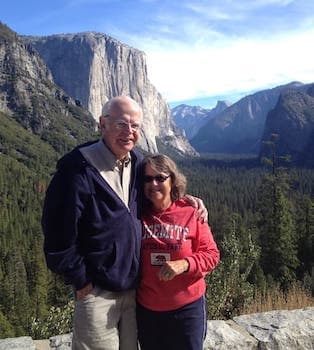
Curated with aloha by
Ted Mooney, P.E. RET
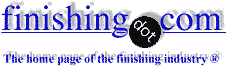
The authoritative public forum
for Metal Finishing 1989-2025
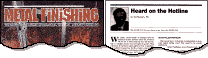
-----
Aluminum oxide
Dear Sirs,
We are manufacturing SS needles and pins. To remove material i.e., to reduce the diameter we put the needles ( approx. 400 kgs) with Aluminum Oxide ( either brown or white grit size 90/100)and water in barrels. However at the end of the cycle , we observe tiny holes ( under 16/25X) on the surface of the needles. We assume that these are caused by the Aluminum oxide grains, which maybe initially embedding themselves in the needles. Can anyone therefore suggest what grit size of Aluminum oxide should be used to avoid these tiny holes. We remove approx. 200 microns of material from surface in this barreling process. We generally wash the aluminum oxide once the cutting stops and put new Aluminum oxide and water till we achieve the desired diameter. Is any other material suggested for cutting which will not embed?
Radhidoshi JonesEngineer - Melbourne, GA, Australia
2003
Two points.
1. Bit risky considering action to combat what you ASSUME is the mechanism producing the holes - and a mechanism that seems very unlikely, anyhow. Should first be sure of what is happening, so that informed decision can be made on corrective action, rather than guesswork.
2. What grade of stainless steel? The processing that you describe generates quite aggressive corrosion conditions, and the grade of steel becomes an important consideration.
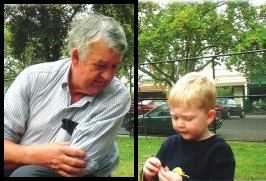
Bill Reynolds [deceased]
consultant metallurgist - Ballarat, Victoria, Australia
We sadly relate the news that Bill passed away on Jan. 29, 2010.
2003
Sounds like you are on the right track with your problem.There are alternative media materials; however, try a smaller size alum oxide first. Maybe 400 or smaller. If you were polishing, I'd even recommend a smaller size.
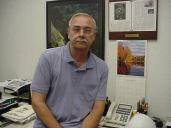
AF Kenton
retired business owner - Hatboro, Pennsylvania
2003
I agree, even if the SS is not of a superior grade, a slower method of finishing would assure a less aggressive deterioration of the surface.
Stephen Duvalloil field services - Elreno, Oklahoma
2004
Q, A, or Comment on THIS thread -or- Start a NEW Thread