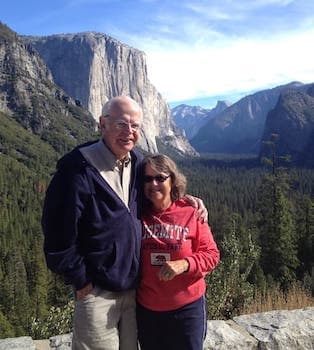
Curated with aloha by
Ted Mooney, P.E. RET
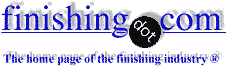
The authoritative public forum
for Metal Finishing 1989-2025
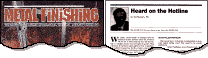
-----
Recovering silver via electroplating
I'm interested in producing a deposit of silver on a cathode (either rod or sheet, could be Fe, C, Ta, Nb or any other material I have access to) However my intention is not for decorative purposes but to produce pure silver from a nitrate solution in the form of a solid crystalline mass or tree or plate,(or like typical electrowon material) something that won't fall apart.(as alternative could use silver sulphate or it's NH4 complex). Books don't go into much detail aside from obtaining the usual crystalline powder which does not interest me. Also interested in similar procedure for IRON, Cr, GOLD. Suggestions regarding bath composition, voltage,current density etc...REMEMBER, not to plate but to obtain pure,solid or heavy crystalline mass of metal starting from a pure electrolyte solution of such. I'm familiar with the related regents(I use them all the time in lab) as well as their hazards.Work will most likely be done under fume hood.
PLEASE REPLY THANK YOU/GRACIAS,
university student;hobbyist - Madrid, SPAIN
2003
2003
Sounds to me like you need a plating bath(s) or an electroforming bath(s), more than anything.
In order to give a good answer, I would need more information. What is your goal? What are you trying to do? How much do you want to do? What is your starting material? If you give me some details, I can narrow in on your needs.
A traditional, electrolytic, silver purification cell uses silver nitrate as the electrolyte. This produces a pile of loose, very small
(20 mesh?), heavy, 99.99% pure, tree-like (microscope) crystals , making it easy to filter, rinse, and melt. This is why the nitrate was chosen. I know of no nitrate solution that produces a sound adherent deposit. Likewise, the sulphate. The NH4?. I doubt it. Also, I don't like ammoniacal metal solutions. They tend to blow up.
In the new non-cyanide (almost) world, people have been trying to come up with non-cyanide silver baths. On the internet https://www.google.com/search?hl=en&ie=UTF-8&oe=UTF-8&q=%22non+cyanide%22+silver+plating&btnG=Google+Search they seem to be either immersion baths (VERY thin deposits) or alkaline baths. http://www.metal-plating-chemicals.com/silver-plating-article.html By the plating characteristics listed, the alkaline baths sound like they are composed of silver sulfite. If similar to gold sulfite baths, this would require the silver becoming a cyanide, then a phosphate, then a sulfite. Not that easy.
It sounds like the alkaline baths on the market use soluble anodes. IF this is so and IF you're starting with pure silver metal, you might be able to buy a starting bath, feed a bagged titanium anode basket with silver shot (silver melted and poured into a 3 foot tall stainless container filled with water), periodically, and plate pure silver on the cathode. The solution might last a long time, with proper care. Ask the manufacturers.
Unfortunately, the best of all is the old double silver cyanide, High Speed solution, sold by some of the same people. It runs rings around the others. You can feed it and plate with it forever, as thick as you want, as pretty as you want, if you keep the contamination out of it and treat it for when it gets old. All of this at near 100% efficiency. If you go cyanide:
1)Do it with a commercial solution and ask the manufacture a ton of questions about safety and the bath's usage. When you buy a bath, you are buying their expertise. At least, it used to be that way. If you have some commercial plating knowledge, make up your own solution out of a book. I like the older Metal Finishing Guidebooks. I have a 1968, written when information was more freely passed out.
2) Study the operating instructions and read some plating texts, before you begin.
3) Always use excellent exhaust.
4) Keep any acids in another room. Acids and cyanide mixed together produce HCN, the same gas they used in the prison gas chambers. They lowered cyanide eggs into sulfuric acid.
5) Keep it out of your mouth and your eyes and off your skin and clothing, in order of importance. If I remember right, it only takes
.003 gms to kill by ingestion. I may be a decimal point off.
6) Wear good $8 rubber
rubber gloves
⇦ this on
eBay or
Amazon [affil links] and a
face shield
⇦ this on
eBay or
Amazon [affil links]
, at the minimum. Cuff the gloves to prevent solution from running off the gloves and onto your arms or clothing. Wash your gloves before removing them. If you get a pin prick in the gloves, get a new pair.
