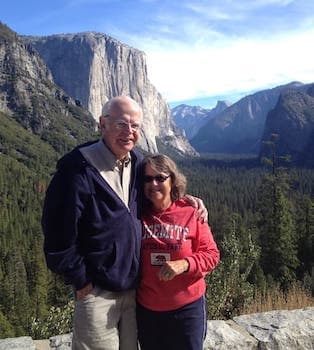
Curated with aloha by
Ted Mooney, P.E. RET
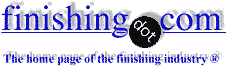
The authoritative public forum
for Metal Finishing 1989-2025
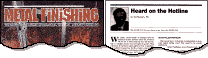
-----
Chromating of Zinc-Nickel Plating Q&A, Problems & Solutions

Q. We do alkaline zinc nickel barrel with blue passivation finish. Minimum thickness 5 µm with a Ni percentage of 12-15%. We control Zn and NaOH at 8-12 g/L, 115-140 g/L respectively.
Before passivating, we dip in HCl with a pH of 1.9-2.0.
After finishing plating, we checked the thickness and percentage of Ni, the results were still within the range. However, when passivating the color is uneven. The color range is in accordance with quality control, but not even. Passivation was carried out for 2-2.5 minutes with pH 3.8. What causes uneven color? How to handle it?
Thank you.
Chemist Lab - Batam, Indonesia
November 21, 2023
A. Hi Astri. I am not personally familiar with the use of HCl between zn-ni plating and chromating. I was under the impression that DI rinsing was preferred, but my understanding may be dated -- did this recommendation come from the supplier of the chromating process?
It may depend upon your chosen supplier, but Atotech seems to recommend shorter chromate immersion times at a pH of 2.1-2.5, saying that above 3.5 the reaction is too slow and inefficient. inability to get dark black,
Luck & Regards,
Ted Mooney, P.E. RET
Striving to live Aloha
finishing.com - Pine Beach, New Jersey
Quickstart: Zinc-nickel alloy plating, combined with hexavalent-free chromating, is a relatively new and relatively high technology finishing process causing problems for many shops, including inconsistent blue chromate color, inconsistent yellow color, inability to get black, and contamination issues.
⇩ Read on for some solutions, oldest first ⇩
Q. Presently we are operating a Barrel Zinc plating plant. I would like to know about the Zinc-Nickel plating to enhance the corrosion resistance. My questions are: 1.What is zinc-nickel plating? 2. What modifications are required to incorporate zinc-nickel plating? 3. What are the different color finishes possible with zinc-nickel plating? It would be of great help.
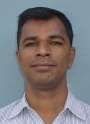
V. G. Rajendran
- Trichy, Tamilnadu, India
2003
A. Hi VG. Zinc-nickel plating is the plating of an alloy of nickel and zinc. One supplier (or more) of the alkaline variety claims that about 6% nickel is the magic number to get the electrochemical potential, and the benefit of more corrosion resistant corrosion products where it needs to be for best corrosion resistance.
To my knowledge, zinc-nickel is only available as a proprietary process, so you need to pick a supplier and work with them. But it is available either as an acid process (where a different percentage of nickel may be ideal) or as an alkaline process, and the choice may depend on whether you currently do acid or alkaline zinc.
This is a cathodic, protective plating, not a decorative process, and the most conversion coating color (yellow) is not pure yellow but an iridescent color which some people call more prone to "reddish" or "purplish" streaks compared to a conventional yellow chromate on zinc. I believe black chromating is also an option, and clear as well. Good luck.
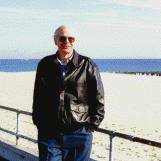
Ted Mooney, P.E.
Striving to live Aloha
finishing.com - Pine Beach, New Jersey
Can't get jet black passivation on Zinc-nickel plated parts
Q. My customer spec. is to have jet black passivation, whereas our process produces brownish tint with black colour after passivation. What is the possible remedy to get jet black colour?
Parthasarathy [returning]Manager - Chennai, Tamil Nadu, India
2007
A. Does it have to be zinc-nickel plating, Parthasarathy? I think you'll find that reliable blacks are easiest to obtain if the plating is zinc-iron because of the iron content. Good luck.
