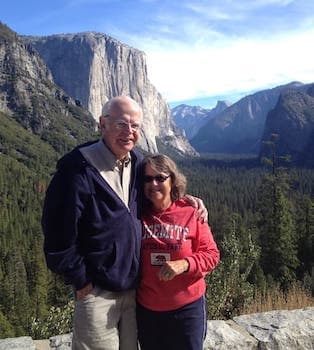
Curated with aloha by
Ted Mooney, P.E. RET
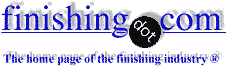
The authoritative public forum
for Metal Finishing 1989-2025
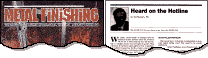
-----
How to keep the copper we are cutting from adhering to the thread cutter? TiN?
2003
Hi,
We use a screw to form a copper bushing we use to adjust mirrors in our laser cavities. The prob is, after we've formed the bushing, the copper from the bushing is deposited on the screw we use to form it. After a while the screw barely turns into the bushings. I've heard ammonia
⇦ this on
eBay or
Amazon [affil links] is a way to clean the copper out, but we'd like a better solution to the prob. I was thinking of trying a plating like TiN. The screw we use is SST and has 1/4-80UNS-2A threads.(very fine, so the copper is a problem). If you think TiN is a good way to avoid this, how do you call this out on a drawing. I don't have any experience with this type of plating....all I know is its not electro plated..
Thanx in advance,
mechanical engineer - Redwood City, California, USA
I may be missing something here, but why are you not using a tap and cutting fluid rather than a screw? If you look around trade catalogues, you should be able to find a ground tap that has been coated with TiN. Cutting fluid is your answer. Buy several taps and then use the ammonia to remove the copper by soaking overnight or as required.
James Watts- Navarre, Florida
2003
2003
Well, that would and does work but after forming 3 bushings, the threads are unusable to further form bushings so it would need to be soaked. We do about 100-150 at a time, so that would require a very large number of taps. This is why we want to plate the screws we use with TiN. I also did a search and couldn't find a ground tap for
1/4-80 UNS plated with TiN. If anyone has a suggestion on a material or plating we could use so the copper wouldn't adhere, its much appreciated. Thanx for the speedy response Jim.
Regards,
lasers - California
I don't really know, I can only guess and suggest a trial, but I think either electroless nickel or chrome plating would be fine. They are often used in molds for their good release properties. Chrome also has a very low coefficient of friction and is inexpensive compared to TiN.
While titanium nitride is very hard, and is proven better than chrome or electroless nickel for some applications, I think it is used on some consumer metal-cutting items like drills as much for the saleability of its gold color as for any demonstrable advantage over chrome :-)
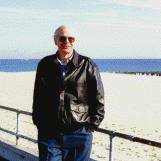
Ted Mooney, P.E.
Striving to live Aloha
finishing.com - Pine Beach, New Jersey
2003
A couple more questions. What are you using for cutting fluid? Are you hand tapping or using a tapping "machine" or doing it on a drill press OR ? As you tap, are you periodically backing up to break the chip or are you just "plowing " thru? Can you switch to a harder copper heat treat or a hardened alloy? Have you tried using the next larger drill, as in a wire size or a decimal drill that is very minorly larger?
James Watts- Navarre, Florida
2003
Q, A, or Comment on THIS thread -or- Start a NEW Thread