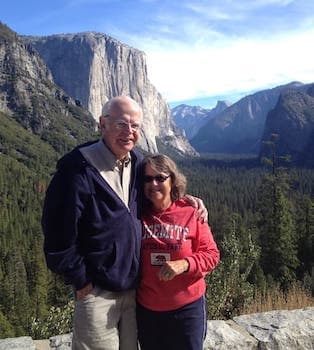
Curated with aloha by
Ted Mooney, P.E. RET
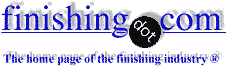
The authoritative public forum
for Metal Finishing 1989-2025
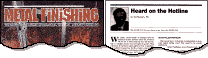
-----
RMS conversion to anchor profile depth
Is there a chart or a calculation for representing RMS in terms of profile depth (anchor pattern) used for surface preparation for protective coatings? Most protective coatings specifications state the anchor profile in mils (.001") depending on the coating system. Sometimes RMS is used. What is the profile depth in mils equivalent to 250 RMS?
Bill Gouletteconsultant - Spring, Texas
2004
You know, it bothers me to see a question go unanswered. Maybe I can redirect your thoughts. First of all 250 RMS is one h--- of a surface roughness. I'm not sure it is possible to have a piece of metal that rough unless you intentionally rough it up. Considering that mill steel from the factory is about 35 RMS at its roughest, I can't understand why you would want to even consider this question.
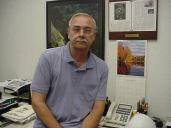
AF Kenton
retired business owner - Hatboro, Pennsylvania
2004
I agree, 250 RMS is very rough; that works out to gouges of a half inch deep! Was the 250 maybe referring to abrasive grit size used to blast the surface? That would be about right for a .001 anchor profile. Anyhow, RMS roughness defines how much a surface deviates from a plane. The RMS stands for Root Mean Square and is a way of calculating the height variations while ignoring whether the measured points are above or below the nominal surface. In words, it's: the Square Root of the Average of the Squared Deviation from the Average Height.
(For the mathematically inclined: Sqrt[(1/n)*Sum((X(s)-Xave(s))^2)] Where: X(s)= the height of an individual measurement Xave(s)= the average height ^2 means to square the value n= the number of measurements Sum means to add up all the values ).
So a 250 RMS roughness will have average high and low spots of 1/4 inch from the nominal surface. The anchor profile or anchor height is just the peak-to-valley height difference on the surface. In light of the above, 250 RMS would be approximately an anchor profile of 500 or so. The 'approximately' in the last sentence is because the RMS roughness depends on the shape of the hills and valleys and on the size of the probe tip you use to measure the valleys; a larger probe won't go as deeply into the valleys as a smaller probe would.
Tom Gallant- Long Beach, California
2004
CORRECTION:
Surface finish is defined in microinches or millionths of an inch, not in mils (thousandths) as previously stated. a finish of 250 is about what you would get with a rough saw-cut or a smooth flame-cut. I recall that several decades ago there was a plastic panel available that was embossed with various finish levels. You would run your thumbnail over the work and then over the plastic, trying to find an approximate match. More detailed information is in specification ASME B46.1, available for a price from the American National Standards Institute (ANSI).
- Long Beach, California
2004
August 4, 2008
A little explanation: My work primarily has to do with protective coatings and linings. The .010-.020" thick coatings that are applied to goods (primarily oil field equipment) to protect it from the environment (normally subsea).
Abrasive blasted substrates that are prepared to accept these coatings may have an "amplitude" of .002 - .003" (2-3 mils). This is referred to as anchor profile and is expressed in mils in the US, and microns internationally. Blasting is designed by adjusting abrasive size, air pressure etc to achieve various anchor profile depths depending on the thickness of the protective coating to be applied.
Occasionally, parts originating in a machine shop environment may specify the anchor profile in RMS terms, presumably because this is the measure they typically work with. I was hoping for an "RMS to mil (or micron)" conversion.
Thanks for your responses.
consultant - Spring, Texas
Ran across this page looking for a conversion calculator to convert metric surface finish to RMS as we Americans are used to dealing with. Thought I would comment that a 250 RMS is used quite often in the pipeline/petrochemical industry. Many flange faces are required to have at least a 250 RMS finish dependent on the gasket material type. This rough spiral finish allows the flange sealing surface to "bite" into the gasket when the flanges are torqued.
Melvin Garner- Spring, Texas
October 7, 2009
The original question is valid. I am facing the same question in my job right now. A 250 RMS finish is actually not as rough as the first few commenters allude. The finish would have regular machined or blasted ridges on the order of less than 1/64" tall. The purpose is to make a gasket or sprayed material adhere. For a gasket, it would likely be a "phonographic" finish to anchor the gasket material solidly and seal better. If you have seen an old vinyl record, it is nearly the same finish, hence the name it is called commonly (in a machine shop that does such work anyhow).
Daniel Pease- Saint Marys, Georgia
February 23, 2012
Q, A, or Comment on THIS thread -or- Start a NEW Thread