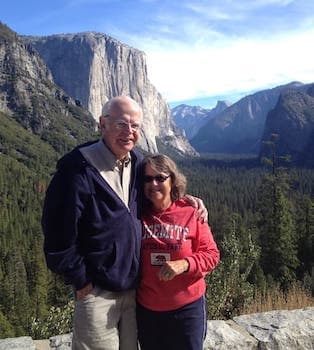
Curated with aloha by
Ted Mooney, P.E. RET
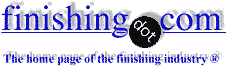
The authoritative public forum
for Metal Finishing 1989-2025
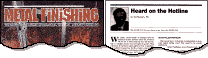
-----
Iron Electroplating problems (Electrodeposition of Iron)

Q. Iron Plating is a hard process to get correct. Once you do get the correct mixture of chemicals, then having the anode do its job is a different story. Still learning the whole process and looking for advice on plating liners for large Engines
Jason Scott- Texas
May 25, 2023
⇩ Related postings, oldest first ⇩
Q. We are looking for information regarding "iron plating". Looking for up to date formulations and compatible brighteners. Also would like to find out about how to overcome pitting on the plated parts caused by gassing during the process.
Leo Corbeil- Canada
1996
A. Good luck, this is a tough one, Leo!
Lowenheim's "Modern Electroplating"
[on
AbeBooks,
eBay, or
Amazon affil links]
has a 16-page chapter on iron plating, but I know of at least two manufacturers of soldering iron tips, and two jobshops that have struggled with iron plating over the past two or three years. The tendency of the iron to oxidize introduces a continuous problem to be addressed -- perhaps mechanical agitation should be used rather than air agitation. Successful iron plating techniques tend to be more closely guarded than most other plating techniques. I hope someone here will offer tips :-)
I think your best bet may be to talk to a process supplier regarding their proprietary iron plating baths, or to retain a consultant on this one. But you may find some general tips with a computerized literature search for 'iron plating' or 'soldering tip plating'.
Regards
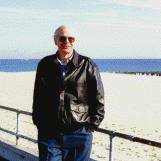
Ted Mooney, P.E.
Striving to live Aloha
finishing.com - Pine Beach, New Jersey
A. I am responding concerning Iron Plating. I am the General Manager of a chrome and iron plating facility in the Dallas, Texas area. Iron Plating is alive and well and we are successfully doing it on a large scale.
Calvin RiggsDallas, Texas
Multiple threads merged: please forgive chronology errors and repetition 🙂
Electroplating (Electrodeposition) of iron deposits
Q. Does anybody electroplate iron deposits?
Derek VanekIndependence, Ohio
1998
A. Dear Mr. Derek Vanek,
I have some experience of ductile Iron plating. We plate tips of soldering iron tips with iron. The deposits are subjected to high temperature stresses and stress due to differential expansion. At present the job is being done on a lab scale. The deposits are quite successful and users are happy. The same technique should be upgradable for bigger jobs.
- Pune, Maharashtra , India
A. Yes. Currently the only application I have come across is for the plating of soldering iron tips. The iron is plated over copper to enhance the heat "holding" capability of the tip.
At one time, iron plating was very popular for electroforming applications, but with the advent of sulfamate nickel plating, iron was phased out.
- Garfield, New Jersey
Iron plating onto copper base
Q. Sir,
I'll make a soldering iron with copper base. The lead must bond to the iron when it is dipped.
We tried some iron plating but it won't work. Maybe there are other chemical additives for the iron plating?
Thank you very much.
fabrication co. - Philippines
2005
A. There is a well used commercial iron plating solution based on ferrous chloride, hydrochloric acid and calcium chloride. It has been used for nearly a century, obviously with some success. From my experience, iron plating is very inefficient and not very easy to get a good deposit. As far as additives and formulations are concerned, it would be helpful if you told everyone what you were using, how you are running the bath and what sort of results you are getting.
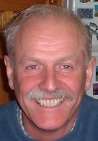
Trevor Crichton
R&D practical scientist
Chesham, Bucks, UK
A. Also, iron plating is one of the baths where air agitation must not be used because it oxidizes the iron. Mechanical agitation only.
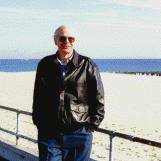
Ted Mooney, P.E.
Striving to live Aloha
finishing.com - Pine Beach, New Jersey
Q. I would like to know how to plate steel onto copper wire. It's my understanding that soldering gun tips are steel over copper. My hunch is that ferric II acetate would be the solution? But I am no chemist.
And I imagine an appropriate applied voltage would be about 1 volt?
I use #12 copper wire to make my own tips, but the copper seems to dissolve away, presumably into the solder...
Looking at the problems of power supplies, by the way, a small battery charger
⇦ this on
eBay or
Amazon [affil links]
with the 118 VAC input controlled by a dimmer from home depot? Just a thought - have not built it.
- red bluff California usa
June 7, 2015
A. Surely it is an iron deposit and not a steel deposit.
With a Manual type battery charger plugged into a Variac, you can control the DC output fairly well. Automatic battery chargers don't work well at all for this.
Read this
www.finishing.com/379/18.shtml
To iron plate (or to do any other type of plating), you generally desire a deposit that is smooth, hard, and adherent (doesn't peel off).
This is easier said than done, especially when you're making things up as you go along. I don't think you know enough yet to make any decisions as to how to do this and you don't know what questions to ask. Searching (and studying) this forum for "iron plating" will get you there much faster.
If you really want to do this, do it right. You first need to find a professional formula for an iron plating bath, preferably found on finishing.com - not on youtube; not on one of those how-to-do-it sites; not one using common household chemicals. Most of these don't produce hard, smooth, adherent deposits. If possible, pick one that operates at room temperature. Order all of the chemicals in the formula (eBay is about the cheapest)and buy a scale. Make up the bath as per the formula.
Now the hard part. You must learn how to best clean the copper so it will accept the iron deposit. Peeling's not good. You must learn how to select the proper amperage. What type metal will you use as the anode? When the bath chemicals get out of kilter and starts producing lousy plating, what do you do? These are only the tip of the iceberg. Read. Read. Read. Study.
Precious Metals Refining Consultant - Nevada, Missouri, USA
A. I would suggest closed loop argon agitation with exhausted gas going through a condenser/filter/separator before reentering the loop. This has improved on my copper and nickel plating.
Sam Blakesley- Sulpher Springs Texas
August 16, 2020
Q, A, or Comment on THIS thread -or- Start a NEW Thread