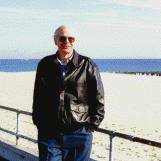
Ted Mooney, P.E.
Striving to live Aloha
finishing.com - Pine Beach, New Jersey
A. Hi!
In your letter there is no clear picture about plating. The substrate should be Zinc (acid) plated, followed by nickel plating. Then the thickness should be more than 20 micron. If the substrate is plated like that you can achieve the desired colour.
GOOD LUCK
- Bangalore, Karnataka, India.
A. Please verify with your chemical supplier; the latest developments in trivalent chromates will help you to achieve with 80 to 90% Jet black finish (acceptable level)
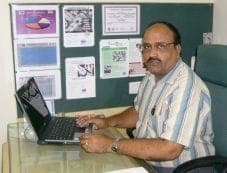
P. Gurumoorthi
electroplating process chemicals - Chennai, Tamilnadu, India
A. Parthasarathy,
Please give more details about your customer spec. and also full details of what is your plating process. There are lots of developments happening in Zinc and zinc alloy plating.
Alkaline cyanide-free Zinc-iron plating, followed by trivalent passivation is the answer. If you come out with more details, you will get good suggestions.
P.S. It is nice to see Gurumoorthi back!
Regards
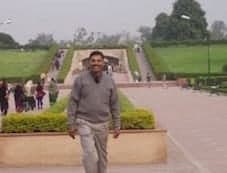
T.K. Mohan
plating process supplier - Mumbai, India
A. Dear Mr Parthasarathy,
Try doing an XRF analysis of the Nickel - Zinc percentages on the parts that don't look so good with black. You may find that they have a higher percentage of Nickel in them.
And you may have to increase 2-3% of Zinc in the plated alloy to get a pleasing black.
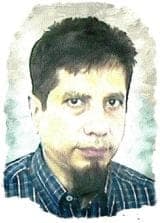
Khozem Vahaanwala
Saify Ind

Bengaluru, Karnataka, India
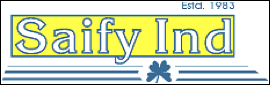
Multiple threads merged: please forgive chronology errors and repetition 🙂
Color Variation on Zinc Nickel Plating
Q. I have a plating supplier that sent me some parts with a good corrosion protection but the parts we have been getting have been gray finished. Now we received a new batch of material "blue" -- the supplier is stating it is a normal process variation and should not affect the functionality of the parts. What do you all think?
Ruben Duran- Juarez, Mexico
2006
A. Buenas Diaz,
He should let you know what's the difference between the "grey" ones and the "blue" ones.
Saludos cordiales,
- Mexico City, Mexico
A. Ruben Duran
This may be due to latest trivalent chromate over zinc nickel plating available in the market. However normally zinc nickel alloy with trivalent blue produces blue nuances are accepted. This will not alter functional application of zinc nickel plating. We are facing similar problem in India. The coated piece shall exhibit base metal colour (grey) or blue nuance (both are accepted colour).
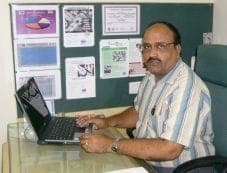
P. Gurumoorthi
electroplating process chemicals - Chennai, Tamilnadu, India
Q. Facing problem in zinc nickel --
After doing zinc nickel plating the component becomes black after dipping in trivalent passivation.
- Ludhiana, Punjab, India
March 10, 2012
A. Vikram,
Alkaline Zinc-Nickel plating process may be considered as a typical Alkaline zinc plating process with added "impurities" of Nickel in ppms say from 600 ppm to 12-1500 ppm.So you can expect a color change in passivation and it will have a blackish tint but without patches. Also remember there are special chromates for Zinc-Nickel process. Ed Budman rightly said that excess Nickel plays havoc with passivation color. The buyer has also to be educated and shown the color before finalizing the acceptance level of the color. Even the so-called giants in Automobile Industries still go for aesthetics in Trivalent blacks and Zinc Nickel passivation colors. Plating Voltage plays a big role in this system. It is advised to give lesser volts say 3-3.5 to get an even mix of Zinc & Nickel with acceptable percentage. Remember if you increase the voltage you will get a good shining plate color which will not give the property of Zinc- Nickel plating and you will have more Nickel on the HCD (flaking deposit) and less on the LCD.....
