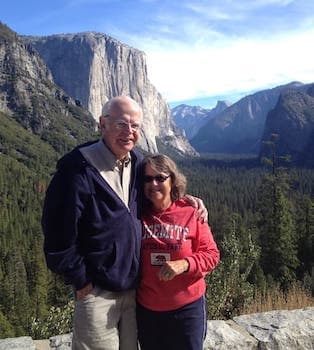
Curated with aloha by
Ted Mooney, P.E. RET
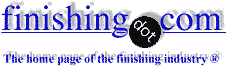
The authoritative public forum
for Metal Finishing 1989-2025
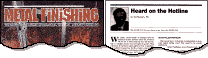
-----
Process Control of Solutions
My question is related to the maintenance of all process solutions. When the process solutions go out of spec what do you do with the parts? The process solutions that I am referring to are: Chromate Conversion Coating, Anodize, Etching, Deoxidizing, Alkaline Cleaning, Degreasing, etc. The Quality lab tests all of the solutions used by production, once per week. When a solution is nearing it's useful life it has always been difficult to explain what coarse of action is acceptable. Quite often the solutions are dumped prematurely. Quality management wants to know if a tank goes out of spec. do the need to reject all parts run during that week? My answer, as a Manufacturing Materials & Process Engineer, is that the parameters used to each solution are guidelines. Parts processed outside these guidelines are considered to be acceptable based on acceptable performance tests further down the production process ie. adhesion, salt spray, etc.
John P. McLaughlinaerospace - Moosup, Connecticut
1999
It has been my experience that even when the process analysis goes outside of specification limits, most people will continue to accept the parts as long as they pass cosmetic or performance criteria. I think there is a tendency for the "engineers" to create analytical limits that are far too tight. Many plating and surface finishing solutions are far more forgiving than we give them credit for, and can often be nursed along until you have the time to make the chemical adjustment, or dump and start over. Consider two set of limits: Control Limits, and Specification Limits (terms obviously borrowed from SPC). The first set are tighter and serve to trigger action such as chemical additions, dummying, or carbon treatment. They are the warning that it is time to do something, but you can still use the bath. The second set are the "DO NOT CONTINUE TO USE THIS PROCESS UNDER ANY CIRCUMSTANCE" limits. Shut down when you get there. Analyze your bath whenever you think you are going to be near the Control Limits. You can do a higher frequency of analysis until you have a sense of the necessary schedule. A week is way too long to wait for some parameters. For others once a month is often enough. You have to study the process to know what is right.
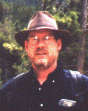
Bill Vins
microwave & cable assemblies - Mesa (what a place-a), Arizona
1999
We have found it useful to establish two criteria for tank chemistry control. The first uses the SPC concept of control or action limits. If the bath parameters fall outside of this range then some action is required. (i.e., add chemicals, regenerate acid, or dump bath.) The second is a wider specification or never exceed limit. If the bath parameters falls outside of this range then unacceptable products could result and the production should be quarantined pending further testing.
Chris Jurey, Past-President IHAALuke Engineering & Mfg. Co. Inc.

Wadsworth, Ohio
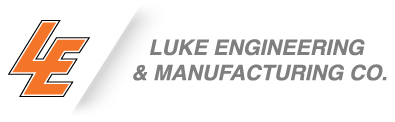
1999
Just to add one more item to excellent suggestions above: Implement a "deviation Signature procedure" for every lot processed after control limit is reached. This is signed by line engineer and approved by Engr. Mgr. Keep track of all deviations signed and numbeer of parts processed. Over a period of time, it will allow for modifications in control limits. Plus, it will force an action from Engg/production dept. This worked like a charm in where I worked before.
Mandar Sunthankar- Fort Collins, Colorado
1999
The Boeing position in this type of situation is as follows: Any parts produced in a solution which is identified as an out of specification condition must be rejected by Quality and sent in with a tag identifying it as discrepant material. The time frame for the out of spec. solution parameters can be identified from the last analysis and extrapolated to the current date. Engineering then can make a decision based upon physical testing, how far the solution is out of spec., etc. Parameters listed in our specs., are required, they are not merely guidelines. Frequently, chemical manufacturers will have a wide concentration range depending upon circumstance like soil loading etc., those make their way into specifications, however many solution parameters are critical, as in phosphoric acid anodize, or silicates in anodize seals for example. Further, any tank solutions when identified as out of spec. can not have parts processed through them. Process control tests such as salt spray, coating weights, are typically performed on a frequency ! determined by time, monthly, wee kly etc. Usually, the time frame the process control tests are performed in, is not the same as when the parts are actually processed. Typically, Quality will determine through history an action through prevention to eliminate this type of situation in the first place. One strategy used is "bleed & feed" in order to maintain solutions almost indefinately. Another strategy is quasi-SPC using moving range calculations.
Ward Barcafer, CEFaerospace - Wichita, Kansas
1999
I've read some good advise above and wholeheartedly agree with using SPC with two levels of action/alarm. The first being "process warning alarm" and the second "process out of spec warning". When the process reached the first level, it is time to take action to adjust the process back within those fairly tight limits. The second alarm is used to recognize when the process is about to go haywire, but still well before it actually causes performance problems. Next, I'd like to suggest two other ways in which to determine solution-life oriented controls.
1. Production oriented limits. This is a simple calculation that any engineer worth his salt can do. Count the number of parts, square feet, cubic feet, pounds, etc. of production that have been put through each bath before it is dumped (based on performance criteria). You only need to do this through three dump cycles for it to be "statistically significant". And you have just set up a preventative maintenance-type dumping schedule. Of course, the dump schedule may be different for each tank (more than likely). If you adjust the PM schedule for each tank forward slightly (a few days or weeks), you'll never get to the point where you have to dump for performance reasons (in theory).
2. Soil loading. cleaning tanks can be monitored for the amount of soil build-up (called "soil load"). Determining the limit is the same as above. Take a sample just before the tank is dumped and measure the "soil load". This will establish the limit. The same is true for rinse tanks and etch tanks. The "soil load" is determined differently for each tank. Rinse tanks for example the soil load could be TDS or ppm of cleaner dragged in. Cleaner tanks are generally measured for the percentage of oil in the tank, because as oil builds up in the tank it has the potential of re-depositing on the parts. Etch could be measured by TDS again or by the concentration of aluminum in the bath. Good Luck...


Craig Burkart
- Naperville, Illinois
1999
Q, A, or Comment on THIS thread -or- Start a NEW Thread