other 3 are milky and streaked.
The pieces were sanded to 1000 and then polished with white compound to a mirror finish. They were gorgeous before anodizing.
I need to get the very clear, bright finish of the factory original. What can I do?

Shaun Budka
- Watertown, Massachusetts USA
9th Edition, Vol. 5
"Surface Cleaning, Finishing & Coating"
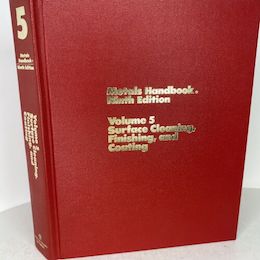
on eBay or Amazon
or AbeBooks
(affil link)
A. Hi Shaun. I would certainly expect that one out of three anodizing shops, at the least, would be technically proficient enough to solve the problem if it was solvable. Based on that -- and the previous input on this thread which we appended your inquiry to, and several related threads -- I think you may be trying to achieve the finish on an alloy which can't support it.
I am not an alloy expert but my understanding from the ASM Metals Handbook is that hard tempered 5457, 5357, 6463 and 6063 would be best, in order of decreasing quality. Good luck.
Regards,
-->----
P.S. June 9: Prompted by Willie Alexander's posting, I reread yours ... and it seems that all of these samples are your customers' from their Porsches ... so my response about you perhaps needing a different alloy sounds off track.
Q. Thank you Ted, I appreciate the quick posting. I think the solution lies in the ALZAK process. Do you or does anyone know of an anodizer on the East Coast who is offering this process?

Shaun Budka
- Watertown, Massachusetts USA
June 6, 2016
![]() |
There aren't many shops which want to put up with the fume, hazardous conditions and waste disposal problems of the R5 bright dip, but there are a few.
![]() Jeffrey Holmes, CEF Spartanburg, South Carolina June 7, 2016 Since you know the anodizing thickness of originals is brighter than even thinner anodized reworks, I think you'll have to do more work with bright dipping. Bright dipping should, properly controlled, produce a highly reflective finish. June 7, 2016 Dear Shaun, - Asansol, West Bengal, India June 7, 2016 Hi Shaun, ![]() Harry Parkes - Birmingham, UK |
I remember when the plating supply company I was with was offering acid zinc plating plus clear-coating as an alternative to chrome plating for bicycle rims. I thought they looked darned good! ... until somebody got a chrome plated wheel and put it next to them, that is, and you had to admit there was just no comparison at all :-)
That's life -- I loved Gillette Castle until I saw Falling Water; Scarlett Johansson was gorgeous until I saw a Grace Kelly re-run. It just might be that you can't get the 1970 Porsche clarity with any process that is environmentally acceptable in 2016 (nor can you get the full look of cadmium plating on classic car restorations). Best of luck with the journey though!
Regards,
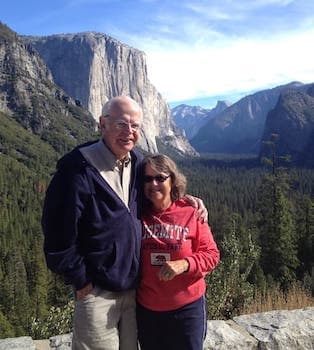
Ted Mooney, P.E. RET
Striving to live Aloha
finishing.com - Pine Beach, New Jersey
June 2016
How's that for a wide variety of answers? All are good, but Harry's strikes me as the most likely description of the overall situation. Things tend to look fine until they're compared to something which looks better :-)
A. Shaun
If I read you post correctly, you are trying to re-anodize the original window frames. I would think the pretreatment is effective, the buffing and bright-dip, but the anodize is what is causing the hazy finish. I believe you will need to alter the operating conditions to achieve a 'clearer' anodize. I would try a cooler bath temperature 63 - 65 °F, 15 - 18% by weight acid, and 9 - 10 ASF current density.
- Green Mountain Falls, Colorado
June 7, 2016
A. To add to what Willie Alexander said, I've red this exact thing in one of the anodizing related books or publications, can't recall where though
About the "streaks", they look to me not to be related to extrusion at all, but rather sanding marks from the early grits used to remove scratches (some rotary "witness marks" are visible also), thus I would recommend, after stripping the old anodizing from the parts (I would use 5% phosphoric acid + chrome oxide at ~95 degrees C instead of caustic so as not to deepen the scratches), then use no coarser that 600 grit wet paper and some type of lubricant other than water (I've successfully used WD-40
⇦ on
eBay
or
Amazon [affil links]
, I simply had this at hand) to sand the deep scratches out, and do this "across" the part, then use 800, and 1000, and maybe even 1500, each time go across previous sanding direction (otherwise you will not notice that you haven't sanded out marks left by previous grit), after last paper you can start to polish the part, and use at least 2 grits to do that aswell - all these steps are required on aluminum, since it is so soft, going from, lets say 320/400 to 800 and then paste, there is a high chance you will simply "smudge" and level deep scratches left by coarse grits, and this is exactly the reason you see those marks later after anodizing - because the smudged/mirror-polished top layer is being converted to oxide revealing your early sanding marks.
Restoring something like this is quite difficult and laboursome, much more than when the new parts were made at he factory - simply because they didn't have to deal with such defects and required less polishing, mechanical or (electro)chemical.
- Riga, Latvia
June 10, 2016
June 16, 2016
Q. Hello Everyone,
Thank you for all the great input here!
My apologies for the late reply, I've been swamped with work and was testing out a new shop, Summit in Pawtucket, RI, for bright dip. Results were extremely disappointing. They said it's because their recipe is for industrial bright dip.
It looks like I will have build my own bright dip and anodizing solution in-house.
How would I go about creating an in-house bright dip and anodizing infrastructure? I would be happy to pay a consulting fee to get me up and running, quickly.
Thank you

