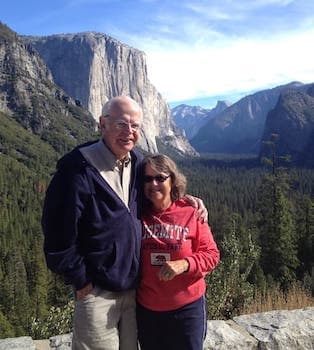
Curated with aloha by
Ted Mooney, P.E. RET
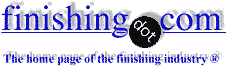
The authoritative public forum
for Metal Finishing 1989-2025
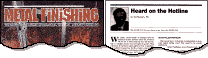
-----
Nickel plating stainless steel tubing
1999
I am trying to find a way to nickel plate the inner surface of stainless steel tubing. (usually 2" long with a small inner diameter of 1/16"). It is not a problem for the nickel to be on the outside of the tube also, but it is the inner part that is critical. Our electroplating process will only plate inside the tube a distance proportional to the diameter. Is this because there is no current flow due to shielding? (tube becomes a gaussian surface?) Does anyone have any suggestions? How about electroless? Can someone suggest and electroless strike for stainless steel?
Any info would be greatly appreciated.
Allan Cass1999
While electroless copper is used on PWB's with awesome aspect ratios, it is a specialty product and is on relatively thin material.
I am not aware of any electroless nickel that will work well, simply because there is no cheap way to force the solution thru the hole. Air agitation will be random and a pumped rig will be slow to fixture.
The OD was not given, but if it is large, it will be enough of a heat sink to slow down the initiation of the EN on the ID.
SS requires good cleaning and activation. That is not simple with an ID as small as yours.
Virtually all SS receives a Woods Nickel strike. The middle of this 2" bore is not going to get any significant amount of strike, thus probable poor adhesion.
It can be done, but I doubt if there are very many shops that can do a great job.
It will be expensive, relative to most plating jobs.
Will a better grade of stainless work? If strength is a criteria, can you increase the size to compensate? It will be cheaper and less painful if you can avoid plating.
James Watts- Navarre, Florida
Allan, are we talking about just a few parts or a large volume? We could look into it if there is a future.
Mandar Sunthankar- Fort Collins, Colorado
1999
Thanks for the responses. We only need about 20 per month, but the problem is when we need them, we needed them yesterday. (you know how that is) We have a shop we have been sending them to and had good results, but it takes a week or so to get them back. I was hoping someone would have a quick fix so I could do them in-house, but if that isn't possible I think I might try another option besides SS. Thanks again, Allan
Allan Cass1999
As a plater, I was always amazed that a engine part to be overhauled could set for a week at incoming QC, but when it got to plating, it had to be out in 12 hours when it required a 24 hr run.
Three obvious solutions: Plan further ahead or keep 5 on the shelf or pay the plater a premium for faster turnaround.
James Watts- Navarre, Florida
1999
Your enquiry about plating the inner surface of a tube is an interesting one. We specialize in Chemical Vapour Deposition - especially deposition of nickel. The CVD process is a gaseous one and therefore the plating of the inside of a tube is not any problem. We have coated or plated tubes from 2" ID down to as small as to 350 microns ID! (Those little guys were about 1" long!)
When the nickel deposition starts, it will coat a layer of nickel onto anything that is heated appropriately and is clean.
CVD of nickel and nickel alloys might give you all sorts of alternative possibilities to consider. It's up to 25 times faster than electro-forming too.
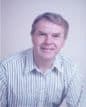
Mick O'Meara
- Toronto, Canada
2000
I wish to know the process for plating (zinc yellow passivation) for tube of dia 12.7mm, 1.6mm of length 700mm.
We require to plate the tube inside also.
Looking for you reply
shivaprakash- Bangalore,Karnataka, India
2000
If you electroplate them, the thickness of the deposit will be proportional to the current density at that position. The current will follow the path of least resistance, so the current density inside the tube, except right at the ends, will be zero for conventional rack plating.
You will only be able to plate the inside of these tubes with auxiliary anode rods running through them, and a continuous flow of solution. It is possible but probably impractical.
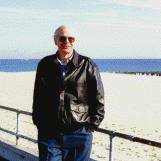
Ted Mooney, P.E.
Striving to live Aloha
finishing.com - Pine Beach, New Jersey
2000
Q, A, or Comment on THIS thread -or- Start a NEW Thread