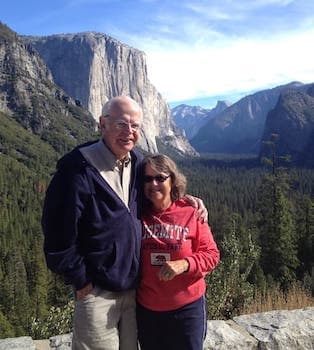
Curated with aloha by
Ted Mooney, P.E. RET
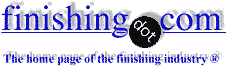
The authoritative public forum
for Metal Finishing 1989-2025
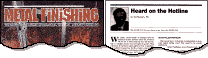
-----
Sandblasting before Anodizing -- Q&A, Problems & Solutions
Q. The sand blast material after natural anodizing, there is certain spot looks shining as shown in Figure.
- Kapar Klang Malaysia
April 16, 2021
⇩ Related postings, oldest first ⇩
Q. To Whom it May Concern:
I am anodizing per MIL-A-8625 / MIL-PRF-8625
[⇦ this spec on DLA] Type II, Class II black on 6061 aluminum which prior to anodizing is being powder glass bead blasted at the customers facility. After anodize the part becomes patchy with white streaks where it appears the blasting is uneven. I have tried varying my Alkaline Etch time from 15 seconds to 2 min. with no improvement. If you would have any solutions on this matter it would be appreciated as it involves large quantity orders and several different jobs.
Respectfully,
Tim
Anodize Shop Manager - Chino Valley, Arizona, USA
2003
A. This is VERY simple, follow this instructions :
1) etch in your caustic for 10 sec,
2) 20 sec deoxidize,
3) approx. 45-60 sec in ABF solution.
4) flash anodize for 10 min.
5) GO BACK TO YOUR CAUSTIC ETCH, STRIPPING THE ANODIZE
6) deoxidize the same as before 20 sec.
7) go back to your ABF solution same time
8) anodize for normal time w/your dye and seal
And that's how you get rid of the streaks from any blasting
- Oxnard, California
2003
A. Poor Bead Blasting is poor bead blasting. Excessive pressure and uneven blasting produces uneven appearing parts. The solution is to decrease pressure, use the proper media and blast with even movement. Aluminum will "burn" otherwise. Few people know how much art is involved in cosmetic beadblast. To correct the problem a strip, light & even beadbast, and anodize.
Good Luck.
- Santa Cruz, California
2003
Multiple threads merged: please forgive chronology errors and repetition 🙂
Sand blasting media for clear anodize pre-prep
Q. What Sand Blasting Media is best when trying to achieve a uniform clear anodized surface on 6061-T6 Aluminum? We have tried vibratory tumbling and have been unhappy with the uniformity.
Thanks,
owner - Crystal Lake, Illinois, USA
2004
A. If you are unhappy with vibratory wait until you try blasting. Abrasive blasting methods will leave you too rough of a surface and your plating processes will be not be uniform, and/or subject to failure. For good protection plated surfaces need to a be about 18 RMS or finer (lower). About the best blasting can achieve is about 35RMS. Probably your vibratory problem is that the media composition is too rough (coarse) and therefore you may have to do a multi-step operation.
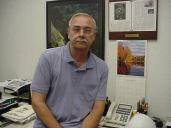
AF Kenton
retired business owner - Hatboro, Pennsylvania
2004
A. In your other post you were talking about bright anodizing. Is this another product? If you are using the vibratory tumbler to deburr and then doing a light etch, you should get the desired uniform (satin-like) finish on your parts. What is the product?
Michael Georgiadisengineer - Durban, South Africa
2004
A. With a hand held wand it is absolutely impossible to get a "uniform" finish on (soft) aluminum. This is because anyplace that gets 3 seconds longer blasting then an adjacent place will have a "shelf" and hence never uniform.
Further, any kind of blasting makes the anodizing non-uniform because the metal is soft and you are pounding it with a hard substance backed up by strong force. You will be pounding all sorts of non-aluminum junk into the surface. Some of this junk can be removed in the alkaline etch. Hey, why not just alkaline etch (after thorough cleaning) and get a uniform finish to start with?