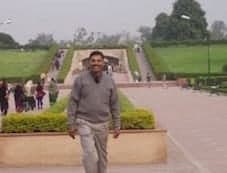
T.K. Mohan
plating process supplier - Mumbai, India
Nitric acid dip turns the Zinc-Nickel plating black
Q. Sir,
I have just started alkaline zinc-nickel plating bath. My problem is Plating gets dull/black in nitric acid.
At present the bath is having 12 gms/lts zinc and 1.8 gms/lts nickel. But I haven't use it for 2-3 months after the bath make up; does it affect the quality?
Plating shop - Gujarat, India
May 19, 2013
A. Hello Mr. Tarang,
I hope you solved your problem already, but if you didn't, you should add some (0.5 cc/liter) purifier (your vendor should have alkaline bath purifier for this use) and use the bath for a couple of hours to electrolyse (at low voltage and current, 2-3 Volts) the brighteners and levelers. Then you should run a Hull test and titrations to add sodium hydroxide, zinc and nickel if it needs to...
Just when you have done all of this, start with your production with actual parts. I do not recommend to use left aside baths without electrolysis, because you could get some impurities into the surface of your part. The black spots could be free nickel, so you may need to add some nickel leveler. All this may appear in the Hull test!
Hope this is not too messy and helps you! Regards,
- Cañuelas, Buenos Aires, Argentina
Q. Sir,
Thanks. I did the same and already started the plating, but my chemical supplier has suggested to me to avoid nitric dip before passivation. Is it advisable?
Plating shop - Gujarat, India
Q. 1- What is the best bath composition and operating condition for electroplating of bright Zn-Ni? (for a thesis project)
2- What is the solution for dark appearance of electrodeposited Zn-Ni alloy?
I have some options as below :
- Iran
March 19, 2014
by Abner Brenner
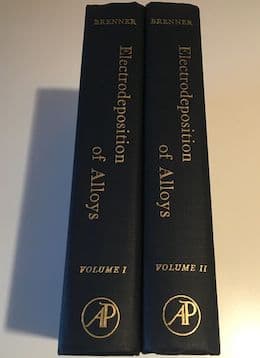
on AbeBooks
or eBay or
Amazon
(affil links)
A. Hi Mostafa. You haven't told us what you are up to and trying to do, which makes it a bit tricky to reply. As you can probably tell from this and other threads, the usual approach in the Americas, Europe, and India is to buy packaged solutions from companies who have done the development work and who hold their formulations proprietary.
An early question must be what alloy composition do you seek? Most typically, zinc-nickel plating has a few percent of nickel, say about 6%, chosen for best corrosion resistance ... but is that what you're looking for?
Brenner lists about two dozen formulations but does not claim that they all work; and they deposit varying ratios of zinc to nickel; few supposedly deposit over 90% zinc. Some contain cyanide, which you probably don't want.His "Bath 6" from Schoch and Hirsch supposedly deposits 96% zinc, and consists of 47 g/l NiSO4.7H20, 20 g/l ZnSO4.7H20, and 22 g/l Al2(SO4)3.
His "Bath 15A" from Sathyanarayana and Rama Char supposedly deposits 93% zinc, and consists of 29.3 g/l Ni and 32.7 g/l Zi as sulfamates, with 16 g/l Na acetate.
Regards,
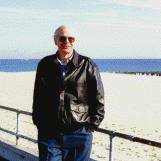
Ted Mooney, P.E.
Striving to live Aloha
finishing.com - Pine Beach, New Jersey
Q. Dear ted mooney,
thanks for your kind reply.
