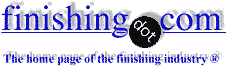
-----
Improving our citric acid passivation process
Q. We do cold passivation of components in citric acid. However, we use de-mineralised water to do the passivation. Final wash is also in DM water. Is DM water harmful to the passivation film, should we use regular tap water instead? Also, is hot passivation a better option? We do get a failure rate of approx. 3% in salt test doing the above passivation procedure. Moreover we observe that the components that have some sort of cut or pit tend to catch the rust. How can we passivate so that these components also do not rust.
Jack Stevenengineer - Istanbul, Turkey
2003
A. The use of DM water is critical to a proper passivation. It is acceptable to use tap water for intermediate rinse steps but I don't recommend it unless the cost of DM water is a prohibitive factor. I would also suggest an elevated temperature. ASTM A967 and ASTM A380 specifications will have the information your looking for. I would also recommend polishing any pits or irregular welds before passivation. Hope that helps.
Joseph Lockremchemical cleaning - Indianapolis, Indiana
2003
Q. Thanks but I read an article saying that Deionised water (which I assume is same as Demineralised water) strips the chromium oxide layer that forms due to passivation. Is that true? Also we do polish the pits but the pits are in microns, not even visible by naked eye. How do we make sure that the citric acid passivation takes care of such minor scratches or pits?
Jack Steven [returning]- Turkey
2003
A. We use steam distilled water at a conductivity or 20 microsiemens/cm2 or less for passivation baths and rinsing. Keep in mind that the passive layer does not form immediately upon rinsing. The film requires some time (minutes to hours)to form depending on temperature, environment, and drying method. The chlorides and iron in tap water would deposit on the cleaned surface and could cause problems later. I am less capable of advising you on the pits or inclusions in your welds. We receive parts that are polished to a sanitary finish and have no problems with "rust". An elevated solution temperature and longer immersion time may help. A nitric acid solution may be better suited to your application. I would refer to the ASTM A380 and A-967 specifications for advise on chemical selection.
Joseph Lockremchemical cleaning - Indianapolis, Indiana, United States
2003
A. citric acid removes iron from the surface and does not oxidize the nickel and chromium. Nitric Acid removes the iron AND controlled oxidizes the nickel on the surface so that the nickel will not continue to tarnish. Passivation means controlled oxidation.
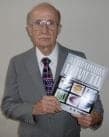
Robert H Probert
Robert H Probert Technical Services

Garner, North Carolina
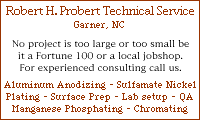
2003
A. I use DI in my A-967 passivation procedure largely for removal of chlorides in tap water. If DI strips the chrome oxide layer, what's the problem? That's all part of passivation. It may lead to a more uniform passivation once the cleaned part is exposed to air.
After years of using Nitric, I now use Citric style passivation. I feel the rinse is more critical due to the mild nature of the citric to dissolve the surface iron.
Last year, I ran some tests at one customer's corporate metallurgical lab. They wanted to see if A-967 chelant passivation was as good as the old ASTM A380
Nitric. We contaminated test coupons of 317L and applied both methods-Citric vs. Nitric. Both passed the copper sulphate
⇦ on
eBay or
Amazon [affil links] test with the exception of one tiny spec on the Citric panel. It seems they stamped the coupons for identification purposes using mild steel punches. One tiny spec of iron embedded in the impression of the letter remained after the chelant passivation. To me, it reinforces the importance of rinsing under pressure. I feel that spec may have been dislodged with a higher pressure rinse.
I clean large equipment using a spray approach rather than bath applications. I use at least 1500 psi and prefer 3000 psi for the rinse. Is a pressurized rinse possible for your application? Heat is also big plus.
- Monroe, Louisiana
2003
Deionized water is always preferred for rinsing if it is available and cost effective for the operation because it does not allow contamination of the surface with chlorine and other ions. It also will give you a spot free surface if your final rinse is clean.
Passivation with citric acid will always give you a better passive layer when the right formulation and procedure is used. The best corrosion resistant oxide layer can be formed using citric acid formulations and multiple deionized water rinses. If you need help with your particular alloy let us know. If you read ASTM A967 it gives you the definition for what passivation is.
ASTM A380
is not a passivation specification and should not be used for that. It is a recommended practice. A-967 is the ASTM passivation specification. A-380 has many good practices for cleaning, pickling, etc., and does contain some ideas for passivation, but it is not a specification.
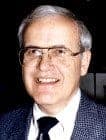

Lee Kremer
Stellar Solutions, Inc.

McHenry, Illinois
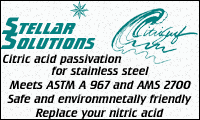
2003

this text gets replaced with bannerText
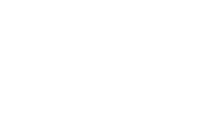
Q, A, or Comment on THIS thread -or- Start a NEW Thread