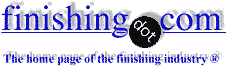
-----
Mil-spec anodization sometimes porous sometimes not
2003
If someone specifies MIL-A-8625 / MIL-PRF-8625 [⇦ this spec on DLA] anodizing, type I and Class 2, is that enough to control the porosity of the anodized coating? I am having issues with different porosities of supposedly the "same anodization" process.
Thank you,
Ivan AraktingiOptics - Murrieta , California, USA
You have two items to consider. Coating thickness and pore size. Pore size is mostly controlled by tank temperature/part temperature. The warmer the solution, the larger the pore size. Coating thickness is frequently expressed as coating weight which is actually a combination of porosity and thickness. The mil spec absolute minimum is just that, a minimum and not an optimum. The warmer tank also promotes a faster attack on the oxide coating which will give a thinner coating for a given time and voltage. If you specify a not to exceed 70 °F temperature and a coating weight closer to the top of the range, I think that most of your problems will go away. Require certifications.
James Watts- Navarre, Florida
2003
Q, A, or Comment on THIS thread -or- Start a NEW Thread