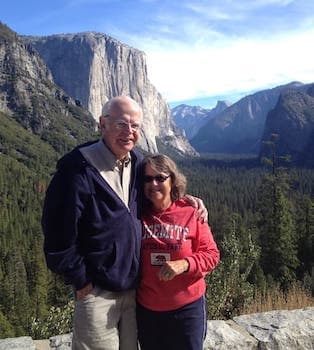
Curated with aloha by
Ted Mooney, P.E. RET
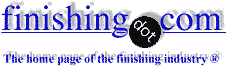
The authoritative public forum
for Metal Finishing 1989-2025
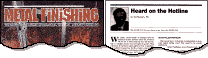
-----
Too little ferrite in my 316 C12 castings. What will happen?
I have a question about ferrite content in stainless steel. I have a cast stainless steel part which historically has required that the ferrite content be between 6 and 20%. A new manufacturer of this part can only achieve a ferrite content of 4%. My questions is, what properties are affected by the content of ferrite in a 316 C12 stainless steel casting? I need to determine whether I can accept these parts based on the lower than expected ferrite content.
Ben MellickProcess Instrumentation manufacturer - London, United Kingdom
2003
Austenitic stainless steels do not usually solidify as fully austenitic, hence the necessity for specifying a certain percentage of ferrite in castings and welds. Higher ferrite is detrimental to corrosion resistance, but reduces cracking during solidification. My guess is that a lower percentage of ferrite will be better, as long as the application does not involve welding.
Toby PadfieldAutomotive module supplier - Michigan
2003
2004
Depends on the application of the piece. With delta ferrite you may have corrosion (ammonia components, 0% required).
With high delta ferrite lower surface finish and/ or brittleness and corrosion (if there is a post weld heat treatment, because of sigma phase formation, petrochemical industry <8%).
With low delta ferrite you may have hot cracking in weld metal, higher chances of sensitization (because of carbides precipitation in post weld heat treatment).In addition without delta ferrite it seems that you might have cracking if the piece undergoes heating in the 580 to 800 °C.
4% could be a nice figure for some applications.
Do not forget that the percentage of delta ferrite is dependent on the measurement method (ferromagnetic, microscope determination, chemistry)
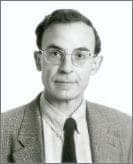
P. Veron
ENSA - Santander, Spain
dear all,
I am expediting valve castings made of c12 & c12a castings which have shown high susceptibility to have visual cracks and mpi cracks, thereby increasing my lead time; apart from this they have shown heavy shrinkage characteristics.
My question
1. Are these intermediate range freezing alloys. Which have dendritic growth forming pools of rich solute at end of solidification.
2. If this were to be true what should be done to avoid them if possible completely eliminate them.
3. Does it need any method changes or chemistry changes
supplier developer/methods consultant - Bangalore, India
July 5, 2011
July 21, 2011
We have been manufacturing billets by continuous casting and then by hot rolling in the size range of 50 mm square to 100 mm square.We have observed that controlling delta ferrite lower than 5% has been very useful in reducing edge cracking during hot rolling and subsequently forging flanges.
The user of flanges ,however insists in having delta ferrite more than 5%
What will be the adverse effect on flanges during/post welding in flanges with delta ferrite less than 4%, as this is contrary to the need of hot forging/rolling.
Soaking time reduction at 1220 °C could help us reducing hot cracking ,but will it have any effect post on welding?
Product designer - Pune, Maharashtra, India
Q, A, or Comment on THIS thread -or- Start a NEW Thread