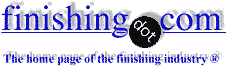
-----
Can nickel/nickel chrome replace electro zinc plating?
Our product is 10 feet long, so not many shops can handle the length when doing electro zinc plating. There are more shops available who can do nickel and nickel chrome plating in 10 foot lengths. I have not been able to find a comparison of the two finishes. The product is for indoor use, so corrosion resistance is not too difficult. There is some question about conductivity and the ability to bend the product in the field.
Kevin Phelanproduct design - Brewton, Alabama
2003
First of two simultaneous responses --
The biggest difference is that zinc plating is a sacrifical coating whereas nickel-chrome is a barrier layer coating. If the part is scratched, zinc is still effective in preventing it from rusting, whereas the nickel-chrome will actually accelerate the corrosion of the tubing. That does not mean that nickel-chrome is not useful, however.
In a mild environment it probably doesn't matter which you choose. In a severe environment, a very high quality nickel-chrome will work wonderfully, as witness truck bumpers. But a low quality nickel-chrome plating is worthless in a severe environment.
Nickel chrome is significantly more expensive, but nicer looking. Neither is a very malleable coating well suited to bending.
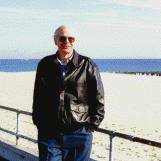
Ted Mooney, P.E.
Striving to live Aloha
finishing.com - Pine Beach, New Jersey
2003
Second of two simultaneous responses --
You can look for other coating methods for Zn than conventional electroplating.
Regards,
Pankaj Gupta- Baton Rouge, Louisiana
2003
2003
You need to give more information about the application. Since you have stated that corrosion resistance is not a problem (and probably would not have been even for an exterior application) the "field bending" can be a problem if the plater is not aware of this need and does not use processes that will allow for the needed ductility and grain elongation of the plate. The thickness of plating is also important in this consideration. You really need to develop a spec for thickness, etc before you can determine if a substitute process is applicable.
Not to mention specific shops, but if you were to ship a greater distance I know that in an overnight freight zone of most of Alabama there are a number of zinc platers who could probably do the job. You probably should increase your geographic search to within 500 miles ±
Gene Packmanprocess supplier - Great Neck, New York
Q, A, or Comment on THIS thread -or- Start a NEW Thread