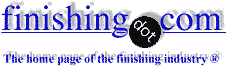
-----
Cylinder mfgr. investigates a treatment for piston rods
2003
We are a manufacturer of hydraulic cylinders. We have received an inquiry for a hollow piston rod 220 x 180 mm and 240 x 200 mm (We also have the option to use solid rods 240 mm or 220 mm.The problem is the treatment on these rods.
The customer receives the rods with a mixture of Nickel/Chrome and some other substance They are bonded to the rods with some metallurgy process and then are turned down to the size needed.They say they can achieve a surface finish of under Rz 1Um.The layer can vary from 0.3 to 1.2 mm thick. They have salt spray test results of around 1000 hrs. Is there anybody out there familiar with this or a similar process.
Best Regards,
Eng Sales Manager - Bagenalstown,Carlow, Co Carlow, IRELAND
Sorry, I'm having a hard time following you. Are you saying that some competitor of yours has previously supplied your customer with these rods and you are trying to get a better understanding of what your competitor was providing? Based on the good corrosion resistance that is reported, and the "mixture" of nickel-chrome, it sounds to me like the rods are electroless nickel plated before chromium plating, and then ground to a final finish.
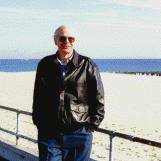
Ted Mooney, P.E.
Striving to live Aloha
finishing.com - Pine Beach, New Jersey
2003
The 0.3 to 1.2 mm thick can be done but is certainly way too high for most practical plating processes (specially EN). Based on the thickness, corrosion resistance and surface finish attained according to what you report, it could also be a spray and fuse S/F application. Plasma spray or HVOF are also capable of thick coatings but the layer can be somewhat porous and difficult to polish to such a fine RMS. The S/F process can be described as a "metallurgical process" as it involves high temp, is capable of producing totally dense hard nickel-chrome alloy deposits and perfectly allows for single point machining. On the other hand it can lead to distortion even if done carefully.
Guillermo MarrufoMonterrey, NL, Mexico
2003
Q, A, or Comment on THIS thread -or- Start a NEW Thread