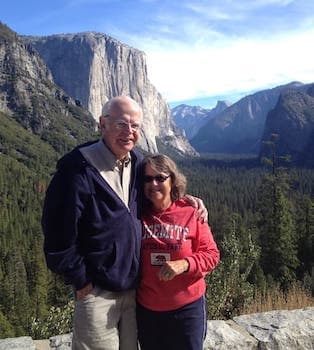
Curated with aloha by
Ted Mooney, P.E. RET
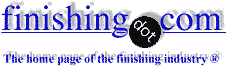
The authoritative public forum
for Metal Finishing 1989-2025
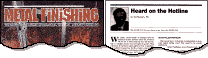
-----
Non conductive smut develops between EN and copper contacts during burn-in
2003
The scenario:
Our company manufactures military radios. The electronics are housed in a cast box with a cover. On the cover we put berylium-copper contact strips that 'seal' to the box so that the electronics are protected from unwanted electronic signals getting inside; so it's very important that they make good electrical contact. The cast aluminum (grade LM25) is electroless nickel plated to MIL-C-5541. The plating is about 12 microns thick. When we get the parts back from the platers we assemble the electronics in and then they go though a
'burning-in' process - i.e. they go through -50° C to +90° C cycles. Lots of moisture gets into the radio during this test because of condensation. When we inspect the cast parts after and there is some 'smutty' deposits on the surfaces of the cast part where the contacts are. The problem is that this deposit is non-conductive. What causes this and how can it be avoided? Any info would be of great help to solving this mystery!
If there are any products you have please let me know also.
Thanks in advance.
electronic communication systems for defense - Durban, Kzn, South Africa
It seems like 12 microns is not enough EN thickness. Castings normally need more thickness due to their intrinsic porous nature. Also an improper prep cycle can contribute to aggravate the problem. Keep in mind that corrosion protection afforded by EN depends on absolute imperviousness, especially if substrate is aluminum in contact with copper.
Guillermo MarrufoMonterrey, NL, Mexico
2003
2003
Your smut may be aluminum corrosion product resulting from galvanic corrosion between aluminum and electroless nickel or copper. Aluminum castings are often quite porous. This porosity replicates as pores through the coating, allowing contact between the active aluminum and the more passive EN or copper. The potential difference can be as high as 700 ma in deaerated water, which can drive corrosion of the aluminum to high levels.
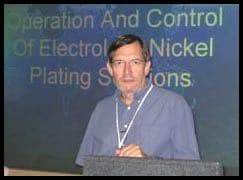
Ron Duncan [deceased]
- LaVergne, Tennessee
It is our sad duty to note Ron's passing on Dec. 15, 2006. A brief obituary opens Episode 13 of our Podcast.
Guillermo and Ron,
Thanks for your valued inputs. I had my suspicions. I was not sure if was, perhaps a leaking out of the Loctite on the fasteners but this sounds more plausible. I agree on the thickness and will rather opt for Grade A thickness instead.
- Durban, South Africa
2003
Q, A, or Comment on THIS thread -or- Start a NEW Thread