7) When hot, steam carrying some ammonia
⇦ this on
eBay or
Amazon [affil links] and a little bit of cyanide comes off the surface. If the skin is constantly exposed to this, it will lead to produce "Cyanide Itch", a rash of little super-itchy blisters. If you get away from the fumes for a few days, it clears up.
8) Read the Material Data Sheet on sodium or potassium cyanide.
9) Obtain a Cyanide first aid kit, keep it near, and learn how to use it.
10) Don't eat, drink, or smoke around cyanide.
11) Use common sense. Respect the cyanide.
12) Clean up spills when they happen.
13) Work with a partner present, in case something happens.
14) Cyanide is safe and pleasant to use if you know and follow all of the rules. It's not something to guess about.
15) Adhere to state and federal laws, concerning waste and fumes.
16) I could tell you real stories about each of the above 15 points. I'm sure I missed some.
Regards,
Consultant - Houston,Texas
2003
Mr Owens
Thanks for your response. To give you a few more details, I will use an insoluble anode(tantalum, titanium, pyrolytic graphite are my choices...I'm open to suggestions)
My intention is to refine silver. I have about 200 grams of silver nitrate and some sulphate(also some metal).I'm not going to take it to a refinery because the amount isn't worth the hassle.Besides I have personal interest regarding the technique. What I'd like is to produce a massive crystalline deposit but not like copper immersion in AgNO3 which are microcrystals. I've seen rather large (1 inch) dendridic tree-like silver(weighing several grams) produced by cathodic electrodeposit. THAT'S WHAT I'M AFTER. If not then at least a very thick deposit(massive plate)which can be later stripped from the cathode.(similar to cathode nickel or cobalt when it comes from the refinery).Or if not then just a massive plate out of metal...like in electroforming.
I know that using the nitrate for decorative plating does not produce desirable finishes , however I was thing that maybe for what I want it will do...? I also have some sulphate which isn't very soluble in water but more so in NH4OH.But your right regarding the explosive nature of Ag ammonia complexes.(won't go there)
Cyanide bath would be my last option.Thanks for the tips regarding the cyanide.You're absolutely right with regards to handling it.I have used KCN in the past in analytical chemistry. I must say however that KCN is no more toxic than mercury,lead,cadmium,nickel,chromium,beryllium,thallium, etc.... and the list goes on.I feel that we tend to give more attention to CN- because of its fame as a war gas,and poison of choice for murder.Other inorganic salts, gases and lets not forget organics, deserve as much RESPECT as CN-.I believe that chemical knowledge and laboratory safety along with common sense and hygiene will rule out most risks regarding the handling of chemicals. I have KCN, NaCN and have used them in the past in organics so I'm familiar with there nature. If there's an easy substitute I'll take it, if not then I have no inconvenience handling it.
Again thanks for your reply and hope to hear suggestions from you.Also looking for same conditions for Fe, Cr and Au...?
THANKS
- Madrid , SPAIN
2003
Javier,
I'm trying to zero in on your problem. As I understand it, you have about a half pound of silver, in several forms, and you want to convert this to massive, solid, silver dendrites, through electrolytic means. Is this correct? If so, I agree. They appear, rarely, in the earth as native silver. They are beautiful.
You use the word, "refine". To me, this means re-fine, or purify. Do you mean refine or do you mean convert? In the plating industry, treeing (formation of dendrites) is always undesirable. When we see it, we take steps to get rid of it, such as better filtration, better agitation, adjusting the constituents of the bath, or fixing electrical problems. You want trees. I know of no system that intentionally produces trees. The cathode nickel that I've used is more nodular than dendritic, and only forms on the high current density edges of the deposit. Do you want nodules or trees? A main factor is the condition of your 3 types of silver. Is the AgNO3 in crystalline form or is it dissolved in water, or something else. Is the AgNo3 pure or are there other metals or chemicals associated with it? Same questions with the Ag2SO4. Is the metal pure or is it Sterling or something else?
I think you're on the right track with the silver nitrate. It seems to be the only matrix that will immediately start treeing upon making electrical contact. The others tree over time. The problem is controlling it. I have much experience in operating Thum silver purification cells. The starting ingredients are about 60 gm/L silver nitrate, 40 gm/L copper nitrate
⇦ this on
eBay
or
Amazon [affil links]
, pure water, and about 3-5% free HNO3. The silver and copper nitrates are made by dissolution in HNO3. The impure bars are the anode and the cathode is usually stainless steel. The deposit is in the form of heavy, non-adherent, 99.99% pure, dendritic crystals about 12-20 mesh in size. This form is desirable, due to the ease of filtering and rinsing out the copper/silver solution. The copper doesn't co-deposit until it reaches about 120 gm/L, or more. The presence of copper is what produces this form of hi-density crystal. When the bath is out of kilter, it sometimes trees, but not of the quality that you specify.
