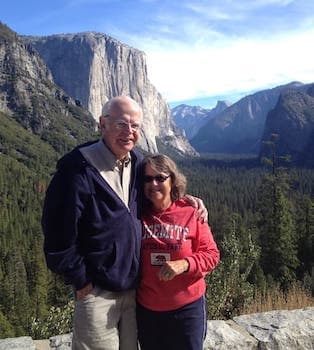
Curated with aloha by
Ted Mooney, P.E. RET
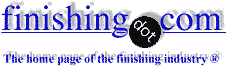
The authoritative public forum
for Metal Finishing 1989-2025
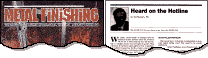
-----
Solutions to Problems electropolishing stainless castings
Q. We have encountered dark, burnt-like marks on a 316L stainless steel part after the electropolishing process.
These defects penetrate through the 3mm thickness of the material and exhibit characteristics of carbon diffusion, as the affected areas are carbon-rich and somewhat brittle.
What could be the source of these? These are seen after electropolishing.
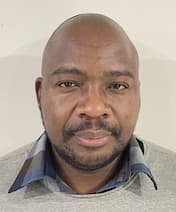
Zwia Mudau
- Auckland [New Zealand]
September 19, 2024
? Hello Zwai,
Are you doing the electropolishing in-house or sending them out? Is this a casting, a small coupon, a large flat sheet?
Unfortunately, figuring out what went wrong solely from a zoomed in photo of the defect, with no process information nor real-world info, is at best a wild guess. Can we get a pic of the whole component to understand what you are dealing with, rather than only the defect?
My guess is that the component touched the cathode, which might be a reasonable guess if it was a large, thin, floppy sheet being processed, but might be a silly guess in other situations ... and we have nothing to go by yet. Thanks!
Luck & Regards,
Ted Mooney, P.E. RET
Striving to live Aloha
finishing.com - Pine Beach, New Jersey
Q. Hi Ted,
Thank you for your response.
The part in question is a 316L casting with a hollow spherical shape with a wall thickness of 3 mm and a diameter of approximately 400-600 mm. Unfortunately, I can't share full photos or drawings here due to client IP restrictions.
There isn't much information available about these types of defects, but the closest reference suggests it may be related to an electrical arc burn defect.
Have anyone seen similar images? If I could be directed to an electropolishing defect atlas or previous related research papers would also be really helpful.
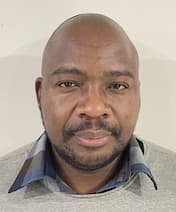
Zwia Mudau [returning]
- Auckland, New Zealand
September 23, 2024
and Chemical Polishing
of Metals in
Research and Industry"
by W.J. Tegart
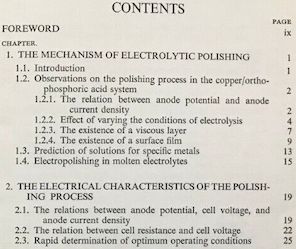
on eBay or
AbeBooks
or Amazon
(affil links)
A. Hi again.
I'd like to ask again if you are doing the electropolishing in house or sending it out because if in house you should be able to see some things for yourself and perhaps describe the situation to us. If the parts were sent out, you have nothing to go by but the appearance of the defect ... and the shop which processed the part might possibly even stonewall you about it.
I suspect that you are correct that it is an electrical arc burn, but I'm not sure what your relationship to the electropolishing process is, such that you know what that means ... but the shop which electropolished them certainly does :-)
An electrical arc burn means that this casting, which was connected to the "-" side of the power supply actually mechanically touched the cathodes connected to the "+" side. It can happen, especially if the 400-600 mm diameter is a bit too large for the cathode rod spacing which it was inserted into. If that was in fact the cause of the defect, the shop which processed the parts could not possibly have missed the fact that it happened! It would cause a bright flash like arc welding because that's pretty much what it was.
