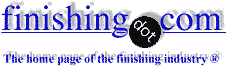
-----
Tumble polishing stainless steel
Q. Dear sir
Can you please explain to me what is the chemical composition of vibratory ball burnishing process? I am buying pale yellow color liquid from one manufacturer but I couldn't find the chemical composition, even whether it has corrosion inhibitor also.
Kindly explain to me what are the chemicals mixed in it.
Thank you
- Madurai tamilnadu, India
November 11, 2021
A. Hi Dinesh. As I understand it, vibratory ball burnishing functions primarily by causing microscopic plastic flow on the surface of the components rather than by abrading the surface off -- more analogous to shot peening than to sand blasting. Thus, one of the ingredients will be a lubricant rather than an abrasive, another will be a mild acid to deter oxidation during the treatment. Some burnishing compounds might include corrosion inhibitors and others might not.
The fact that the liquid you are using is pale yellow probably doesn't say much about its composition though.
A search through scholar.google.com or patents.google.com might offer you further guidance, but all we can offer here is generic information about such formulations. :-)
Luck & Regards,
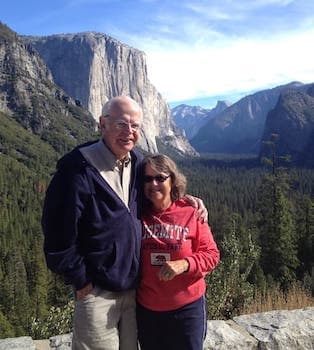
Ted Mooney, P.E. RET
Striving to live Aloha
finishing.com - Pine Beach, New Jersey
November 2021
Q. Dear sir,
I am from india and have a stainless steel articles manufacturing company. For stainless steel polishing we are using vibratory finishing machine and we polish by steel ball media and using ball burnishing chemical. It's an alkaline solution and pH level will be 9 to 9.8.
And we would like to make this alkaline solution as our own because so far we are buying it from other companies.
Therefore if it's possible to explain this alkaline liquid composition then kindly explain.
Thanking you
- Madurai tamilnadu, India
May 22, 2022
A. Hi again Dinesh. Your supplier is obligated to give you the safety data sheet for their compound, which should be helpful in attempting to reverse engineer their product. I have verified that there is indeed info on this topic at scholar.google.com and at patents.google.com. That info, plus reference to specific books and published articles is probably as far as anyone is going to be able to go in helping you develop a mildly alkaline burnishing compound for stainless steel. You're going to have to put in development efforts.
No one is likely to post "I was just fired from ... and their formulation is ...", but if they did we couldn't print it anyway :-)
Luck & Regards,
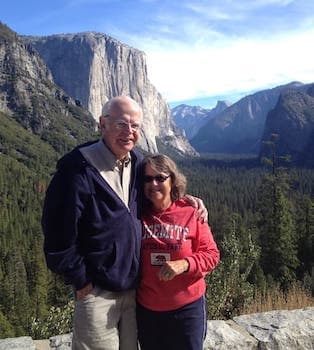
Ted Mooney, P.E. RET
Striving to live Aloha
finishing.com - Pine Beach, New Jersey
May 2022
Q. Dear sir
Many thanks for yours guide and as you said I found some books and google patents.
Would like to tell you this: I have made an alkaline composition and got enough result in ss polishing that it's getting good shine; but during the burnishing process it's making passivation layer after 10 min run, so would like to know that if I add acetic acid
⇦ on
eBay
or
Amazon [affil links] in alkaline solution then will it be solve this passivation issue?
I am looking for yours kind reply
- Madurai tamilnadu, India
May 23, 2022
A. Hi again. I do not know enough about this subject to over you formulation help; hopefully another reader will. But my question is: why is passivation a problem? Passivation is usually considered a good thing, sometimes a very necessary thing. Why do you not want passivation?