This is my master of science thesis. I want to achieve a coating with below conditions on low carbon steel substrate
1. the nickel wt% is between 8 to 14, and the rest is zinc
2. the deposition technique is pulse plating
3. the temperature is 50 °C
4. pH is 3
5. current density 1 to 100 mA/cm2
6. duty cycle is 5% to 80%
7. we use chloride bath with HCl (for correcting the pH), KCl and H3BO3 acids and ZnCl2 and NiCl2.6H2O
Your help would be appreciated
Thanks & Kindest regards,
- Ahvaz, Khuzestan, Iran
March 27, 2014
A. Hi again. I am not a chemist, let alone a zinc-nickel chemist and can't help too much except to say:
- You might try to locate a copy of Brenner's "Electrodeposition of Alloys" in a library (or try to buy one ⇦[this on
Amazon,
eBay, &
AbeBooks affil links]
) because it is both the principal authority and the bibliography on the subject. Pages 196-199 briefly list almost 2 dozen formulations for Zinc-Nickel baths, along with their operating conditions; and pages 236-238 list the references where the formulations were found. Safranek's "The Properties of Electrodeposited Metals and Alloys" ⇦ this on
eBay,
Amazon,
AbeBooks [affil links]
should also be among your references.
- You might also try to get access to SurfaceQuery.com, which is a searchable database of patents, journal articles and technical conference proceedings from the metal finishing industry, and includes some references to zinc-nickel plating.
- I would suggest shooting for your midrange current density of 10 ma/cm2, with no pulse plating, and try to get a sound and not black deposit as a starting point before worrying about the percentage of nickel or trying to tame the additional variable of pulse plating. Until you accomplish sound plating of some sort, all the rest should wait. Best of luck.
Regards,
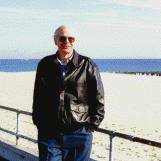
Ted Mooney, P.E.
Striving to live Aloha
finishing.com - Pine Beach, New Jersey
A. Anselm Kuhn does a great job with his information resources. I would also recommend two free ways to access information relevant to your query - uspto.gov (the U.S. Patent Office) and google.com/patents. The vast majority of available relevant information on zinc-nickel plating is in U.S. Patents. These sites are not difficult to use; they're not easy, either. Both of these sites offer a number of search tools and a researcher would be well-advised to familiarize himself or herself with most of them. Keep in mind a few things - first of all, you cannot 'make, use, or sell' any processes which the patent claims if the patent is still in force (usually 17 years); and secondly, the patentee is required to provide within the text of the patent the 'best mode' of practicing the invention. He or she doesn't have to identify it as such - there is no 'lookie, lookie here is my best mode,' and it is sort of a game to hide it as best can be done.
Having said all of this, if there is no equivalent patent in any country, people in that country are free to practice the teachings of the patent.
Patents can be great, fun reading (in my opinion).
My answer is relevant to many, many other queries.
This is not legal advice; I am not a lawyer. This is just my opinion.
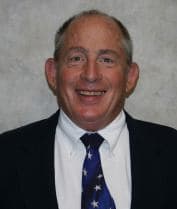
Tom Rochester
CTO - Jackson, Michigan, USA
Plating Systems & Technologies, Inc.

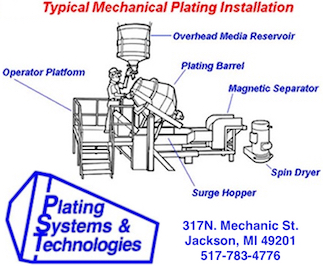
![]() |
opinion! Yes, patents are fun, but can infuriate us as well :-) ![]() Ted Mooney, P.E. RET Striving to live Aloha finishing.com - Pine Beach, New Jersey |
Inconsistent finish of Zinc-Nickel Plating with Yellow Chromate
Q. I am facing Quality problems with Zinc Nickel Plating with Yellow Chromate. The Finishing is inconsistent. Please advice on concentration and timing. We are selling Nuts and Bolts. Currently using Chromate Powder.
Paul NettoCoating Manager - Johor , MALAYSIA
October 31, 2014
A. Hi Paul. We'd all like to help you, but people devote decades of their lives towards solving such problems. Have you called in your zinc-nickel plating process supplier? If you can narrow it down to one particular problem you encounter, and give us your complete plating cycle, we may be able to help. Presumably these nuts & bolts are hardened steel -- can you tell us the grade, etc.? Thanks.
Regards,
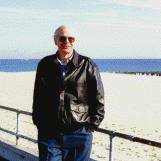
Ted Mooney, P.E.