I doubt that anyone is writing articles about components touching the cathodes during electropolishing or compiling photos of it, but I think it's time to call the electropolishing shop for a discussion. It's possible that an operator did this and did not tell management and managed to get the part shipped without inspection. The shop may even be effusively apologetic and appreciative :-)
Luck & Regards,
Ted Mooney, P.E. RET
Striving to live Aloha
finishing.com - Pine Beach, New Jersey
Q. Hi Ted, the polishing is outsourced.
There is no evidence found yet linking the defect to casting/foundry processes hence I am now also looking at the possibility that this may be related to the electropolishing process. I do not have industry knowledge of polishing hence I needed to test my theory.
Apart from the part (anode) making contact with the cathode, it also seems like poor contact between the racks and the part can be another source of arcing.
I was hoping that this defect is well known in the metals finishing industry and there would be information on it. Thank you for sharing your views so far, it has been very helpful - much appreciated.
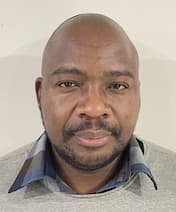
Zwia Mudau [returning]
- Auckland New Zealand
September 24, 2024
A. Although poor contact can indeed be a problem in electropolishing and similar applications, something simple to envision is that the conductivity of watery solutions is hundreds of times lower than the conductivity of metals. With a 12 to 24 volt DC power supply, you're only going to be able to push rather limited amperage through the resistance of the electropolishing solution; you're simply not going to get an arc that can burn all the way through 3 mm thick cast iron from a loose contact. For that kind of arc you need a flow of current that you'll only get from the near zero resistance of metal-to-metal contact.
I think the component physically touched the cathode and that the electropolishing shop manager will own up to what happened even if he didn't see it or previously know about it. Good Luck, thanks for visiting. Let us know when you learn.
Ted Mooney, P.E. RET
Striving to live Aloha
finishing.com - Pine Beach, New Jersey
⇩ Related postings, oldest first ⇩
Q. We have had constant quality problems from vendors who electropolish our 15-5PH stainless investment castings. Sometimes the parts come out fine, but other times the surface is very frosted or pitted. The outcome is almost random, and bad results end up in several thousand dollars worth of scrap. It makes you want to pull your hair out.
I have tried to work with our vendors to set up some controlled experiments and narrow down the sources of inconsistency. However, both of my vendors refuse to work with us, stating that the process is "secret" and I am not allowed to work with them. This is ridiculous.
I have some background in the field and have read many publications on electropolishing, but without a laboratory set up, I cannot determine the problem exactly. My questions are as follows:
1) Are investment castings always inconsistent in polishing, and if so, what causes this randomness?
2) When we heat treat the parts, (1025 °F for 4 hours), the stainless turns brown. I believe this may be a nitride coating from nitrogen present in the air. Would this thin brown tinge be a source of our problems?
3) When the parts are machined, we use a coolant. We then clean the parts very carefully before heat treating. However, I am wondering if any residue from the coolant is diffusing into the metal when heat treated, and then comes out during electropolishing. Is this reasonable?
4) How hard is it to make a small laboratory set up. I commonly find 15 gallon containers of electropolishing solution, but is there a place to buy 1 gallon?
Thanks for any help.
Sincerely,
Tim Tylaskamarine hardware - Mystic, Connecticut
1999
A. Any pre-existing surface condition on the castings is critical to the resulting electropolish finish. This does not preclude that your vendors are causing the problem, which is always a suspicion when they refuse to work with you.
Investment castings can have surface residue from the casting process, in addition to porosity and inclusions that can affect the polishing outcome. Machining lubricant residue can result oxide films, especially after heat treating, which are also potential problems. I don't think that the machining lubricants are diffusing into the metal, nor is the metal picking up significant nitrogen from the air at 1025 °F.
Laboratory analysis of the surface physical and chemical condition can provide you with much information about your processes and possible affects on electropolish results. We have had some good successes in using surface analysis to troubleshoot electropolishing problems. The analytical plan could be tricky if the problem is truly random.