Luck & Regards,
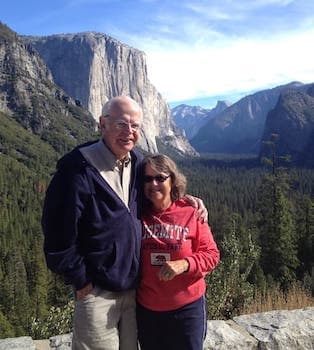
Ted Mooney, P.E. RET
Striving to live Aloha
finishing.com - Pine Beach, New Jersey
May 2022

this text gets replaced with bannerText
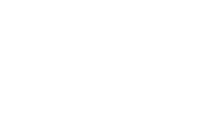
⇩ Related postings, oldest first ⇩
Q. What is recommended for tumble polishing stainless steel castings (RMS 72) to a full mirror finish? The parts are of an "S" shape with corner radii of .093, weighing approx. 5.8 oz. Hand finishing is a definite NO-NO and a waste of time. Can someone advise me?
Thanks,
JC Marcottetoolmaker - Sudbury, Ontario, Canada
2004
A. Wow! That's rough. Are you sure that isn't RA? Normal mill steel is made to about 35 RMS. That means you roughen it up some more? If that is the case, you're talking about at least a 3 step and maybe 5 step mass finishing process. That much material removal will also work harden parts. Suggested procedure is to get and use the largest, coarsest ceramic media and run for maybe 2 to 8 hours at the maximum amplitude of your machine. Repeat with medium cut and a fine cut. You might also want to consider using a chemical accelerator instead of a normal deburring compound.
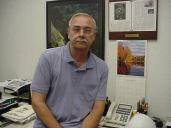
AF Kenton
retired business owner - Hatboro, Pennsylvania
2004
2004
A. In a tumbling barrel, max. efficiency is obtained when the barrel is loaded to about 60% of its volumetric capacity. For the mirror finishing on S.S. components, I would recommend
Step 1: Ceramic Media, Abrasive Grade.
Step 2: Plastic Cones, Medium Abrasive Grade.
Chemicals are available for such finishes that expedite the process.
Regards,
Niranjan S. Kulkarnifinishing machines - Thane, Maharashtra, India
February 11, 2016
Q. I make custom bracelets and am trying to get mirror shine on 302 ss wire. I tumble for hours, it seems like, but it always turns out the same finish with the ss pins I am using for the final polishing step. I am looking for a mirror finish and do not know if they make a chemical that will assist in the finishing, or do I need to approach this from a different methodology?
3 lb tumbler --
1st plastic resin abrasive br
2nd step ceramic polishing grade
3rd step ss pins with brass polishing compound
- hernando florida
![]() |
A. Kenneth, ![]() Anna Berkovich Russamer Lab ![]() Pittsburgh, Pennsylvania ![]() A. Good day Kenneth. Aerotek Mfg. Ltd. - Whitby, Ontario, Canada |
![]() |
Q. Okay, lets see if I can answer all of the questions -- - hernando, Florida February 16, 2016 A. It sounds as if the first step is too aggressive. Also, I have never worked with a magnetic tumbler and again cannot verify the finish you are getting; however, it sounds as if the compound might be the problem. A mechanical dry treated organic process always gets you a mirror finish but in smaller machines, this can take way too much time. ![]() AF Kenton retired business owner - Hatboro, Pennsylvania February 18, 2016 |
A. Dear Kenneth,
I would recommended that you use MAGNETIC PIN polishers first before you put the bracelet in the steel tumbler machine. Pin magnetic will give you better result as after you finish filing pin magnetic it for 20 -30 minutes and then put the bracelet in the steel tumbler for overnight for a mirror finish.
Also make sure that you don't add too much water & soap solution.We add C60 compound (Even I do not know the composition). Add compound OR any dishwasher to the tumbler chamber to the level of the steel balls only.
You should have a combo of Satellite steel balls & round steel balls in the ratio of 50% each
All the best to you.
Regards,
Jewelex India Pvt Ltd. - Navi Mumbai, Maharashtra, INDIA
August 14, 2018
Q. Hi, I am making stainless steel jewelries. I am planning to use stainless steel blanks, graphic stickers to stick on the blanks and then coated with epoxy resin. So I want my blanks to be shiny at the rim area and also want to make sure the sticker and resin bond to the stainless steel as well.