Striving to live Aloha
finishing.com - Pine Beach, New Jersey
Q. After Degreasing and Acid Pickling, the studs and nuts (B7/L7) are placed in the Zinc Nickel barrel for approx. 1 hr to obtain thickness above 15 µm. The temp control for the Rectifier is 10-11 amp. Than the nuts and studs are dipped into Nitric Acid, Hot Water, Yellow Chromate solution (90 °C) and Hot Water again before they are blown dry using compressed air. The colour required is Rainbow colour but at times, very dull and rusty.
Paul Netto [returning]Coating Manager - johor bahru, malaysia
A. Obtain your chemical manufacturer's Technical Data Sheets and ensure you are following every detail. Amperage is not temp control. You say your parts are looking dull and rusty. I suspect that's not rust, but a thicker chromate layer which makes the end product look more like a dark orange/brown hexavalent chrome compared to the "rainbow" look you say you're after. Using your vendor's Technical Data Sheet, ensure you have the right concentration, temperature, and time in your chromate tank.
Art Campbell- OKC Oklahoma
[editor appended this entry to this thread which already addresses it in lieu of spawning a duplicative thread]
Q. I am facing the problem in blackness in fastener plated alkaline zinc nickel.
- Rohtak Haryana
April 19, 2017
Ed. note: please see the several very good answers to Parthasarathy's earlier question which was very similar to yours.
Zinc-Nickel Plating turned dark in 10 days
Q. Hi guys, I am noob in Plating, I am working in a plating company in my city and I have a some questions, why the color of plating changed. For example I produced some parts one day, and 10 days after, the color is different? I had light parts with zinc-nickel coverage but later the parts are dark or brown.
Edgar Garcia- San Luis Potosa, Mexico
May 15, 2017
Hi Edgar. I realize that you admit to being a newbie, but it's still difficult to figure out the cause of a problem that is only verbally described (no pictures) and when we have no process information. First question: the parts are presumably chromated; tell us about the chromating step. Thanks.
Regards,
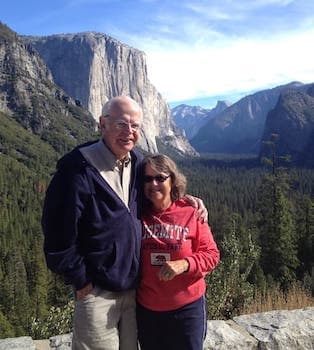
Ted Mooney, P.E. RET
Striving to live Aloha
finishing.com - Pine Beach, New Jersey
Q. Hi Ted, thanks for your answer.
We receive casting from our area of machines, the process is as follows:
Ultrasonic degrease
Hot degrease
Rinses
Pickling
Rinses
Electroclean
Rinses
Neutralize
Rinses
Zinc-Nickel Plating (pH 5.2-5.6, Temp 33 °C)
Rinses
Passivate
Rinses
Sealer
Drip
Dryer
It's the complete process to our product. (Acid Zinc Nickel)
- San Luis Potosi, Mexico
A. Hi Edgar!
As Ted said, please take some pictures of the parts before and after discoloration.
Do you test your plating bath in Hull cell? Does this defect appear in this test too?
Hope we can help you solve this!
Regards,
TEL - N FERRARIS - Cañuelas, Buenos Aires, Argentina
Q. Hi guys. I'm a newbie in acid zinc nickel plating with barrels and I have some problems. I had a new project that is acid zinc nickel plating with high percentage of nickel (12%-15% on parts); I produced it with trivalent passivation for 25 seconds.
Then when the process finished, it doesn't look good. The parts have a yellow shade. The percentage of Ni is between 12% and 15%, but regarding appearance I'm not sure. Can anyone show me what the appearance of high percentage Ni product should be?
Best regards,
- Bangkok,Thailand.
January 29, 2018
A. Hi Sirasit!
I think you have iron contamination either in your zinc-nickel bath, or in your chromate (or both).
Test your baths for iron. If you find it, remove it (purifying with hydrogen peroxide/activated carbon in your bath, usually there is no easy solution for the chromate) and try again.
You should neutralize with nitric acid (1%) and see if you have yellow shading in your parts. If not, the contamination must be in the chromate. Alternatively, you can plate a hull cell with a brand new bath and use the chromate to check how it works. If it turns yellow, it's the chromate, if not, it's the bath.