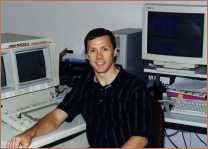
Larry Hanke
Minneapolis, Minnesota
A. For what it is worth I concur with Larry. It is important however to realize that everything that has been done to the material will have a effect on the electropolish process.
Most people understand that e/p is generally the last process that the part will receive prior to shipping. The electropolish process is so affected by the other treatments that in order to maintain any degree of repeatability in the finished product all facets must be documented. If the heat treat changes or the type of soak or the material isn't exactly the same every time the results will almost assuredly be reflected in the electropolish. I agree with the comment about your vendors not working with you. Electropolishing isn't rocket science. Anyone who tells you their process is proprietary is pulling your chain.
Greg Godbeyelectropolish - Fountain Valley California
Strange black residue appears on 15-5PH stainless after electropolishing
Q. Strange residue left on stainless after electropolishing I have a large number of 15-5PH stainless castings electropolished by a vendor, and frequently there appears a strange scale-like residue left on rougher sections of the parts after we receive them back from the vendor. This residue is brownish black and can be physically scraped off with a knife, but not without a lot of work. The residue is generally found in patches and appears to be perhaps a few thousands of an inch thick. It is really stuck on the parts almost as though it were baked on enamel. Most of the time, it is located in interior slots, blind holes or cavities of the casting. Never has it appeared on any pre-machined surfaces. Only on cast surfaces and mostly in slots or interior surfaces.
The vendor has demonstrated that if the parts are left in the electropolishing tank for long enough, this residue eventually disappears. However, the parts are then over-polished and are well beyond tolerances. As an initial suggestion, the vendor thought that the parts had some oil or other impurity on them before they were heat treated. We then took some raw parts and boiled them in approx. 10 Molar sodium hydroxide solution for 45 minutes. The parts were about as oil free as they could get. These parts were heat treated (1025 °F in air furnace) and electropolished. The same black residue still randomly appeared on the casting after electropolishing, although perhaps not quite as much.
The next suggestion was that the air furnace was creating some type of oxide scale on the parts, and this scale was what was responsible for the residue. We next took some raw parts, boiled them in the sodium hydroxide solution as before, and had them heat treated in a vacuum furnace. Titanium chips were packed around the parts to insure that every last trace of oxygen had been removed. The procedure was very expensive, but little to zero oxidizing occurred. It was hard to tell that some parts had even been heat treated. A sample of these parts were next electropolished, and the same residue again appeared although now to a seemingly lesser extent. Another sample of the parts were taken from the vacuum furnace and additionally glass beaded to insure that absolutely no anything was present on the surface. These ultra clean parts were electropolished, and again the black residue appeared to the same extent as the non glass beaded parts.
Next, I took some of the residue itself and tried to dissolve it in various solvents. Solvent #1 was MEK / methyl ethyl ketone. The residue did not dissolve. Solvent #2 was methylene chloride. Again, very little to no dissolving took place. Solvent #3 was toluene with no dissolving. Solvent #4 was approx. 20% nitric acid at room temperature. The residue seemed to dissolve slightly, and definitely softened up. Solvent #5 was a 45% nitric acid bath at 130 °F for 30 minutes. The residue dissolved quite a bit. The bath time was then increased to 45 minutes, and at this point, at least half of the residue on the parts did indeed dissolve away. However, this treatment was very harsh on both equipment and operator and was not something we could do on a production basis.
My questions:
1) What is this residue and how can we prevent it from occurring?
2) Is there any easier way to dissolve away this residue short of the 45% nitric bath?