So my question is if I do tumbling on the the stainless steel to give a shiny look, the glue from sticker and epoxy will stick to stainless steel or not? Normally most people recommend to abrade the stainless steel before coating with epoxy. Can tumbling be considered as abrading?
Soe Thein- Singapore
March 10, 2018
A. Any coating will stick better to a rough surface than a smooth one; however, if that coating is thin it may not cover the peaks of the roughness. There is a trade off and as long as you do not burnish surface, it sounds like you can achieve what you are looking for.
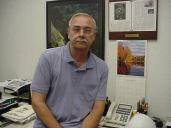
AF Kenton
retired business owner - Hatboro, Pennsylvania
March 16, 2018
April 9, 2018
Q. Hello,
I have recently bought a magnetic tumbler after reading about how good and efficient a polishing machine it is. The first item I polished was a SS small part. After 30 mins of tumbling, the ring was dull and had a frosted finish or what others call an orange-peel effect. I then noticed on the product page of the website that says: "Not a Final Polish May leave behind an orange peel effect on smooth broad surfaces."
So I tried to polish smaller items like a few pairs of gold and silver earrings. They too came out looking dull and frosty. Other items such as bracelet and necklace came out okay but I find the finishing quality inferior to that of a rotary tumbler.
I've tried using liquid and powdered burnishing compounds, experimenting on different amount of water used and extending the tumbling time but to no success. I have seen videos in youtube and read online articles showing how bright and shiny a seemingly plain ring (among other jewelry) can be after it has been tumbled in the magnetic tumbler.
The good thing about it is that it doesn't remove delicate designs on the jewelry during the tumbling process and produces a very even finish.
So what did I do wrong? Why am I struggling to get a bright and shiny finish as advertised? How should a magnetic tumbler be used in conjunction with other polishing tools? Also, should I polish my now frosty-looking ring with Tripoli then rouge or can I just skip it and apply rouge instead?
Any help is greatly appreciated!
I will upload photos my work and comparisons upon request. Thanks!
- Karachi, sindh, Pakistan
A. Hmmm. it sounds as if you are running the machine at too high an RPM. If there is no adjustment for speed then run fewer parts. Another important issue is the chemical compound, also the quality of the water may play into this. Then again, make sure you have a good grade of SS pins.
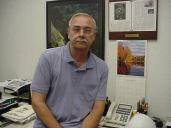
AF Kenton
retired business owner - Hatboro, Pennsylvania
April 10, 2018
Q. Hello my name is Ryan I have a question regarding polishing 303 stainless steel I have a tubular piece of metal 3 in Long quarter inch in diameter that I'm trying to get to a Polish mirror finish what kind of material would I tumble with to create the effect I'm looking for hand polishing is out of the question because I have over 5,000 of them to get done
Ryan Cason- Owasso, oklahoma/USA
April 20, 2019
? What kind of polish finish are you looking for. Subjective question. Are you looking for a smooth finish or a bright finish?
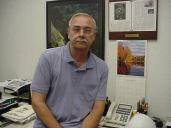
AF Kenton
retired business owner - Hatboro, Pennsylvania
April 24, 2019
Q. I am interested in the answer also, I have tubes in SS that were 3D printed, that needs a smooth finish inside, similar size to the previous question. Thought about extrude-hone but curious to see your recommendations.
Best regards.
- Montreal, Quebec, Canada
July 3, 2019
A. Hi Jasmin. Although your tubing may be the same size as Ryan's, polishing the inside of tubing is a totally different thing that polishing the outside :-)
Tumble polishing, magnetic pin polishing, and other ideas suggested on this page are inapplicable to I.D. polishing. You may be on the right path with abrasive flow machining, but chemical polishing might be applicable too.
I don't know if it's applicable to your situation, but making the tubing by electroforming nickel onto a wax or aluminum mandrel rather than 3-D printing it would give you a super smooth and totally non-porous ID without further processing.
