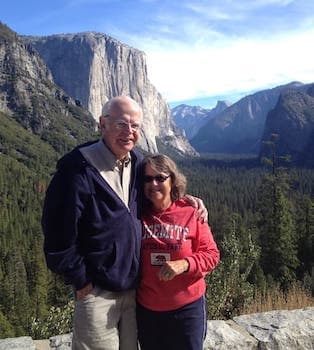
Curated with aloha by
Ted Mooney, P.E. RET
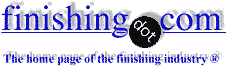
The authoritative public forum
for Metal Finishing 1989-2025
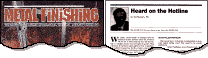
-----
Zinc Alloy Plating on carbonitrided steel is "chipping" during plating and drying
2003
Q. We are barrel plating carbon nitrided steel parts in an Alkaline Zinc Cobalt bath. These parts are then dipped into a hex-chrome passivation bath and dried at 190 °F.
The problem we are having is that the plating on the parts chips when they are banged around during the unload process from the drier. The plating is not flaking off entirely. The standard for plating these parts is 8-10 microns. The chipped sections have 1-4 microns of plating remaining.
This chipping is adversely affecting our neutral salt spray results and we are concerned about future quality issues.
Our current cleaning process is as follows:
- Soak Cleaner @ 170 °F with air agitation, rotated for 6 minutes.
- Two rinses (counterflowing)
- Acid Pickle, hydrochloric between 30 and 60 percent with 0.1% inhibitor; six minute cycle time
- Two rinses (counterflowing)
- Reverse Cleaning @ 160 °F and 800 amps with air agitation; six minute cycle time
- Two rinses (counterflowing)
Why is the chipping occurring and what can we do to prevent it? Is there any way this can be solved without changing the number of stations within the cycle? Thanks for any help.
David CustisChemical Manager - Columbus, Ohio
A. The chipping of the plated Zinc/Cobalt coating that you describe is coming from part on part action in any of the final finishing operations. You mention the dryer. I believe that dryers should have a "soft-start" mechanism and also be thermostatically controlled.
The soft start will allow the parts to dry in your centrifugal dryer without any part on part chatter, or at least minimized chatter. If your dryer cannot be retro-fitted, you can jockey the start switch off and on until the parts are all comfortably seated. Then allow them to dry. Also, I do not like drying over 140 °F. Higher temperatures will desiccate or dry out the chromate film that you have just applied, reducing the corrosion resistance markedly.
Finally, if the plated deposit in your opinion is brittle, you might wish to contact your vendor and address that problem with their Sales/Technical staff for a possible remedy.
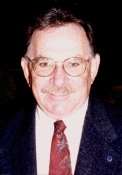

Ed Budman [dec]
- Pennsylvania
With deep sadness we advise that our good friend Ed passed away Nov. 24, 2018
2003
Q. Hi experts,
I'm new to barrel plating.
But I am now facing brittle deposits on bolts and nuts ONLY! Other stamping parts have no problem at all. Anyone face this type of problem before?
Lovely thanks & Please advise.
- Penang, Malaysia
May 31, 2013
A. Hello Tim!
First of all, what are other stamped parts? Please specify as much you can to help us help you! And are you using a zinc plating bath, or other kind of bath? Alkaline or acid?
If you can clarify these questions above, we may help you with your issue in barrel plating.
Regards :)
- Cañuelas, Buenos Aires, Argentina
June 12, 2013
Q. Hi Daniel Montañés,
Stamping parts are motorcycle parts. I'm running acid zinc bath.
Lovely thanks for help! Cheers,
- Penang, Malaysia
June 14, 2013
June 17, 2013
A. Hello Tim,
Nuts and bolts usually are heat hardened, so they are somehow more difficult to plate than non hardened parts. This problem usually appears in alkaline zinc baths, and not in acid ones. If you have problems with chipping in bolts and nuts, I suggest:
FIRST TALK TO YOUR BRIGHTENER VENDOR, HE MUST ASSIST YOU!!
Then, there are some things you can try...
- Lower the brightener concentration, or do not add brighteners until you see in Hull cell (or in the parts if you can't do a Hull test) some brightener problem.
- Lower the tension, so the current will more leveled and the zinc deposit will be less brittle. You may have to increase the time in order to achieve the same thickness!
- Make the total chlorides (potassium or ammonium chloride) go up to the maximum concentration that your vendor puts in the technical data sheet (135 grams per liter of total chloride is a good concentration for bolts, nuts and screws). This will grant you more level in the process current.
I hope some of this works! And welcome to the plating world!
Regards,
- Cañuelas, Buenos Aires, Argentina
August 5, 2013
Q. Checked the hull cell test, brightener concentration is fine, but with high zinc metal concentration 28.3g/liter!
Is the problem caused by the zinc metal concentration?
Why after I hold the plated parts my hand is stuck with lot of zinc from the plated parts?
I ready don't have any idea to solve out the problem, please help me.
Please check the attached photos
Lovely thanks, cheers.
- Penang, Malaysia
A. Hi Tim!
Please tell me what is for you "fine" in Hull cell, as I have seen many Hull cell tests validated as "OK" and not being OK for me...
If the brighteners are OK, Hull cell test OK, zinc in 28 g/l (seems high but some acid zinc systems work in that value, I work in that value for barrel plating and works fine) and no organic contamination (Hull cell test should consider this), you should see the potential and current parameters in the zinc tank for this part: maybe you should lower the V (potential) in your process, so lowering the current and diminishing the chipping problem.
This change in your process parameters could "hide" some other problem in your process, please ask your vendor for assistance to get concentration of zinc and brighteners to normal :)
Good luck and best wishes!
- Cañuelas, Buenos Aires, Argentina
August 29, 2013
Q. Dear Sir,
I would like to the possibility of Alkaline Zinc Nickel Plating of Carbonitrided Low Carbon Steel (C1022), carbonitrided using process (Case Hardened 500 HV and Core Hardness of 400 HV ). Part: Fastener.
If possible could you suggest the process sequence.
Regards,
- Chennai , India
October 29, 2014
A. Hi Geetha. As you'll read on this and related threads, alkaline zinc alloy plating of carbonitrided parts probably can be done, but is quite difficult to do reliably. In the old days, platers would do a cadmium strike before cyanide zinc plating. Today, a cadmium strike is usually not environmentally acceptable. So your choices are probably to tear your hair out trying to achieve a robust alkaline zinc-nickel plating direct on the carbonitrided surface, or start with a Wood's Nickel strike :-)
Other input is welcomed; I am not a plater and most of my suggestions are just book knowledge.
Regards,
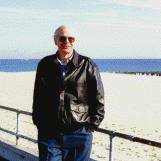
Ted Mooney, P.E.
Striving to live Aloha
finishing.com - Pine Beach, New Jersey
October 2014
Q, A, or Comment on THIS thread -or- Start a NEW Thread