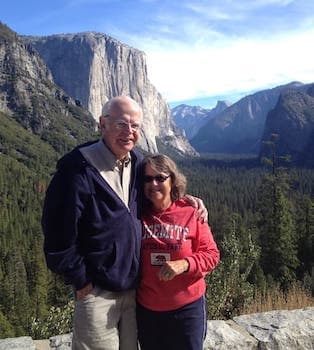
Curated with aloha by
Ted Mooney, P.E. RET
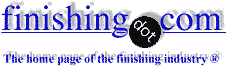
The authoritative public forum
for Metal Finishing 1989-2025
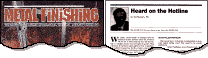
-----
Ideas for non-conductive coating on locating pins for spot welding
I am a Manufacturing Engineer at a welding facility where we produce chassis frames for the automotive industry. We have many spot welding applications where a locating pin is used to position two components together. Typically, we try to keep electrical current out of the pin because it causes the pin to wear quite a bit faster that normal. What type of coatings are available to be applied to a steel detail that would be non-conductive and have good wear characteristics?
Benjamin A. KarrerManufacturing Engineer, Tier One Auto Supplier - Galesburg, Michigan
2003
Ceramics as a class of materials have good wear resistance and low electrical conductivity. I would investigate liquid nitriding (Kolene, Arcor, etc.) the steel as this is a common surface engineering process (combination of coating and diffusion heat treatment). Other coatings to investigate are tool coatings like TiN, TiAlN, AlTiN, etc.
Toby PadfieldAutomotive suspension modules - Michigan
2003
TiN, TiAlN, and most other nitrides are electrically conducting. The non-conducting coatings include alumina, zirconia and AlN. These latter can be deposited by CVD, PVD, or plasma (thermal) spray processes.
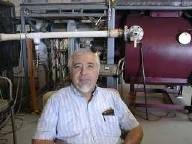
Jim Treglio - scwineryreview.com
PVD Consultant & Wine Lover
San Diego, California
2003
We have for many years applied a wear resistant ceramic coating via plasma spray on pins used in spot welding. At first we used ceramics with high dielectric strength but soon realized that wear was more important so we selected a ceramic that had the best wear resistance as its lower dielectric strength was still sufficient for the low voltages associated with spot welding. The coating worked well enough to eliminate the need for heat treated pins and allowed the use of mild steel or austenitic stainless steel for pin material (I am not sure why; something about magnetic fields).
Grant Robinson- Georgetown, Ontario, Canada
December 23, 2008
Q, A, or Comment on THIS thread -or- Start a NEW Thread