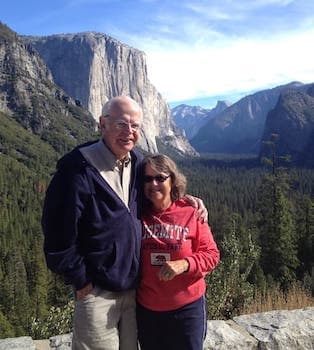
Curated with aloha by
Ted Mooney, P.E. RET
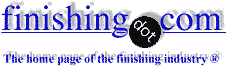
The authoritative public forum
for Metal Finishing 1989-2025
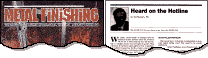
-----
White rust on zinc plated parts
Q. I have in Dec 2000 shipped a container load of zinc plated rave hooks to UK from China and my customer has came back to me that the finishes had turn to powdery and dull grey in colour. Prior to that we had the similar problems. In this shipment we had taken all necessary precautions to avoid repeated occurrence. I was told that there is no leakage and condition of container is good. Could you advise how the finishes had deteriorated to such state. The shipping time is 40 days from China which is quite cold during December via Singapore (hot & warm), Middle East (hot) to UK in Jan which is winter. Could the cold/hot/cold conditions in the container during shipment cause the problem?
Thank you for your kind attention
- Singapore
2001
A. Sir:
I have seen some horrible results from shipping zinc and zinc alloy parts over the ocean. Even with containers that are supposed to be sealed well, you get condensation patterns on the parts, combined with a salt type mist on the ocean. The way we got out of the problem was to wrap all parts thoroughly and completely in plastic with no gaps or voids. Additionally, work was done on the containers on the ships.
We were very surprised at the variances of temperature that we were told occurs in the hold of a ship.
Sincerely,
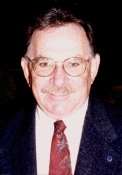

Ed Budman [dec]
- Pennsylvania
With deep sadness we advise that our good friend Ed passed away Nov. 24, 2018
2001
A. I think your products were most probably plated in Zinc and finished in Blue Chromate Correct?
The short answer is that this finish is not suitable for the application, you need a better finish, if your customer wants the blue bright finish then you must look to applying a seal to the chromate finish, i.e., a water borne acrylic lacquer, or, a metasilicate seal.
The packaging material used also needs to be considered, as does the packaging method.
A good consultant can solve your problems quickly and relatively cheaply.
Regards,

John Tenison - Woods
- Victoria Australia
2001
2001
A. Sir,
Zinc plated and yellow or blue chromate passivated parts deteriorate in storage due to various factors like condensation of moisture due to humidity changes and also due to biological fluids from, say, rodents and also due to fingerprints (especially in the case of full (yellow)iridescent passivation).
Apart from these factors, any acidity from the packaging materials may be a contributing factor. Adding packets of silica gel will be a valuable thing to protect the parts from corrosion due to condensed moisture during the sea voyage besides taking other precautions.
Thanks.
- Bangalore,KARNATAKA, India
Multiple threads merged: please forgive chronology errors and repetition 🙂
Q. Dear Sir,
We are currently using Zinc plated Yellow passivation in our product and we are exporting our product to US by sea , normally it will take 45 days to reach. After 45 days of its travel in sea our US peoples found some WHITE RUST formed in the plated parts. We want to sort out this problem completely so please advise us the reason why it occurs and how to overcome this problem ?
Thanks & Regards,
Purchase Engineer - Chennai, Tamil Nadu, India
2004
A. Zinc plating protects steel from red rust, and itself corrodes as white rust, so that is the short answer as to why it occurs, Mr. Prabhu.
But why your product is white-rusting within 45 days of sea travel is difficult to assess based on the limited input. What is the product, how is it packaged, is it guaranteed to be fully dry before packaging, what is the thickness of the zinc, what kind of salt spray hours have you been getting before white rust shows, etc.? Thanks.
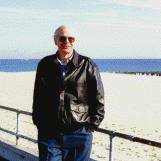
Ted Mooney, P.E.
Striving to live Aloha
finishing.com - Pine Beach, New Jersey
2004
A. Dear Mr Prabhu,
Welcome to the club of white rust problems!
For Sea shipment, this is common as I reckon that 45 days sea shipment is equal to 23 days of a Salt Spray Test.
You may want to opt for Zinc Cobalt Alloy plating with yellow passivation to avoid similar problems in future. It would be wise to test parts up to 480 hours in a SST before shipping the parts again.
Regards,
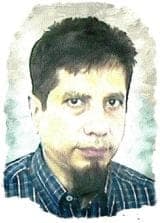
Khozem Vahaanwala
Saify Ind

