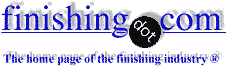
-----
Corrosion protection of 6061 AL, electroless nickel or anodizing?
We've plated a set of 6061 AL heat exchanger plates that have a cooling/warming fluid running inside them with a proprietary electroless nickel meant for extreme corrosion protection. The plates are held a fixed distance apart. Between the plates is yet another heat exchanger (HE) made from polyethylene inside which another fluid to be cooled or warmed is circulated. Depending on the relative humidity, there can be some wetness between the plated plates and the poly. HE. We've found raised pits on the nickel plated plates over the course of months. Sometimes the poly HE is left in place trapping the condensed water between the plates and the poly HE. My question is should we expect the electroless nickel to protect the 6061 AL plates. Due to the reduced thermal properties we didn't want to use anodizing but we might have to give up performance if that's a better solution to this problem. Can anyone comment?
Thanks,
Medical Equipment Engineer - San Diego, California, USA
2003
The raised areas underneath the nickel are the corrosion deposits resulting from an electrochemical attack on the Al6061. Inadvertently I am sure, you have an electrochemical cell formed with nickel and aluminum, an ideal battery. The nickel is more noble so is protected, while the aluminum is giving up to the nickel. The vapor is needed to form the electrolyte so the cell can operate. The diagnosis is a classic but the solution is not classic. To solve this we need more information. Try to eliminate the metal couple, nickel-aluminum, from getting wet.
Dave Fairbourn- Sandy, Utah
2003
I'm not sure how we could ever eliminate the moisture from the part. The "cooling" plates will drop down to around 0 °C during normal operation and remain there for hours at a time. The environment is not perfectly dry so there is always some degree of condensation occurring. While it could be dried up by requiring the unit to heat up to 50 °C after each cooling cycle, that's not always practical and so we're considering anodizing the surface to better protect it.
Fred Bacher- San Diego, California, USA
2003
Q, A, or Comment on THIS thread -or- Start a NEW Thread