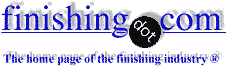
-----
Why is pot metal blistering when plated?
Having trouble with blistering when trying to put a copper strike, cyanide copper on pot metal. The hardware I run with these parts are zinc die cast and they are fine. To my knowledge pot metal should use the same process as zinc die cast. The parts are restoration parts, that we put on acid copper after cyanide copper to fill in the pits. My process now is: degrease (TCE) soak clean electroclean acid dip copper strike cyanide copper Please advise!
Steve Boutonplating foreman - Byron, Illinois, USA
2004
2003
My bet is they are an aluminum alloy which you'll need to zincate first.
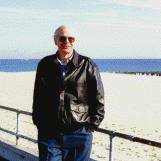
Ted Mooney, P.E.
Striving to live Aloha
finishing.com - Pine Beach, New Jersey
2004
Steve:
Restoration work is a whole different animal then plating on fresh zinc die cast.You cannot mix them. Most likely you will have to run them one at a time also. If it is old car parts it is usually zinc die cast. The problem is that they have had about 50 years of corrosion working on them. Each pit that you see has a little vein of black corrosion running deeper into the metal.
The shallow pits you can sandblast clean, the deeper pits you have to sandblast and then drill past the corrosion vein. To fill that big
"ole" drill hole you just made takes a lot of patience and time. I use a zinc alloy solder to fill all my drilled out pits.
Once they are filled you have to sand them smooth, re-solder, sand, re-solder, sand ... one last sandblast to etch and clean the surface and then you can cyanide strike. DO NOT! put your part in any kind of activator or acid salts after you sandblast it ... just rinse and go to the strike plate....live. I have had problems with the acid copper digging through my high sulphate nickel strike.
Then I go into the acid copper for a hour and a half to give me a good base to work with. You most likely will have to plate acid copper for 3 hours in 1 hour increments with sanding in between to get all the pits out and keep the detail.
- Peoria, Arizona, USA
3.8-4.2 watts nickel bath and then plate with acid copper for 1-1.5 hours. Sand, copper plate, sand, copper plate, etc. Tom Haltmeyer
- Peoria, Arizona, USA
2004
This is to finish the part of my previous reply that is cut off ... I've had problems with the acid copper getting through the high sulphate nickel strike plate that I use and causing blisters later on. Now after the initial strike plate I nickel plate for in a
Q, A, or Comment on THIS thread -or- Start a NEW Thread