Regards,
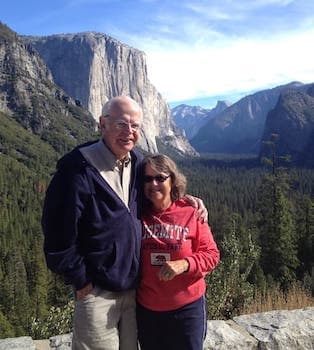
Ted Mooney, P.E. RET
Striving to live Aloha
finishing.com - Pine Beach, New Jersey
Q. I too, have been trying to attain a high polish on stainless steel part for many years now to no avail. I've tried a heavy duty, vibratory tumbler and a rotary, drum style tumbler.
Like others here, I've only been able to obtain a shine, but not a high polish. I'm polishing 304 and 316L stainless steel rings made from 1/4" thick round bar stock.
I've tried both wet and dry approaches, as well as multiple and various types of media, including ceramic balls and triangles, plastic triangles and stainless shot.
I just wish I could find the secret to obtaining the high chrome polish I'm attempting to obtain.
- seattle, Washington usa
August 2, 2019
A. If you're trying to obtain a mirror finish on stainless by mechanical tumbling, I don't think you are going to be successful.
You might do the preliminary smoothing by tumbling/vibratory finishing, but you're probably going to have to follow up with buffing or electropolishing.
It may be possible, if the parts are small, to electropolish in a barrel.
Rather than reinvent the wheel, you'll probably get to the answer sooner by working with a metal finishing shop that has electropolishing experience.
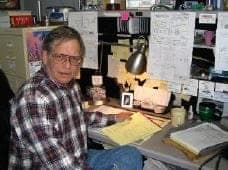
Jeffrey Holmes, CEF
Spartanburg, South Carolina
A. I agree; working with a metal finishing shop with experience is the way to go.
Ryan Murphy- Sanford, North Carolina, USA
Q. Hi, we are trying to polish stainless steel hardware parts in a vibratory tumbler, but are unable so far to get even a good base from which to polish from. We have tried both cone and angle cut triangle white media in a cleaning solution, but it seems to leave the surface with a bunch of little pock marks that only become more pronounced when we go to polish. Can you share what you use in your first and second stages? Most of these parts are a few inches by a few inches. Thanks a lot.
Andrew VonnegutCustom Hardware - Santa Barbara, California, USA
September 24, 2019
A. If you're getting dents/divots, your mass finishing is too aggressive. Reduce speed, reduce load size, load larger percentage media/parts.
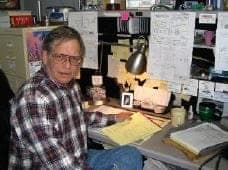
Jeffrey Holmes, CEF
Spartanburg, South Carolina
Q. Thank you for the response. I am using a conical, medium ceramic media on stainless steel with the tub only 1/3 full and only a few parts in it. It seems strange. Here is a picture of the media and the results.
Thanks again. Andrew
Andrew Vonnegut [returning]Caav Designs - Santa Barbara, California
October 2, 2019
A. If that's an actual photo, you're running the process dry? If so, try running with water and a bit of detergent.
I don't know the scale of your photo, but at least some of the damage appears to be part-on-part impingement. It may be that the parts are simply too large/heavy for vibratory finishing.
Mechanical buffing, or electropolishing on fixtures may be the answer.
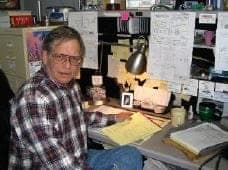
Jeffrey Holmes, CEF
Spartanburg, South Carolina
Thank you Jeffrey, I appreciate your comments. I am recirculating a solution of VF-100 cleaning compound in the bowl. Also, the parts are only a few inches by a few inches, max. The pits seem to have come from the finishing process itself, since some of the parts were fine finished in the machining process and developed pits during vibration. I only have 6 parts in the whole tub, so not sure if they pits could come from part on part interaction. Thanks again for any ideas you have. Andrew.
Caav Designs - Santa Barbara, California
A. Jeff gave you some good information; however, I need to put a lot more media to keep parts separated. The weight and size of the parts might be another factor. You can also reduce the problem by going to a smaller size media, but you will increase your run time.
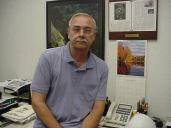
AF Kenton
retired business owner - Hatboro, Pennsylvania
Q, A, or Comment on THIS thread -or- Start a NEW Thread