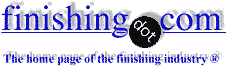
-----
Lack of nickel plating in tapped holes
We are having a copper part plated with FED-QQN-290 (replaced by AMSQQN290)
class 1,.0002" thick, one recessed pocket must be .0001" thick. The part is .34 x .45 x .87 (IN.) and has two 4-40 tapped holes thru. My plater racks one of these holes and we get very little or no plating in that hole. We are trying to stay away from barrel plating due to the nicks, etc.
The drawing has no notes about the tapped holes. QQ-N-290 states the plating shall be as specified for all visible surfaces which can be touched by a .75 dia ball all other surfaces shall be less than the minimum specified. I look forward to your info.
VP - Fulton, New York
2003
QUICKSTART:
The plating thickness is directly proportional to the current per Faraday's Law. But the current takes the path of least resistance such that little to no current will flow deep into holes, with the result that you'll usually get some plating of the hole right at the surface of the part, but perhaps no plating at all deeper into the hole.
Because the plating on inside corners of a part will be scant, and it can be difficult to measure the thickness there, it is fairly common to specify a minimum thickness of plating for any area that can be touched by a 3/4" diameter ball, together with plating coverage of all visible surfaces.
Most companies do not want plating in a 4-40 hole. If there is plating there, a conventional machine screw will not thread into it as the opening will be too small. Any way, what was your question. You gave facts, no question.
James Watts- Navarre, Florida
2003
Hi. I certainly agree with James, but the idea of one hole having however much plating occurs with a rack hook in it and the other having however much plating it gets without a rack hook sounds a bit random and problematic for later insertion of the screws. Maybe you can eliminate the randomness while improving the reliability over gravity racking by considering racking this part on two spring-loaded pins going through both tapped holes?
Regards,
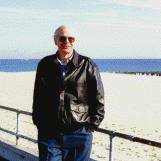
Ted Mooney, P.E.
Striving to live Aloha
finishing.com - Pine Beach, New Jersey
January 2014
Q, A, or Comment on THIS thread -or- Start a NEW Thread