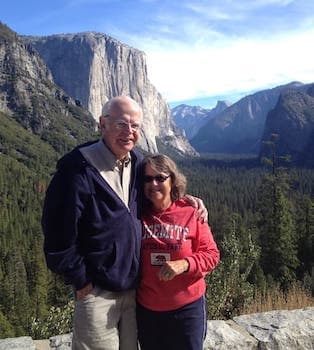
Curated with aloha by
Ted Mooney, P.E. RET
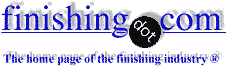
The authoritative public forum
for Metal Finishing 1989-2025
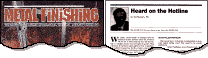
-----
Marine repair shop needs to purify hard chrome plating solution
1. How to decrease the Cr3+ and iron content of chrome plating solution?
Victor MARMarine Engine Parts Repair - HONG KONG, Guangdong, CHINA
2003
Most people employ a porous pot and there has been some work done in electrodialysis. Have you contacted your chemistry vendor?
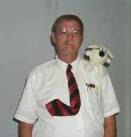
James Totter, CEF
- Tallahassee, Florida
2003
Victor,
Use a small rack smaller area than the anode area and use a current about 30 A/dm2. You can also use a porous pot for treat both trivalent chrome and also iron contamination.
Regards,
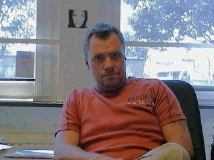
Anders Sundman
4th Generation Surface Engineering
Consultant - Arvika,
Sweden
2003
We are a marine reconditioning workshop in Hong Kong. In our daily operations, we recondition the piston crowns from the marine diesel engines of vessels. On the piston crown ring groove surfaces, we need to plate on a layer of hard chrome of about 0.5mm (finished thickness). The purpose of the hard chrome is to provide a erosion & corrosion resistant surface on the piston crown ring grooves. So far, it seems our plating quality is at an acceptable level. But the product from one operator likely has a longer durability. We found out that the difference in chrome produced by this operator and ours is in the amount of micro-cracks found on our chrome. Theirs has a larger and denser amount of micro-cracks. We wonder if this is the reason for a better durability of their product. Also, what actually is the effect & influence of micro-cracks existed in chrome? How to make more micro-cracks appear? I would very much appreciate if you could advise on this issue. Thanking in advance for your assistance.
Best regards,
Harvey WongMarine reconditioning workshop - Hong Kong, The People's Republic of China
2003
Most likely their chemistry is different. They use proprietary bath and yours is probably a general purpose sulphate 100:1 bath. The reason for their increased durability is obviously more lubricant retention. Contact a reputable chemistry house and ask them for mixed catalyst chemistry.
Guillermo MarrufoMonterrey, NL, Mexico
2003
2003
Harvey, Heef 25 has more microcracks than sargent's chrome solution has. Yes with more microcracks the better will also the lubrication shows, because these microcracks can carry more grease or oil than a standard chrome deposit can. To make these microcracks larger can be done with etching in a chrome solution. I will recommended to read Metal Finishing Guide Book about this or another book by Guffie.
Regards,
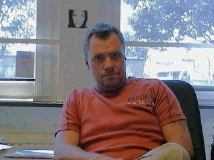
Anders Sundman
4th Generation Surface Engineering
Consultant - Arvika,
Sweden
Electrodialysis of HEEF 25
Q. Hi all,
Can anyone give me any information as to the efficiency of electrodialysis of HEEF 25? There seems to be very little online with regard to this technology, but the small amounts I have found give the impression that it a superior tech to IX technology.
A porous pot is our current method of tramp metal (iron and copper)removal, but it seems to be quite ineffective, especially where iron is concerned. We have not yet experienced any plating problems, but, periodic testing would indicate that this will be short lived if the issue is not addressed in the near future.
We plate hydraulic piston rods in a 3500 L tank.
Any comments or advice would be appreciated.
QC - Sparwood, BC, Canada
September 4, 2013
A. Several years ago we ran several medium size HEEF 25 tanks. We used a porous pot to control tramp metal ions and tri chrome levels. We had zero problems with it.
A thought would be a plugged porous pot or poor anode to cathode areas/spacing, wrong voltage, bad connections to the bus bar or a bad design of the pot or the wrong material for the pot.
- Navarre, Florida
September 6, 2013

Q, A, or Comment on THIS thread -or- Start a NEW Thread