Any responses would be greatly appreciated. Thanks. Sincerely,
Tim Tylaska [returning]marine hardware - Mystic, Connecticut
A. Dear Mr. Tylaska, The clue to the problem here is the fact that this smut occurs to quote you "Most of the time, it is located in interior slots, blind holes or cavities of the casting". These are areas with low current densities compared to the rest of the part. The smut is actually residual iron left on the surface since most electropolishing solutions attack the other elements such as nickel or chrome faster than they do the iron. Additionally, before I offer one possible solution, I would like to point out that any surface clean enough to hold a water break free surface is clean enough to electropolish, and boiling in caustic in not required. A suitable electrocleaner should do the job. That said I believe the use of auxiliary cathodes located near these areas on a separate power supply will solve the problem. If for whatever reason that does not seem feasible, then increasing the solution agitation should help. The other part of the solution to the problem is in your hands, not the electropolishers'. Give the rough areas a light sanding to eliminate this roughness before they are polished. Electropolishing reacts much more favorably to removing sanding marks than to casting roughness.
Anthony J. Coveyelectroformer - Corona, California
Ed. note: Super answer. Thanks Anthony.
Q. Hi
I own a small investment casting foundry in the UK and experience the same difficulties with Electropolishing. The results are so inconsistent no matter what supplier we use. We solution anneal our parts with nitrogen and 4% natural gas atmosphere. The castings have a light greenish brown tinge when finished. Even with parts cast in the same alloy batch, heat treated at the same time and finished in the same shot blasting machine, there are mixed results. We suspect that the shot blasting process may be trapping oxides and crud under the surface, peening over, and not then being eroded away completely by the Electropolishing process.
The inconsistent results have driven us to proposing us to offer Electropolishing followed by glass bead as an alternative finish.
If anyone has any suggestions please post a response.
- Devon UK
February 15, 2013
A. We have some experience in ss casting electropolishing.
adv.
It might work in Universal Electrolyte. Contact us for samples testing.
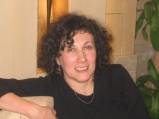
Anna Berkovich
Russamer Lab

Pittsburgh, Pennsylvania
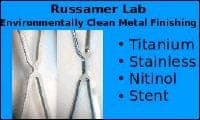
Hi Anna,
many thanks for the suggestion.
We have recently subcontracted a batch to vacuum annealing.
The results look very good; we will continue to undertake the heat treatment via this vacuum process and feedback our findings. I will also send a few samples to you for processing.
- Devon UK
Q. Hi,
My name is Aron and I am a Quality Engineer and I am experiencing a problem which I hope some of you have seen and can tell me the cause (my supplier is less than helpful). We have some stainless steel (14-4PH H1025) castings which go thought a heat treatment process and then electropolished. Some are developing brown staining, the almost look like they have measles!!! Has anyone experienced something like this before? If so, what causes it?
Thank you for taking the time to look at my query.
Aron WalkerQuality Engineer - Bournemouth, UK
August 19, 2021
A. Your problem looks like bleed-out from porosity in the castings. Try improving post electropolish rinsing - longer times or back-and-forth between hot and cold rinses.
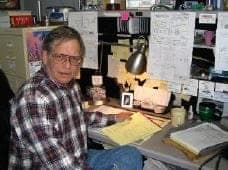
Jeffrey Holmes, CEF
Spartanburg, South Carolina
Thank you Jeffrey for your response. I will pass this on to our supplier and hopefully the condition will improve.
Thanks again.
Quality Engineer - Bournemouth, UK
Adv.
Aron, you can send us a small piece of this cast SS. We will adjust our Universal electrolyte for this alloy. After that we can provide complete chemical know-how composition, so you can mix the electropolishing solution in-house. Unfortunately we do not sell the Universal Electrolyte retail.
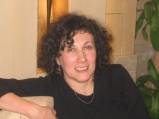
Anna Berkovich
Russamer Lab

Pittsburgh, Pennsylvania
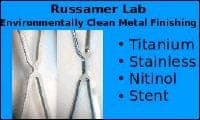
Q, A, or Comment on THIS thread -or- Start a NEW Thread