Bengaluru, Karnataka, India
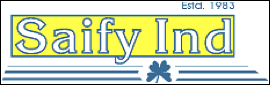
2004
A. Dear Mr Prabhu,
Your biggest problem might be the packaging. Plastic packets or sheeting is an absolute "NO". The metal will sweat and start corroding. Cardboard must not be acidic. Wooden crates with cardboard boxes and polystyrene spacers are best. Find a company that knows about packaging for zinc plating. We had a client who shipped zinc plated articles overseas for years with only 3 microns zinc and blue passivation and they shipped well. Good luck!
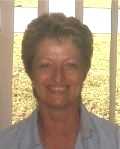
Trudy Kastner
electroplating service - Durban, KZN, South Africa
2004
Multiple threads merged: please forgive chronology errors and repetition 🙂
Protecting Passivation /Zinc plating from white rust
2005Q. We perform Zinc plating (13 microns) and yellow passivation on our carbon steel actuator components.
When we ship the materials to foreign countries by sea the parts get rusted.
Our component passed 140 hours without white rust in the salt spray test under ASTM B117.
Hence we find no problem with the quality of plating.
My Question :
Is there any other method or coating which can be useful to protect the Zinc plating from getting white rust?
Please suggest,
- Coimbatore, Tamilnadu, India
A. You can check the packing material because sometimes the packing material like plastic or glue used for cartons is interacting with the plating and thus it gives the rusting.
Harish Gurnani- AHMEDABAD, GUJARAT, India
2005
A. You can try and use top coat sealants. Plenty are available which will increase white corrosion to maximum to 200 plus hours; also improve packing material.
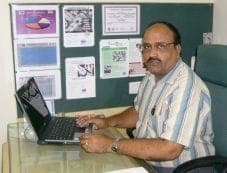
P. Gurumoorthi
electroplating process chemicals - Chennai, Tamilnadu, India
2005
A. You will most certainly find that the parts have been packed wet or that the parts have been subjected to marked changes in atmospheric conditions (humidity & temperature) and the parts have sweated during transport thus getting the parts wet in the process. If the parts were packed in plastic then this will only exacerbate the situation.
Solution is to pack the parts in a container to allow free movement of air , but keep the parts dry and protect them from extremes of temperature .
Regards,

John Tenison - Woods
- Victoria Australia
2005
A. Dear Mr Senthilnathan,
Don't send any parts by sea unless they are alloy zinc plated well is the long and short solution. NO PLASTIC packing is the second solution.
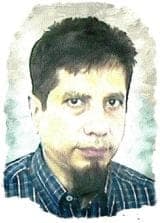
Khozem Vahaanwala
Saify Ind

