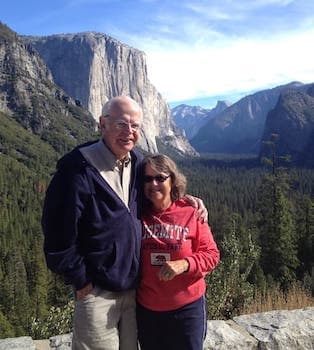
Curated with aloha by
Ted Mooney, P.E. RET
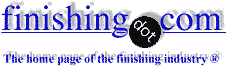
The authoritative public forum
for Metal Finishing 1989-2025
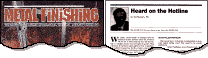
-----
Lead free plating on copper, parts soldered in lead free process
2003
Dear Experts,
I have been working on a problem for a long time. (but I am not a finishing expert.) We produce electronic circuits for high power industrial applications. The leadouts (pins) of those circuits are made of copper wire (Cu-OF, US number is C10100). We solder these pins onto a copper surface in around 260 C, mainly with lead free soldering. The diameter of the round copper wire is 1 mm. Those pins are plated with SnPb (5-10 micron) (electroplating, galvanic). The aim of this plating is to prevent the copper from oxidation, and provide a very good soldering property. So, we need to change that plating material to a lead-free one. I have tried several types, but none of them worked well. Sn plating with a 1 µm thin Ni underlayer: the adhesion of the Ni plating to the copper itself was not acceptable. During various aging tests, the Ni layer peeled off from the pin. SnCu plating: during the soldering the plating has melted, and the particles of the solder paste run up to the surface, done that very dull -- not acceptable. Sn plating: during the soldering the plating has melted and formed some bumps, bubbles on the surface, even the plating was bright or matt, or different thickness. It is also not acceptable. Electroless plating is also not acceptable, because it discoloured very easy.Ag plating: 3-5 micron. First it seemed good, but in the end of the aging environmental tests it shows not so good results (TC, HTRB, HHHTRB). The plating is oxidised in a high degree. Impossible to solder again. It means that, the storage time is not so long in this case. Ni plating: not solderable enough. Wetting properties are low.
Pictures illustrate the bumping effect, which occurs during soldering at Sn and SnCu platings (and very rarely at SnPb finishing) What kind of other finishes, alloys could be use? What other possibilities exist?
The requirements for platings:
Lead free;
Very good solderability;
No oxidation;
No discolouring;
No deformation of plating during soldering process;
No electrochemical migration effect (we can test it)
Therefore: long time shelf life;
Electroplating;
Not so expensive (we can forget gold);
Thank you in advance!
Norbert Kánvásicircuits for power electronic applications - Bicske, Hungary
2003
I believe that at least one of you problems is improper preparation prior to plating. All the symptoms point to that. I am guessing that the copper pins may be beryllium copper ( usually for stiffness and strength). Be copper requires special surface treatment before plating. Example, after cleaning in alkaline cleaners, a hot sulfuric acid dip is one way to prepare. Usually 18%by volume sulfuric acid at 65-67 degrees C for about 1 minute. Other copper alloys usually respond to this preparation also. If it is pure copper, 10% sulfuric acid is usually used, at room temperature for 30 - 45 sec. Rinse quickly and electroplate. The easiest lead free plating is tin. Use a solution without brighteners, i.e. one designed for electronics. Most suppliers have these for sale. Actually any proprietary lead free alloy should work well if the preparation is correct.
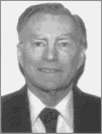
Don Baudrand
Consultant - Poulsbo, Washington
(Don is co-author of "Plating on Plastics" [on Amazon or AbeBooks affil links]
and "Plating ABS Plastics" [on Amazon or eBay or AbeBooks affil links])
Looks like Tri-alloy plating will work for you.
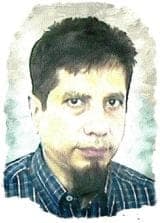
Khozem Vahaanwala
Saify Ind

Bengaluru, Karnataka, India
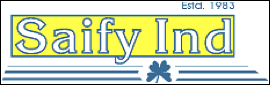
2003
April 16, 2012
Q. Sir
We are in manufacturing of magnetic components and major problem faced is oxidation of pins.
The pin used are copper and phosphorus bronze.
The plating is electroplated tin.
The shelf life is very low of the order 20 days and then becomes black.
This leads to poor soldering and result is dry solder at customers end.
Please help me in solving this problem.
- SAHIBABAD, UP, INDIA
Q, A, or Comment on THIS thread -or- Start a NEW Thread