I think it's possible to make your crystals with a AgNO3 solution, but you'll have to experiment. I would use 200-300 mL batches, in a beaker [beakers on
eBay
or
Amazon [affil links] , and play with the quantities of the various ingredients, Ag, Cu, and HNO3. You might also try it without the copper. Start the experiments with small quantities. That way, you can simply add more for the 2nd, 3rd, etc. experiment instead of needing fresh solution. Only change one variable at a time. Write everything down. Other variables are agitation, electrode shapes, anode/cathode distance, temperature, time, and, most importantly, current density. You may be able to use the metal as the anode.
I would start with 30 gm/L silver, no copper, and 1% HNO3. No agitation at room temperature. Inert anode and a stainless cathode. Cathode current density will be critical. Try starting with about 3 milliamps per sq.cm. Go from there. Add a little copper. Add a little heat. Add a little this, a little that. Go in the direction of improvement. If you add too much of something, get new solution. If you run out of silver, refine it and start over. Keep a chart. Make the left hand column Experiment # and add a column for each variable. On the right, make a wide column for Remarks or Summary. It's most important that you only change one thing at a time.
If your starting materials are not pure, they may still work. Copper might not cause a problem. Worst case would be to have to refine one or more of them. If you tell me EXACTLY, IN DETAIL, what these materials are, I'll post details on how to refine them. It's not that tough and you can do it with lye, corn syrup, salt, bucket, stick to stir it with, coffee filters, water, and, if you do the metal, a little HNO3. You can do the whole thing in about 2 days. It would be best to start with reasonably pure materials, just in case you want to repeat it.
When you find the key, refine what silvers been used, get a bigger setup, and convert almost all your silver to crystal. Make one copy of the chart and hide both copies.
If I get a little wordy, it's because I'm writing to all readers. Also, there's a lot of wrong teaching on this board concerning precious metals.
Hope I've been of help,
Consultant - Houston,Texas
----
Ed. note: thanks for the great exposition, Chris! But if you see "a lot of wrong teaching on this board", please try your best to correct it in the places where you see it rather than devaluing every other responder's efforts by painting with such a very broad brush :-)
2003
Mr Owen,
Thanks for the tips so far. I tried a make shift electrolysis the other day using pure AgNO3 solution, graphite cathode plate of about
1 inch surface area(also tried a thin pencil lead of 0.5 mm, zirconium anode rod 1/4 inch diameter all in a 100 ml beaker [beakers on
eBay
or
Amazon [affil links] . I used
3 volts at about 1 amp.I think the volts may be too much since much less is required to reduce the Ag.Plating baths run with less don't they?
I did get trees but they were small, fluffy and did not adhere long to the cathode before falling due to their weight.Also worth mentioning is the dark crystaline material formed on the anode which I suppose would be a silver oxide.Is there any way to avoid this?
Now I did a little research and found that tartaric acid
⇦ this on
eBay
or
Amazon [affil links] will make the deposit more compact. It said to use about 1/2 teaspoon per cell, but since I don't know the size of a cell maybe you know how much per liter of this or any other additives?
The mentioning of Cu2+ in solution influencing the nature of the deposit sounds interesting. You mention the Thum cell.I heard that it runs on about 3 volts.(thought that might be too much!) My sources total about 300 grams of Ag.Some in the form of nitrate,some in powder(previously refined),about 100 grams of sulphate.Also have sterling scrap,but won't get around to that yet.I must correct myself in that I don't need to refine the silver.I've already done refining before.(chemically)(reduction of precipitated AgCl with glucose, reduction with FeSO4, copper wire are some of the methods used) My starting material in any case would be pure solid(granular) AgNO3. Any silver I have is in that form or can readily be transformed into it.(or any other silver compound, whichever is best..) What about organic silver such as silver acetate? In any case a nodular, or just a thick plate out on the cathode would also be good.( I'm thinking if the crystals I saw were electrowon from molted nitrate or halide?)
- Madrid, SPAIN
2003
In your 1st trial, I think you used way too much current. Don't worry about the voltage. All metals have a threshold voltage, below which no deposit occurs. In the case of silver, I think it is quite low and you don't need to be concerned about it. Go entirely by current density. You used about 144 amps/sq.ft. I would start with about 15 asf, or less, about 1/10 of what you used. The Thum cell uses about 50 asf.
If I remember right, tartaric acid
⇦ this on
eBay
or
Amazon [affil links] is used sometimes in the Thum cell, not to change the deposit characteristics, but to complex certain metal impurities and prevent their co-deposition.
