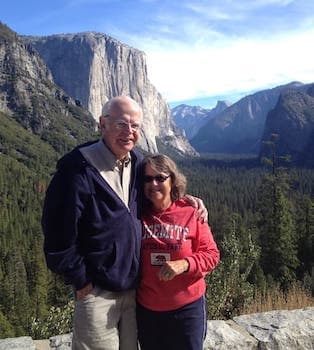
Curated with aloha by
Ted Mooney, P.E. RET
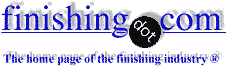
The authoritative public forum
for Metal Finishing 1989-2025
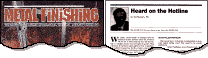
-----
Economically getting chrome plating adhesion on Hastelloy and stainless steel
Q. We have been chosen to hard chromium plate two materials; one is a stainless steel, and the other a nickel based Hastelloy. At this stage I don't know the exact compositions or final heat treated conditions, but I do know they are French alloys.
We trialled them by using the standard vapour degrease, grit blast and reverse sulfuric/hydrofluoric etch, but as we all know, some of these alloys can be very hard to properly activate. The result was no adhesion after chrome plating.
Next we tried using a nickel strike and flash sulphamate nickel plate in addition to the above, and it worked quite well. But we want to avoid using this to keep our costs down. Does anyone have a suggestion as to what cleaning and activation cycle we may employ that will give us the good adhesion required, without having to resort to the nickel under-plating?
Materials & Processes Engineer - Melbourne, Victoria, Australia
2003
A. Trevor,
Hastaloy is almost the same alloy like Inconel 648 and 718 thats is a very difficult alloy to plate on. I have describe a method for it in letter 12398. This method works for me.
Regards,
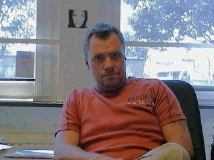
Anders Sundman
4th Generation Surface Engineering
Consultant - Arvika,
Sweden
2003
A. Prep as you have, Light reverse current etch in chrome tank. Big hassle and expense is the big knife switch you will need.
Jon Quirt- Minneapolis, Minnesota
2004
A. Trevor,
As a jobbing shop, I get hundreds of jobs that are "stainless" or
"Hastelloy". The thing that we find always works is a good hydrogen flush. If the alloy has a high chrome content (a bluish colour) then a light etch first, if a high nickel content (a yellowish colour) then straight into the vat live. If you're not sure of the voltage to flush, Start plating at lowest possible voltage, and turn up until you see the first bubbles appear, then turn up a 1/2 Volt every 5 minutes, to the plating speed. On some of the Hastelloys you have to raise the voltage above the plating voltage for a few seconds to 'strike' and start them plating.
Regards, Steve ;-)
PS. For practical demonstration send air tickets to.....
hard chrome plating - Cheshire, England
2004
A. Would try activation H2SO4/HF using current 30-50 A/sq dm, and then as Mr Steve Kelson suggested.
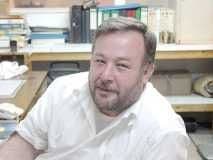
Khair Shishani
aircraft maintenance - Al Ain, UAE
2004
Pretreatment before hard chrome plating
Q. We are plating hard chrome with SS 316 as base metal. Will shot peening improve adhesion? Or suggest me a process to improve adhesion. Plating area will be in inner diameter of a cylinder.
Vigneshwaran N- India
June 28, 2015
A. Hi Vigneshwaran. The usual reason for shot peening is to improve fatigue life. I'm no expert on the subject, but from a layman's perspective: the shotpeening compresses the outer skin of the part so that when the part is loaded, the first portion of the tensile stress at a crack in the chrome plating just goes towards relaxing the compressive stress, in order to deter the propagation of a stress riser at the crack.
To the extent that shot peening acts sort of like blasting, it might offer some improvement in adhesion to unblasted parts, but I doubt that it would solve the problem of adhesion onto stainless steel. Anders and Steve seem to be on the same track that, after activation, "hydrogen flushing" is very useful. Sorry, but I have only book knowledge on this subject, but their postings on that subject are easy to understand.
Regards,
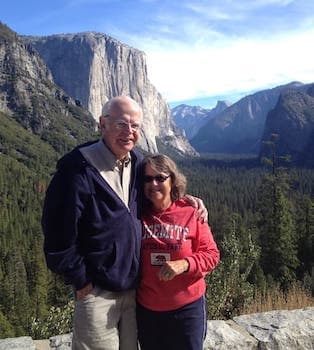
Ted Mooney, P.E. RET
Striving to live Aloha
finishing.com - Pine Beach, New Jersey

Q, A, or Comment on THIS thread -or- Start a NEW Thread