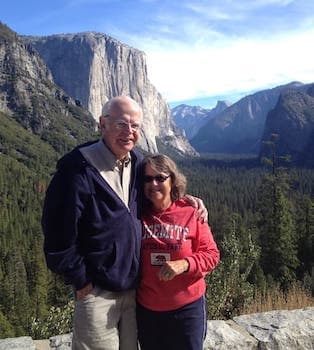
Curated with aloha by
Ted Mooney, P.E. RET
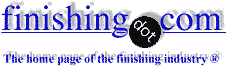
The authoritative public forum
for Metal Finishing 1989-2025
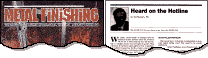
-----
Shop refinishing steel sleeves with Tin
2003
In the mid 1950's XXXX Motor company had a steel canister housing a large spring to assist in the roof operation of a convertible car. These telescoping steel canisters eventually rust out and the springs grown weaker over the past 40+ years. I'm trying to re-build the canisters with new springs and steel telescoping sleeves. I've already machined new sleeves from 18 ga. round welded tubing which is polished to a fine finish using 220 grit followed by 320 grit, 400 grit, 600 grit and finally 700 grit polishing pads. The "pre"finish of the telescoping tubes before metal finishing is almost chrome-like. Now here is the problem; the original 1956 manufactured telescoping steel tubes had a fairly high reflective finish applied to just the exterior of them. The finish seems to have been applied by either dipping in a hot pot and rotating the tubes with some sort of squeegee to wipe the solder-like finish (it is NOT chrome!) off. I'm trying to duplicate the finish in the shop without using a dipping hot tank. I'm the Tech Advisor for an East Coast antique car club and I see a need for somewhere between 300 to 2000 of these canisters as the original ones wear out and replacements can't be found. I can (and have) completely fabricated the whole canister assembly with all new parts and springs....it is the finish on the steel canister telescoping sleeves that I'm having a problem with!
THE PROBLEM: The original finish looks like TIN to me. I've tried Solder/paste without any additional solder and couldn't get a bright reflective finish. I then tried silver solder applied to the solder/paste and that still didn't get it. I followed that with an application of 60/40 tin solder and still couldn't get that bright reflective finish. All of the above applications were done with an acetylene torch and they were all wiped with terrycloth towel while the solder was in the liquid state. For some reason parts of the finish was bright in some areas of the canister but the finish was never uniform. If we re-mount the sleeves in a lathe and polish with
700 grit polishing pads we get a very smooth finish that resembles the original unfinished steel canisters, not that brite TIN reflective look of the original canisters. If we could duplicate the finish of a tinners solder paste BRUSH metal handle, we'd have what we're looking for.
THE QUESTION: How can I get that bright silver reflective finish on the canister sleeves in our shop? We are trying to get this prototype off the ground with a low initial investment even if the shop finishing time is excessive in the initial stages. We definitely have an immediate use for about 10 of these canister but until the marketing of a proper finished product is in place, we'd rather not invest in the cost to send these out to a metal finisher yet. More over, the cost to have 10 of these sets done will probably be considerably higher than 300 of them.
hobbyist, shop machine/lathe operator - Elkton, Maryland, USA
I'd guess the finish is zinc plating, although it could have been electroplated tin or cadmium or a few other platings, or it might well have been hot dipped tin as you seem to suspect. It would be great if your club had a member who worked in the car factory and could tell us what the finish was. But alternately the finish can be tested to see what it is. A plating shop may immediately recognize the finish or be able to easily test it for you.
I guess you already know that this is an electroplated or hot-dipped finish and the right way to duplicate it is to have them electroplated or hot-dipped in the appropriate metal. You quest may not fail, but I think it will. If I can reword it you are asking:
"Who has developed a process that, if the real costs were counted, costs ten times as much as electroplating, looks only almost as good, and isn't as functional?". In other words, practicality tells me that this finish was not created the way you think it was and/or is not what you think it is. Get one (or ten) zinc plated or alkaline tin plated or hot dip tinned and see where you are. Good luck.
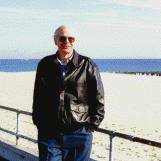
Ted Mooney, P.E.
Striving to live Aloha
finishing.com - Pine Beach, New Jersey
2003
Q, A, or Comment on THIS thread -or- Start a NEW Thread