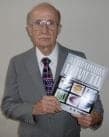
Robert H Probert
Robert H Probert Technical Services

Garner, North Carolina
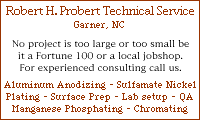
2004
Multiple threads merged: please forgive chronology errors and repetition 🙂
Anodizing doesn't remove water stain marks
Q. We have received Aluminium Section for Anodising which is having water stain marks on it and we are unable to remove the with caustic etching can anyone suggest any other process for removing this water stains. Alloy is 6061.
Satish Shahchemicals - Anand, Gujarat
2005
A. If the parts can handle the dimensional change, you can etch it, then anodize it, then remove the original anodize in the etch, then anodize it again.
That would probably work, a lot of parts look a lot better the second time around - most of the impurities/stains are incorporated into the original oxide layer and removed when you remove it.
Don't try this with castings though, I imagine it would result in a very poor second anodize due to the other casting constituents.
Good luck.
Compton, California, USA
2005
A. It has been my experience you need to deox or desmut the part first. If you anodize over a water stain it will set the pattern, and then only mechanical means can remove it.Sometimes it has helped us if we also flash anodize the part .To do this we desmut , rinse, anodize for five min., rinse and then go back through your regular process.
Mel Hankins- Harrison, Arkansas
2005
A. Mr. Hankins in completely correct - a deox step is necessary after the etch and prior to the anodize. I've become so accustomed to the two baths always being used together that I just think of it as one process, hope it didn't cause any confusion.
Good luck.
Compton, California, USA
2005
Multiple threads merged: please forgive chronology errors and repetition 🙂
Watermarks on Sand Blasted Clear Anodized Surface
Q. Dear Sir,
I am currently developing a anodizing process named "Peer Skin White Alumite" (also known as Satin-finished Clear Anodising) for our new product cosmetic.
We are using Aluminium 6061-T6 as the raw material and fabricate via Turning and Milling to our finished goods in dimension and tolerance. The surface roughness of the machined parts are monitored at 3.2Ra max.
The machined parts are then subjected to Sand Blasting Process to form the Satin Finished on the visible area. We have tried the sand blast media from Aluminium Oxide, Carbide, Glass Beads, or any combination of TWO compounds.
Then, these surface blasted parts are to subject to Clear Anodize process.
And, this is the problem that we are facing. We are not able to control on the color, gloss, texture of the clear anodize surface evenly for every piece in the treatment bath.
We are seriously looking for the solution to improve on the yield and process control on this process.
Thank you in advance.
Contract Manufacturer - Prai, Penang, Malaysia
2007
A. Since I can not observe the process, it is difficult to blame any one thing. My guess is the cause is in the blast process as it is terribly difficult to blast two parts identically, even with excellent automation. A factor might be media break down giving different roughness as the process proceeds through the day. Minor angle and pressure differences make a huge variance in the cosmetics of the part. Have you tried using one level finer blast media?
Mark a couple of parts for the top of the rack and a couple for the bottom of the rack to see if you can find a difference there, since the bottom gets a minor amount longer etch than the top does.
- Navarre, Florida
2007
A. There are media deposited in the surface.
Reduce your Blasting time (Ra too)and use and angle 60 to 90.
- Minneapolis, Minnesota, USA
January 2, 2008
? What is the range of color reading requirement in terms of CIELAB?
What is the gloss range requirement?
If the finished part somewhere shadowed, then the cause lies in the bead-blast, otherwise color, gloss, etc., out of control lie in your anodizing process or material.
- Singapore
A. Have you considered a mass finishing system? You can get surface uniformity; however, part size may be a limitation.
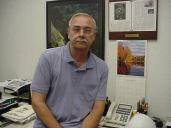
AF Kenton
retired business owner - Hatboro, Pennsylvania
January 6, 2008
Another source of discoloration could be contaminants in the sand blasting media (steel etc.) that are being pounded into the aluminum substrate. This is a problem that occurs when blasting cabinets are used for different materials.
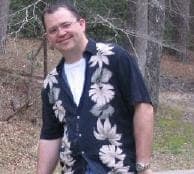
Ryan Cook
Toccoa, Georgia
January 12, 2008
Effect on surface finish of flash anodize
Great intellectual space, people. Thank you all.
What is the effect on surface finish to reverse flash the rack prior to anodizing? Are there any current/time parameters for this action?
- Bainsville, Ontario, Canada
April 27, 2018
Q, A, or Comment on THIS thread -or- Start a NEW Thread