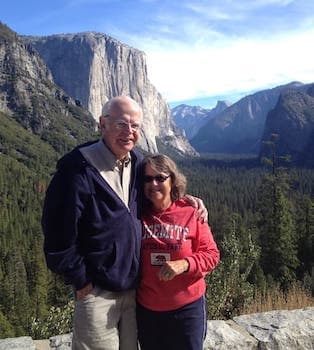
Curated with aloha by
Ted Mooney, P.E. RET
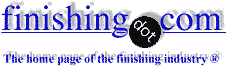
The authoritative public forum
for Metal Finishing 1989-2025
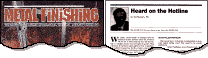
-----
Requirements for type III anodizing with a type II setup
We are currently doing a type II anodizing and would like to try doing some type III. Our process uses 25% sulfuric acid in our tank and this solution is maintained at a temp. of 60-62 F. I have a DC power supply that will run 12-24 volts and up to 50 amps. Our sealing process is boiling water. We mostly use 6061 and 7075 aluminum. What changes would be required for us to do type III anodizing?
Brent C [last name deleted for privacy by Editor]Vocational Instructor - Pulaski, Tennessee, US
2003
You may know that two competing processes go on during anodizing: the electricity oxidizes the aluminum, thereby building an insulating aluminum oxide film, while the sulfuric acid concurrently dissolves this film. To get type III hard coat--which is a significantly thicker layer of oxide--you reduce the temperature to slow the acid attack. However, the anodized film is an insulator so even at the lower temperature the film will stop building unless you increase the voltage. There are proprietary additives that allow a "type two and a half" anodizing at higher temperature and somewhat lower voltage, but true type III anodizing requires operating at about 28 deg. F, 10 percent v/v sulfuric acid, and a voltage probably somewhere between 48 and 75 volts. It is not enough to keep the average temperature at 28 deg., you have to hold that temperature right at the part, and that requires rigorous and reliable air agitation. And you need very reliable rack contacts to prevent arcing.
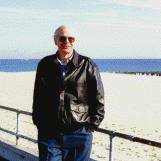
Ted Mooney, P.E.
Striving to live Aloha
finishing.com - Pine Beach, New Jersey
2003
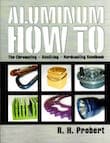
Aluminum How-To
"Chromating - Anodizing - Hardcoating"
by Robert Probert
Also available in Spanish
You'll love this book. Finishing.com has sold almost a thousand copies without a single return request :-)
Treatment &
Finishing of
Aluminium and
Its Alloys"
by Wernick, Pinner
& Sheasby
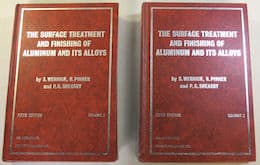
(note: this book is two volumes)
on eBay or
AbeBooks
or Amazon
(affil links)
Hungry student for knowledge, wondering how to do a Type III MIL-A-8625 / MIL-PRF-8625 [⇦ this spec on DLA] Hard Coat Anodize for Large Aluminum pieces. Have tried looking for information but still find a it hard to come down to a better process used for this type of situation. Already have equipment, however not sure exactly how to do it. What is required to do a Type III Anodize?
Matt KunitaStudent - Honolulu, Hawaii
May 13, 2008
May , 2008
Hi, Matt. Sorry, but I can't figure out what your question is if you don't frame it in terms of how I've already replied. You have (or should have) the spec in question, which will include some exact numbers. What do you mean by wanting a better process for the situation? -- you have to do everything that the spec requires. Please spend another paragraph or two telling us your question more exactly, or consider borrowing or buying a book about anodizing, which can present the subject in a more protracted tutorial fashion that can be done in a forum posting. Good luck.
Regards,
Ted Mooney, P.E.
Striving to live Aloha
finishing.com - Pine Beach, New Jersey
Hungry student for knowledge, wondering how to do a Type III MIL-A-8625 Hard Coat Anodize for Large Aluminum pieces. Have tried looking for information but still find a it hard to come down to a better process used for this type of situation. Already have equipment, however not sure exactly how to do it. What is required to do a Type III Anodize?
Matt Ku.Student - Honolulu, Hawaii
May 13, 2008
Wondering on how to do a Type III Anodize. What consistency should I have my solutions at? How long do I leave it in? What is the best Temperature and current to run it at? Is there a way to figure out how long to leave multiple pieces of different sizes in to get a 2 mil hard coat?
Matt K.Student - Honolulu, Hawaii
May 14, 2008

Q, A, or Comment on THIS thread -or- Start a NEW Thread