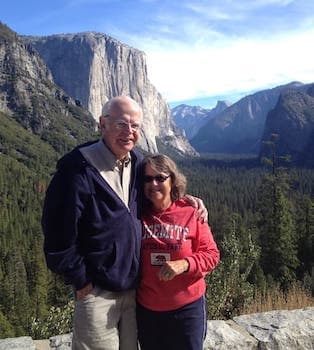
Curated with aloha by
Ted Mooney, P.E. RET
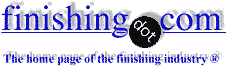
The authoritative public forum
for Metal Finishing 1989-2025
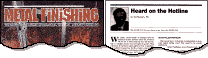
-----
Bonding resistance -- Olive green cadmium to chromated aluminum
Q. Dear sir
Please give your valuable suggestion regarding my question.
Is cadmium 6 micron over nickel plating 12 micron with olive drab passivation conductive?
If yes, we did same process but result was non conductive.
Please help me.
Thank you
Asst engineer - Hyderabad, India
September 22, 2021
A. Hi Bandari. Chromate conversion coatings on cadmium are not highly conductive metallic coatings, so don't expect a surface with a chromate coating to show similar conductivity to bare metal.
But on the other hand, conductivity is not a yes/no proposition, it is quantitative. While cadmium with chromate is certainly not an appropriate surface for an electrical contact, it can be right for a connector housing.
While you are awaiting additional replies, we have appended your question to a discussion about cadmium plating plus olive drab chromate on connector housings. Good luck.
Luck & Regards,
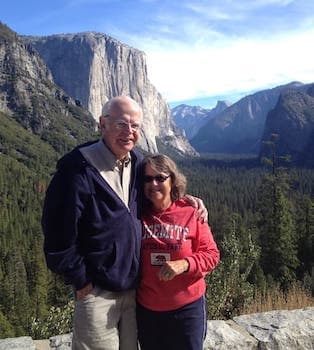
Ted Mooney, P.E. RET
Striving to live Aloha
finishing.com - Pine Beach, New Jersey
September 2021
⇩ Related postings, oldest first ⇩
Q. I have noticed that the bonding resistance can change significantly over a period of time between two good galvanic matching materials: Base material: AA6082 Aluminum conversion coating according to MIL-C-5541E Class 1A, Yellow chromating Alodine 1200 Connector material: MIL-C-38999 series 3, shell aluminum alloy, olive green cadmium plating.
The bonding resistance after initial assembly is lower or equal to 2,5 mOhms. But after some tests (for example vibration test or temperature cycling test) the bonding resistance increases (sometimes by a factor of 10). From my point of view this is due to galvanic corrosion. Is there something I can do to keep the bonding resistance constant over time?
Mechanical Design Engineer - Wevelgem, West-Vlaanderen, Belgium
2003
Q. Hello,
I have noticed the same problem on my equipment:
Connector D38999 / 2024 aluminium alloy with Alodine 1200 coating.
Did you find a solution in your case?
Regards,
Thibaut
- Toulouse, France
September 10, 2010
A. I would advise to use tin coating instead of chromate conversion coating so that better electrical conductivity can be obtained. If bonding resistance still increases after environmental tests, connectors should be re torqued.
Murat YABAN- Ankara Turkey
November 23, 2010
August 16, 2011
A. I have experienced the same issue and am currently running tests in hope of solving this issue. Here is what I have so far:
Use MIL-DTL-5541
[⇦ this spec on DLA] F Class C. This will help with corrosion on electronic applications.
Clean all metal to metal surfaces with something stronger than alcohol.
I have also installed an EMI gasket to account for any flatness issues of the connector or aluminum surface. This has proven to have a huge impact.
Next try Belleville style washers. This will help maintain positive pressure between the connector and aluminum surfaces.
And finally, determine the optimal torque. This may turn out to be more art than science.
Good luck.
- Calverton, New York
Q. Hello,
I know this thread is a bit older, but we experienced the same problem with MIL-C-38999 olive green cadmium connectors (box mount) and Alodine Class 1A chromate.
Does anyone have an idea or a possible solution how to solve this problem?
Thanks for your help.
- Pforzheim, Germany
March 31, 2015
Q. I am facing this problem too, using a cadmium coated 38999 series connector with Trivalent chromated aluminium plate. I have tried various combinations, but still Bonding resistance keeps on increasing. Using Emi/EMC gasket in between didn't help either. Has anyone some solution to this evil issue?
HEMANT RAIMechanical Design - Gautam Budh Nagar
January 2, 2017
Q. Hello everyone!
I also have several problems with electronic equipments regarding bonding. It's very hard to achieve 2.5 milliohms from the connector backshell (D38999) to the unit chassis. This is the req MIL-5087. All parts are free of painting, cleaned, torques are controlled but nothing I do more I achieve 2.5 mohm.
Units that pass through ESS also get higher resistance!
Besides, units receive from customer come with high impedance (25-30 milliohms). Is that normal? Does the requirement change? I read in a paper the bonding resistance can raise up from 8-12 milliohms as time goes by (up to 5 years).
Please advise what shall be done.
- POA, RS Brazil
April 17, 2017
Q, A, or Comment on THIS thread -or- Start a NEW Thread