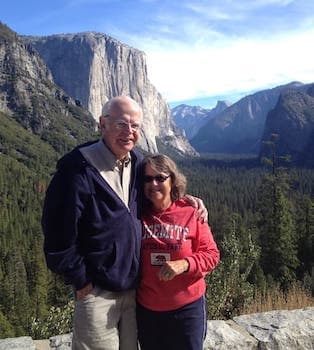
Curated with aloha by
Ted Mooney, P.E. RET
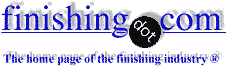
The authoritative public forum
for Metal Finishing 1989-2025
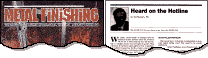
-----
Help dad help son with copper plating project
2004
I am hoping you can answer a question my son and I have about his plating experiment. He is working through his Science Fair experiment. His hypothesis is that increasing the voltage will increase the amount of copper deposited on the cathode. He is using copper bar for the cathode and brass strips for the anode. The bath is Cupric sulphate, Distilled water and Sulfuric acid.
During each run there appears some residue laying on the bottle of the plating tank near the anode. We are curious if you might know what this is? Our supposition is that it is zinc. Since brass is an alloy of zinc and copper we believe the zinc is being eaten away by the acid bath and leaving the copper which is then thickened by the playing process. Are we even close in our supposition?
Thanks,
Douglas R JonesStudent's Dad - Carrollton, Texas
First of two simultaneous responses --
Well done dad, you deserve a gold star for your initiative and enterprise! You have the right basic concept formulation for copper plating; the best simple formulation is 200 g/l cupric sulphate and 30 ml/l conc sulfuric acid. You can also add about 0.1 g/l sodium chloride (common household salt) to the solution if you want to be a bit more professional! This will help dissolve the anode. I do, however, find it interesting you chose the anode to be brass and the cathode copper - you would be better off using brass as the cathode and copper as the anode. This is because the anode will dissolve and keep a reasonably constant copper ion concentration in the solution. Secondly, you will see the copper deposit on the brass as it is a different colour. Having brass as the anode means the brass will dissolve, which admittedly will replenish some of the copper but not all of it. Thirdly, you will be contaminating the solution with zinc ions and this is not a good idea. The residue you see could be zinc salts, but since we don't know how much acid you used, I can only speculate. It is possible that the zinc may precipitate out as zinc hydroxide, which will be a white gelatinous deposit, but I would expect it to ultimately redissolve in the acid. However, if the brass is free machining, it will contain lead and the deposit could be white lead sulphate, which will be insoluble. If I had to guess, I would go for the debris being lead salts. Try making the copper the anode and the brass the cathode and see if you get the same effect - that should tell you something!
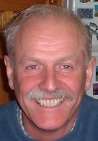
Trevor Crichton
R&D practical scientist
Chesham, Bucks, UK
2004
Second of two simultaneous responses --
This is more likely coming from the Cu anode. The copper anode passes through oxidation states as the anode corrodes, and a properly maintained Cu anode should have a black film on it. Usually, Cu anodes are enclosed in a polypropylene fabric bag to contain the anode sludge. You might also consider adding about 50 ppm chloride to the bath.
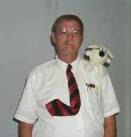
James Totter, CEF
- Tallahassee, Florida
2004
Thank you both for your responses! And thank you for pointing out that we GOOFED! We had it completely backwards! We assumed that the bath would be full of negative Cu ions. Thus the object to be plated should be the anode! Oops! Apparently, the bath is loaded with positive Cu ions and Actually this is probably more my fault than his! EEs should stay out of chemistry labs ;-) I think what we will do is rerun the experiment switching the anode and cathodes around and compare the results! I will suggest, also, that we add a little NaCl to the bath.
Thanks again!
Douglas Jones- Carrollton, Texas
2004
I forget exactly why it is, but you're right about an EE's polarity and a plater's polarity being opposite.
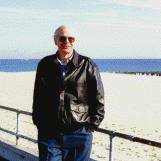
Ted Mooney, P.E.
Striving to live Aloha
finishing.com - Pine Beach, New Jersey
2003
Q, A, or Comment on THIS thread -or- Start a NEW Thread