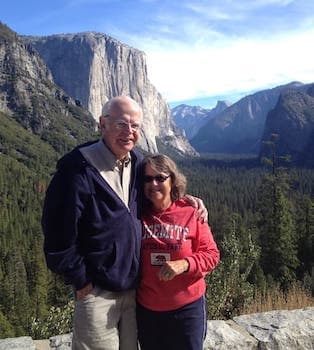
Curated with aloha by
Ted Mooney, P.E. RET
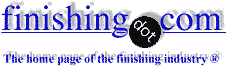
The authoritative public forum
for Metal Finishing 1989-2025
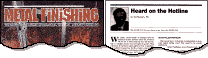
-----
Today's OEM car bodies: Zinc phosphated, e-coated, etch primed
Q. An article in the Feb. 99 issue of a major, nationally distributed auto body trade magazine contains a statement that there is no zinc phosphate coating on the exterior of many new late model vehicles -- that this process has been discontinued by manufacturers probably because of environmental concerns. I find this hard to believe. I was under the impression that zinc phosphate coating (by immersion or wet booth facility) of ALL mild steel panels prior to priming was & is universal among auto makers. Even if the zinc process is restricted someday because of environmental concerns would not some substitute coating be developed -- as opposed to merely priming bare unprepped steel as this article claims is being done? Does anyone at this forum have firsthand knowledge on this particularly regarding manufacturers in Detroit as opposed to import brands? Thanks!
Dave Propst-WW, Washington
1999
A. Dear Dave, most of the major auto makers use "electrogalvanized" steel these days in the manufacture of body panels; this can be single or double sided pre=plated with zinc or a zinc alloy of the particular manufacturers choice. This has eliminated the need for zinc phosphate coatings -- all they need now is an electrodeposited etch primer which I believe most of them use. Unprotected steel is a definite no-no to the major Auto manufacturers and the "electrogalvanized" steels are far far improvements on the old dip phosphates, which offered little if any corrosion protection but did provide a fabulous base for paints to adhere to. regards John . C . Tenison - Woods

John Tenison - Woods
- Victoria Australia
1999
Q. John, thanks for the reply. The PPG Automotive website describing their Powercron electrocoat priming process as used by OEMs does specifically reference the zinc phosphating of items prior to electrocoating. It states "Cleaning and phosphating are essential in achieving the performance requirements desired by the end user." That page was last updated on --. I would assume nothing has changed in the time since that was written but I seem to get conflicting answers to this, which is why I inquired if anyone has specific firsthand knowledge or data on this. Some confusion may be in the following fact. For many years automakers have used zinc plated steel to construct parts in select high corrosion areas such as rocker panels, gravel guards, and valence panels. Typically these panels presented severe paint adhesion problems particularly for the collision repair industry but did offer greater ultimate corrosion resistance. Rather, my question pertains to the entire body surface. What is actually under the e-coat on the outer body surfaces of today's car?
Dave Propst [returning]- WW, Washington
1999
Q. We have a problem with burns in electroplating of car bodies. We need to know the quality of the current and the voltage. At this moment we have current surge of 35 Amps lasting for 0,2 ms every 3,3 ms. That's the commutating period of one rectifier. This energy 3,3 ms that is implemented is about 1 Ws. That means that you need 3600000 Ws to generate 1 kwH.
Is this energy of 1 Ws/3,3 ms enough to generate burns in the process.
If you have time you are welcome to help us with this problem!
Best Regards
Service Engineer - Gothenburgh, Sweden
May 10, 2010
Hi, Kjell. To my knowledge, car bodies are not electroplated. Do you perhaps mean electrocoating / electropriming / electropainting?
Regards,
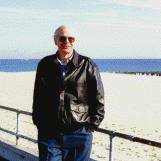
Ted Mooney, P.E.
Striving to live Aloha
finishing.com - Pine Beach, New Jersey
May 11, 2010
May 19, 2010
Hi Ted!
I'm not sure, because I normally work with rectifiers running DC motors. But as I know. After washing and cleaning they phosphatize this car body, and then it goes into this, could it be electropriming? The first coat that the car body gets. We get quality problems mostly on the right side of the car body (burns about 30 micro millimeter). Could this be caused by the quality of the current?
Best Regards
Service Engineer - Gothenburgh, Sweden
A. Hi Kjell. I guess neither of us have quite enough facts available, but I'd suspect a chemistry problem rather than an electrical one. "Burning" when used in the finishing industry doesn't actually imply something reaching an ignition temperature; rather, it's just slang for something that "looks" like burning. i.e., when there aren't enough ions locally available for the proper reaction, the electricity hydrolizes hydrogen from the water, causing a very rough, sometimes blackened, deposit which is called "burning".
Regards,
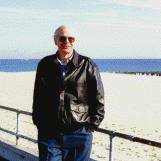
Ted Mooney, P.E.
Striving to live Aloha
finishing.com - Pine Beach, New Jersey
Q, A, or Comment on THIS thread -or- Start a NEW Thread