Bengaluru, Karnataka, India
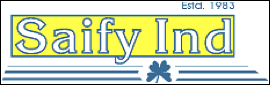
2005
A. Dear Sir,
There is a product available to seal your kind of plating. Thickness is 2/3 microns and applied by dip spin coating method. The product is Delta Coll from Doerken of Germany. Try it, it will work for your application. Best regards.
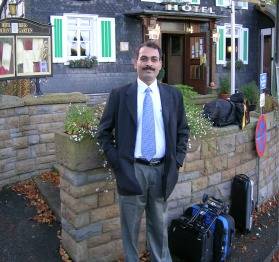
Kalyan Dhakane
Mumbai, India
2005
Q. Hi,
I have few doubts...
1) Is there any correlation available between sea shipment and salt spray analysis... with VCI packing... & without VCI packing? This is for parts just protected only with RPO - completely wiped out.
2) Is there any correlation available between Hot & humid environment Vs. Salt spray analysis? For e.g., Chennai is port city + very hot (normally range between 35 to 45 degrees). If a part is exposed to this kind of environment without any surface protection, how long it will take to rust and what is its equivalent in salt spray? 2nd, if the part is having a RPO coat then, what is the salt spray equivalent? If the part is with RPO and VCI, then, what is the salt spray equivalent?
All I meant as salt spray is normal method used in India.
- Bangalore, Karnataka, India
September 18, 2012
June 10, 2015
Q. We are facing zinc plating issue when we are sending the shipment by sea. Its transit time in sea approx. 40 days. When we send it by air it is found okay. Please advice us what should we do for this so that by sea shipment zinc plating will remain okay.
Mukesh SharmaPlating Shop Employ - Ludhiana,Punjab, India
Hi Mukesh. As you see, we appended your inquiry to earlier discussions on the topic, and the problem is perennial. Please try to review the earlier comments and either ask for clarification on things that sound applicable, or supply the data about your situation which people have indicated is necessary to offer more specifics. Thanks!
Regards,
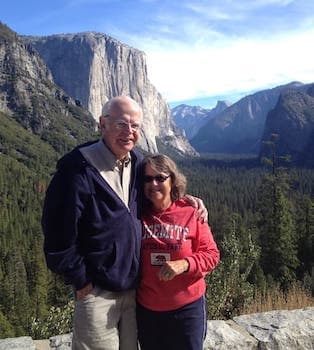
Ted Mooney, P.E. RET
Striving to live Aloha
finishing.com - Pine Beach, New Jersey
June 2015
Reaction of sodium on zinc plated steel surface?
October 26, 2018Q. We have a problem on Zinc plated (with blue passivation) parts which are packaged in corrugated Boxes which resulted in corrosion wherever parts were in contact with corrugated box. Based on Analysis it was found that The metal plated were predominantly having element Zinc with trace amounts of Sodium (Na) and Calcium (Ca). Carbon (C) and Oxygen(O) were also present.
This situation occurred during the rainy season. Does moisture or humidity affect?
- Pune Maharashtra India
A. Hi Kalyan. Zinc plating can deter corrosion but it does not absolutely prevent it. And contact with the cardboard will help keep parts wet or get them wet. The cardboard can also rub off the protective chromate with time & tide; and cardboard is often high in acid or sulfides which are corrosive.
If these are very inexpensive commodity parts, and will be in boxes for a very short time and under favorable conditions, and you are sure they are completely dry, you might get away with loose packaging in cardboard like that, but it's not the right way.
Exotic elemental analysis equipment can be useful if carefully & repeatedly walking the line hasn't disclosed the source of problems ... but it is no substitute for carefully observing and controlling what is being done.
No good decision was ever made from a swivel chair -- General George Patton :-)
Luck and Regards,
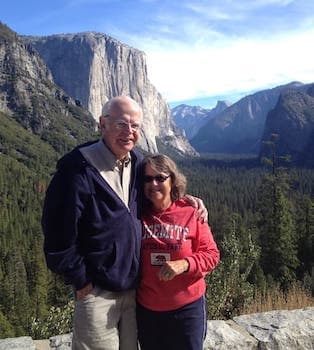
Ted Mooney, P.E. RET
Striving to live Aloha
finishing.com - Pine Beach, New Jersey
October 2018
Q. What is the chemical reaction happening?
kalyan Belsare [returning]- Pune Maharastra India
October 27, 2018
A. Hi Kalyan. If the corrosion is white, it might be white rust (zinc reacting with water and oxygen); if the corrosion is rust colored, it might be red rust (iron reacting with water and oxygen; if the corrosion is black, it might be sulfide products from the reaction of sulfides in the cardboard with the parts. Send us good pictures of the corrosion please.
But what can you now tell us from walking the line and observing? You'll have to find a different traveling companion if you wish to continue down the path of trying to analyze what is going wrong from elemental scans of the surfaces or corrosion theory rather than observation of the process ... I have taught myself little about those subjects, perhaps because I've never found any success from proceeding in that direction :-)
Regards,
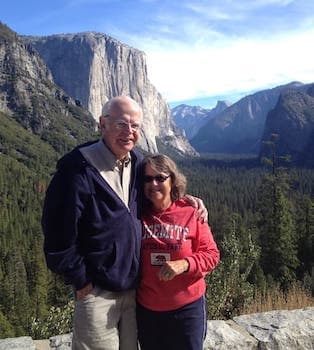
Ted Mooney, P.E. RET
Striving to live Aloha
finishing.com - Pine Beach, New Jersey
October 2018
----
Ed. note: We had enough questions about white rust on black chromated components to make it a separate subject. So if you wish to read more, please see thread 37445, "Black passivation on zinc plating gets white rust"
Q, A, or Comment on THIS thread -or- Start a NEW Thread