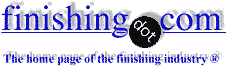
-----
The zinc plated products we bought are rusting
Sir,
We have procured some zinc-plated mild steel products, which have subsequently begun to rust severely in many places. Particularly, around the welded joints and internal pockets. Is there an aspect of the process which is meant to prevent this occurring?
Production engineer - Stone, Staffordshire, United Kingdom
2003
If you send some photos we'll be happy to post them, Michael, so we have a better understanding of what you are referring to. The plating will be thinner (and maybe non-existent) in recessed areas, so it may simply be that the plating is too thin and rust occurs in the low current density areas.
Parts need to be plated to some specification or other, and that is the starting point. Is there a spec number, a minimum thickness, or average thickness, a salt spray requirement, or any information regarding what the plating shop was supposed to do?
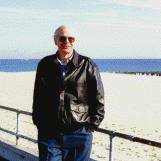
Ted Mooney, P.E.
Striving to live Aloha
finishing.com - Pine Beach, New Jersey
2003
The length of time a zinc deposit endures without red corrosion failure depends on many factors. Thickness of the zinc plated deposit is one, and the type of chromate passivate is another. Some platers clients specify a,"commercial zinc deposit." This means that the part simply has to be covered with zinc. Most specify a desired thickness, (0.0003 inch for example). Then, there is an issue of which chromate passivate to use. Other factors can enter into the equation, like getting a sulfonated oil onto the part and then putting it into a corrosive atmosphere. Service life in that environment will be shortened. We use salt fog tests (ASTM ASTM B117 ) and CCCT testing to indicate the predicted service life of plated parts. Perhaps if you had several sample parts tested at an independent lab, you may gain insights as to why you are getting an early failure. Finally, it is possible that the weld bead on the parts may be setting up a galvanic cell that is causing red corrosion prematurely.
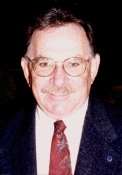

Ed Budman [dec]
- Pennsylvania
With deep sadness we advise that our good friend Ed passed away Nov. 24, 2018
2003
As usual, your answer is both helpful and insightful, Ed. However, permit me to disagree with your definition of "commercial zinc deposit". I have heard some platers and users say it means what you have said, but others say that it means what you said except no guarantee of coverage in holes, or that it means ".0002" average thickness, or that it means ".00015" average thickness. From which I say it's meaningless, imparts a false sense of confidence on both sides, and is a path to a contract dispute :-)
If any platers or users out there agree or disagree with either of us, I'd like to hear more input on what you feel "commercial zinc plating" means.
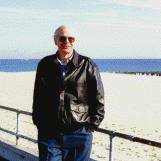
Ted Mooney, P.E.
Striving to live Aloha
finishing.com - Pine Beach, New Jersey
2003
2003
Well Ted,
I've always thought that's an interesting question, what we do rightly or wrongly is when a customer asks for commercial zinc plate or more typically just specs something like BZP (on the scrap of paper that passes for an order) is to plate to the lowest service class of the appropriate national standard in our case the British Standard, and quote that spec on the outgoing paperwork. Whether this is appropriate anymore with the revised ISO9001:2000 requirements where you are supposed to identify customer needs is food for thought. As an aside, many years ago I worked for a company that used to bright nickel plate and apply colourglo, which is a translucent coloured lacquer, sprayed and stoved. One customer supplied items for a stair handrail with typically no drain holes. The customer stated that under no circumstances could holes be drilled and he would accept liability for any problems that might occur (this was in writing from the manufacturer and the architect). So the inevitable happened entrapped solution leaked after installation and ruined about £20K's worth of soft furnishing. After a lot of argument about liability, all parties ended up in court. We waved our letter about the customer accepting liability. No go said the judge, as the finishing company I worked for was in business as a finishing company it (or the people involved) were deemed to be experts and shouldn't have done the work as they were aware of the possible/probable consequences, consequently the judgment was found against us and we had to pay everybody concerned. An expensive lesson. I always think of that whenever I see an order stating XXX plate with no specification.
Regards,
- Lowestoft, U.K.
2003
Thanks for the feedback, I attach a picture of one of the worse panels for reference.
Production engineer - Stone, Staffordshire, United Kingdom
I appreciate the photo, Michael, but I'm not sure about what I'm looking at. Below the rust am I seeing weld metal? Are these parts welded before or after plating? It looks to me like I see a horizontal line of water damage ... or is this heat damage?
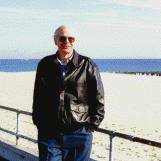
Ted Mooney, P.E.
Striving to live Aloha
finishing.com - Pine Beach, New Jersey
2003
The picture shows a simple fold (with no welds) which is showing the rust.
Michael EastonProduction engineer - Stone, Staffordshire, United Kingdom
2003
In that case, it's a very easy guess. The parts have to be absolutely dry before they leave the plating line, and it's reasonably likely that the visible areas were basically dry while water remained in the seam.
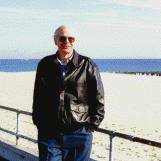
Ted Mooney, P.E.
Striving to live Aloha
finishing.com - Pine Beach, New Jersey
2003
Q, A, or Comment on THIS thread -or- Start a NEW Thread