So, you have some ideas to work with. Tell us if some of these helped you!
Best of luck!
TEL - N FERRARIS - Cañuelas, Buenos Aires, Argentina
Q. Good evening sirs/madams. Many of the electrical connectors we specify for work that traditionally use a cadmium plating are getting replaced with a "black zinc-nickel" plating. I can't really find any information about this coating other than performance blurbs on connector datasheets from various connector vendors. Is this applied similarly to zinc electroplating?
I'm a garage/backyard experimenter as a hobby who has had luck zinc plating previously. I am interested in trying the plating for small personal projects.
Hobbyist - Parsippany, New Jersey
May 24, 2019
A. Hi Dave. If you are buying proprietary solutions, you may well be able to zinc-nickel plate and black chromate. If not, while you are certainly welcome to try, in my estimate you will probably not achieve success.
As an aside, you may have read about students making lemon batteries for their science class by slitting a lemon and inserting a copper penny and a zinc coated roofing nail, and generating about 1.1 volts of electricity between the two electrodes. Copper very strongly (1.1 volts worth) wants to come out of solution and displace zinc metal, forcing the zinc into solution in its place.
From this, and similar situations like zinc from zinc boat anodes going into solution to prevent steel hulls from doing the same, you might wonder how it can be possible to electrodeposit brass or a zinc-nickel alloy. When the zinc desperately struggles to go into solution rather than plating out as metal.
One way to achieve it would be to have hundreds if thousands of times as much zinc in solution as nickel, but then almost the instant you turned the power on all the nickel would be depleted. The practical solution is that suppliers have figured out how to complex/chelate/sequester the copper or nickel ions so that while there is plenty in solution, the concentration of "free" ions is ridiculously low. These complexors tend to not be generic chemicals but trade secret proprietaries. Good luck.
Regards,
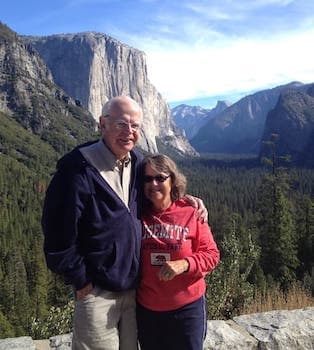
Ted Mooney, P.E. RET
Striving to live Aloha
finishing.com - Pine Beach, New Jersey
Q. Hi,
We do alkaline zinc nickel with trivalent blue passivation finishing. Thickness min 5 µm. We control the Zn and NaOH at 8-12 g/L, 116-125 g/L respectively. Before passivation we dip it in 0.1% HCl.
My question, as attached pic, a black line will appear at HCD and MCD area.
Already do Hull Cell but don't have any issue and the thickness ratio also okay (hull cell at 2 amp, 10 min). This black line can be seen as earlier after zinc nickel plating. Check thickness at black line have high Ni% and low Zn plating.
Secondly, at the edge of part, also have skip colour passivation. Refer to picture.
Please advise.
Thank you.
- Johor bahru, Malaysia
September 30, 2020
A. Hi.
You are doing Zn Ni plating.
Do you control Ni content? What is the concentration?
What is sodium carbonate reading?
Current density?
What is material of the parts?
Which specification you are using? Should be Ni only 10-20% compare to the Zinc content.
My Opinion from observation:
1) Low nickel content (g/L)
2) Adjust current density.
3) LAST, check chromate/ passivation tank.
Thank you
- Selangor Malaysia
Q. Plating colour is coming like silver in Zinc-Nickel Black Passivation bath.
Hi ,
I am facing some problems in Zinc-Nickel black passivation bath. When I have loaded parts in bath after plating, colour is coming like silver. And we did not get bright colour in black passivation. I am setting current a 15 ASF. Some parts I am getting good result.
Kindly help me, when I was wrong.
Thank You.
- Bangalore, India
January 28, 2021
Q. Dear All,
When we are doing rework on zinc-nickel black passivation part, that time plating has not happening properly. I don't know why this issue is coming.
We are using 50% HCl bath for removing plated section.
Kindly let me know if any changes require from HCl bath or any other?
Thank You,
- Bangalore, India
June 25, 2021
Q, A, or Comment on THIS thread -or- Start a NEW Thread