Shaun Budka
- Watertown, Massachusetts USA
"It looks like I will have build my own bright dip and anodizing solution in-house."
Not wanting to rain on your parade, but the investment in time, technical knowledge, equipment, permits and environmental compliance to set up a bright dip and anodizing operation, even at a minimal level would cost as much as a trailer load of restored Porches.
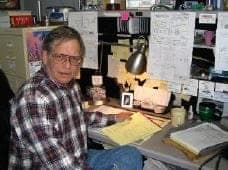
Jeffrey Holmes, CEF
Spartanburg, South Carolina
October 4, 2016
Q. I have developed some proprietary polishing techniques so I no longer need a true bright dip and then anodize process. I have been using a local anodizer and they have been great to work with. But we have a new problem: Splotches in the anodize. These look like dried water splotches. They are very hard to photograph.
Pics shown are a perfect clear anodize, a macro view of splotches and a close-up of the splotches. We have done a ton of testing and can't figure out why this is happening. The test piece here was cleaned with several rounds of acetone ⇦ on eBay or Amazon [affil links] Warning! Flammable! and was a perfect mirror before going into the anodize bath, from there sealed. Any ideas on how or why this is happening? There is no residue whatsoever from the acetone ⇦ on eBay or Amazon [affil links] Warning! Flammable! cleanings.

Shaun Budka
- Watertown, Massachusetts USA
A. Good day Shaun.
Very interesting situation.
I like the thought of using acetone instead of MEK.
Are you using a mild alkaline soak and checking for water break?
Can you inspect the frames directly after anodize, before sealing/drying?
What is the TDS, silica and chloride concentration of the seal?
What is the compressed air quality, if used used to assist in drying?
I have found 15 ppm in RO water to cause some grief.
Sometimes I can't see the forest because the trees are in the way!
Hope this helps.
Regards,
Aerotek Mfg. Ltd. - Whitby, Ontario, Canada
October 7, 2016
Q. Hi Eric,
Good questions, thank you.
I am washing frames in our washout sink using Dawn with a soft polishing cloth, rinsing vigorously with a spray hose and then blowing dry with 125 psi.
I am going to the anodizer today and will ask about inspecting. And about the seal.
We did a test yesterday that turned out perfect. Here's what I did. The polishing cloths that I use for final hand polish and cleaning are the softest things on Earth. I figured they must have silicone on them to be this soft. I washed a set with Tide Pur (extremely simple laundry detergent) twice and then rinsed 4 times in the washer. I then soaked these in isopropyl alcohol, dried and then soaked in acetone. Using these ultra-clean cloths, I cleaned the test piece with copious amounts of acetone and it came out perfect. I think the acetone was dissolving the silicone and leaving an invisible residue on the frames.
What do you think?
I did the same to a complete set of frames and the anodizer is running them today. Fingers crossed!

Shaun Budka
- Watertown, Massachusetts USA
Q. I am Bright dipping small parts that require a very shiny finish. suddenly I cannot run these anymore because the END of the part where it is racked on the titanium clip is shinier than the rest of the part. The bottom of the part rests on aluminum while Bright dipping. The bottom is not any shinier. Just the titanium clip end. This just started happening and we swear... Nothing has changed ... that we know of. Been running these parts a while now and NEVER had this issue. Help!
Brian Kolendalight Metals Corp - Jenison Michigan, United States
April 19, 2018
A. `
Hi Brian.
Forgive me for being a smart ass, but saying that things are different but unchanged is a hard point to start from.
Brightness around titanium contacts is due to local electropolishing caused by the current generated by the Al/Ti couple. It is always there to some degree but normally not noticeable. When the brightener gets out of balance, especially with respect to nitric acid, the chemical brightening generally becomes poorer (slight etching) and the electropolished area stands out.
Generally, look for anything which might pull down the chemical brightening and increases the contrast between the two.
Things on my list would be:
Nitric acid
Water content
Aluminum content
The aluminum metal - Do you have parts from previous batches to compare?
An open mind!
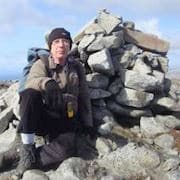
Harry Parkes
- Birmingham, UK
Ted, Thank you very much. Harry Parkes gave me some excellent advice that we tried immediately. It took TWO shifts of no nitric adds to our Bright Dip but by golly the lower nitric concentration totally took care of our problem. Thanks again. Great website.
light Metals Corp - Jenison Michigan, United States
April 30, 2018
Q, A, or Comment on THIS thread -or- Start a NEW Thread