I think you'll need some free HNO3. Start with about 1% by volume. Try adding some copper in increments. Start with about 1 oz/gal = 7.5 gm/L. Copper should harden the deposit.
It may be best to use soluble silver anodes. Sterling would be OK. It contains 7.5% copper, with the rest silver. With insoluble anodes, the solution becomes less concentrated in silver as time goes by. The deposit characteristics will, therefore, also be altered over time. The use of a soluble anode will tend to stabilize the silver concentration. You also won't have the oxide problem.
You need to understand the mechanism of how trees and nodules form. In most solutions, they start with a foreign particle on the cathode. The metal plates over the metal and causes a bump or a point. Once formed, these become high current density areas as compared to the rest of the cathode. This is caused by a greater rate of replenishment of silver at the high points than at the low points. The result is a progressively thicker deposit at the high CD areas. This higher CD also occurs on the edges, which is why you see nodules on cathode nickel. Nodules build slowly and these took several days to form. According the literature, silver is different in the nitrate matrix, in that treeing starts immediately, even in a super clean, highly filtered bath.
Using a vertical setup, it will be difficult to keep the silver from falling off the cathode. Thum solved this problem by putting the cathode at the bottom, in a horizontal position. He used a tank within a tank. The outer tank is shallow with the cathode sheet covering the bottom. The inner tank has solid sides, but it's bottom is a series of glass or plastic rods, which support the impure bars. Muslin cloth is spread between the rods and the bars, which acts to filter out insoluble impurities, like gold.
You could do something similar in a beaker. Cut the stainless in the form of a circle a little smaller than the bottom of the beaker. On two opposite sides of the circle, leave a strip of metal about
1/2" wide and 4" or 5" long. This will allow you to put the cathode flat on the bottom. Bend the strips so they run up the sides and out the top. The strips are used for electrical connections (two cathode connections will give better current distribution across the cathode). Mask the strips with fingernail polish or use the liquid plastic designed for coating the handles of pliers and other tools and is available in hardware stores. This way, all the current will be focused on the circle. Suspend the soluble anode at the top of the solution.
Once trees start forming, you'll have to watch it closely. Trees grow towards the anode and will eventually bridge and short out the electrodes. You'll then blow the rectifier fuse. If it doesn't have a fuse, I would certainly install one.
Keep plugging,
Consultant - Houston, Texas
2005
Hi
We refine impure silver anode by using Thum cell and our electrolyte is silver nitrate.
silver nitrate initial concentration is 65 g/l in Thum cell our problem is after running cell 8 hours rather to get enough silver crystal at cathode we are getting high silver containing silver nitrate solution usually 400-500 g/l silver in silver nitrate solution.
Please can you solve this problem.
- Karachi, Pakistan
I have copper electrical components that are silver plated. Instead of losing the silver when the copper is sold as scrap, I'd rather like to recover the silver in a form that makes it useful or worth reselling as a separate entity. Is there any process you can recommend for stripping the silver coating from the copper?
Pieter BlignautEngineering - Pretoria, Gauteng, South Africa
2006
2006
I have approximately 2000 kgs of silver plated copper from some old transformers. Is there enough silver to make it worth removing?
If so, how do I remove it?
Thanks,
Ken
hobbyist - Sydney, Australia
August 15, 2010
please help me...
I really like the idea of recovering silver from a solution for our research. the problem is that I don't know how. I an just a secondary student and I don't know a lot of things. please help me. also, is it possible that a bacteria or any microorganism can recover silver from a fixing bath. I need to have two ways of recovering silver. First is the only commonly used and the other one is the proposed. thanks.
Student - Davao City, Philippines
I have copper coated with silver and wanted to separate them for selling the silver, is there a realistic way for me to do this? Thanks in advance
Lance Davenport- Pottsville, Pennsylvania
April 29, 2011
Q. Hi,
I am working in an Electroplating industry. We are doing silver plating. We have some rejected parts to strip. So we'd like to strip and recover the silver from the stripped (stripper) solution. So, please tell me a good solution to my question. Thanking you.
Electroplating - Singapore
November 22, 2011
Q. What are silver precipitation crystals?
Edward J Stroble- St Clair shores
March 2, 2012
Hi Edward. Give us the context please. What is your situation? Sorry, but I have no idea what you're talking about :-)
Regards,
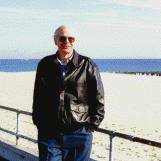
Ted Mooney, P.E.
Striving to live Aloha
finishing.com - Pine Beach, New Jersey
March 5, 2012
Q, A, or Comment on THIS thread -or- Start a NEW Thread