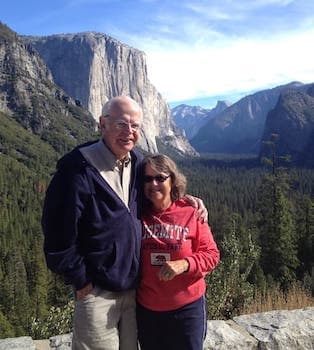
Curated with aloha by
Ted Mooney, P.E. RET
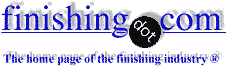
The authoritative public forum
for Metal Finishing 1989-2025
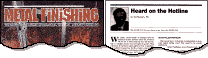
-----
Coating Selection for Ti Alloy
I have a need to plate or otherwise coat a titanium alloy component for wear resistance. I've read that titanium alloys can be chromium plated or electroless nickel plated. I've also read that there are more exotic coatings for these alloys in use today, but I have no direct experience with coatings on Ti. Are there any "war stories" I should know about?
John Ullman1999
Titanium is no where as easy to coat as steel or stainless. There is considerable disagreement on what is the best preplate cycle. After a Woods nickel strike, nearly anything can be applied. Getting to that point is where the difference of opinions are. Chose your shop carefully and see what kind of service warrantees they will give. Prior good results experience would be a large factor in a choice, at least initially.
The physical vapor deposition (PVD)folks will sign on here saying that there products are the absolute finest. If the part is small and dimentions are critical, I would definitely try a few, probably from a couple of different vendors.
Final choice of coating will be controlled by the application. Each has its own niche.
James Watts- Navarre, Florida
1999
Why not just nitride the surface and form TiN? Ion nitriding or some such process could do that.
Mandar Sunthankar- Fort Collins, Colorado
1999
1999
Have you ever experienced "wear " on titanium? The metal is so tough and chemically inert (due to the thin TiO*TiO2 layer on the surface) that perhaps only its own nitride can compete with it. You can use Titanium or Ti/V alloy for making eternal showels which will last for centuries in any condition of use. However you still can try to put a nitride on it, but you may end up with matte goldish color which is not beautiful at all (compared to Titanium nitride coating on steel). It is also possible to activate the surface with acids (nitric, sulfuric) and plate any other metal on it with comparatively high adhesion. The activation is better done on exposure to AC of 50-60Hz in solution (12-15V).
Anton CheglovThe hard part about coating titanium is the oxide. It makes adhesion difficult. We've had success coating titanium with TiN and ZrN using high energy ion bombardment during the deposition. TiN is a good coating, but ZrN is prettier and generally more wear resistant. If you're interested, we be happy to discuss coating some samples for you.
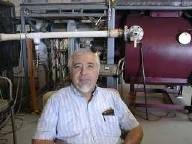
Jim Treglio - scwineryreview.com
PVD Consultant & Wine Lover
San Diego, California
1999
Maybe what you are really looking to do to reduce wear and galling, John, is to anodize the titanium? Specialty shops like Tiodize and Titanium Finishing offer functional anodizing of titanium (it's done in an alkaline solution, and is quite different from the decorative anodizing you'll read about in other letters here).
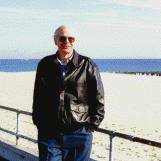
Ted Mooney, P.E.
Striving to live Aloha
finishing.com - Pine Beach, New Jersey
1999
Q, A, or Comment on THIS thread -or- Start a NEW Thread