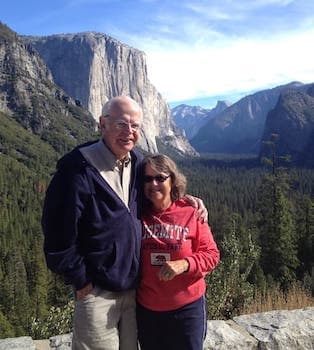
Curated with aloha by
Ted Mooney, P.E. RET
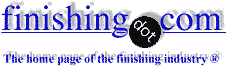
The authoritative public forum
for Metal Finishing 1989-2025
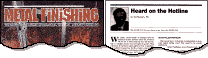
-----
Cut/sheared edge of metal parts rusts. What's a better coating for office equipment / printers/ copying machines?
Q. Dear Sir,
We are a Hong Kong company making office appliance metal parts, such as copy machine. Rust is happening on the cut edge of metal parts (electroplated metal) within a very short period. It is our headache problem. As per our understanding that your company providing anti-rust coating for the metal, would you please introduce your product that is suitable for the solution of our problem?
Best Regards,
Patrick LauOffice Appliance Parts - Dongguan, Guangdong, China
2003
A. I am having a little bit of language difficulty here, Mr. Lau, but I think you are saying that you are using pre-plated stock and the sheared edges are rusting?
You didn't say what the stock is plated with, and that's very important! If the sheetmetal is zinc plated, there should be at least some measure of protection afforded by the adjacent zinc on the surface because zinc plating offers cathodic protection to steel. If the metal is nickel plated or tin plated though, those coatings offer only barrier layer protection, so the cut edge is going to rust immediately because this materials are cathodic to steel and accelerate its corrosion.
In terms of an immediate practical solution, it is imperative that the parts be thoroughly dried after any process operations that may wet them, and that the last liquid they see is alkaline rather than acidic. Whether a post-dip has any chance of helping probably again depends on what the metal is plated with. I'm sure you already know that ideally the edges ought to be rolled or the parts plated after forming. Good luck.
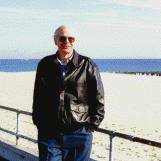
Ted Mooney, P.E.
Striving to live Aloha
finishing.com - Pine Beach, New Jersey
2003
Q. Dear Sir,
Do you have any ideas how long before the cut edge of electro-galvanized steel sheet metal parts get rusty when they are stored in a warehouse with 30-38 °C and > 80% RH.
Looking forward to having your reply.
Thanks,
- Hong Kong
2006
Q. Need some advise from you. I am stamping STPE materials (pre-plated) in Shanghai where the climate is wet. The stamped cut edges rust fairly quickly. Is there any solution to prevent the cut edge from rusting. Currently we are thinking of stripping and re-plating the layer of tin. Is there a more economical solution.
Thanks for your advise.
Regards,
- San Jose
2007
A. Hi Dennis. A dip in a rust preventative or even an alkaline cleaner should help. See previous response that insuring that the parts are dry is very important.
Regards,
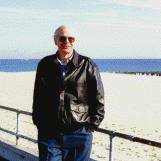
Ted Mooney, P.E.
Striving to live Aloha
finishing.com - Pine Beach, New Jersey
Q. We have a supplier that has given us some sheetmetal that has a desirable coating. It is cold rolled steel and is 19 gauge thick. The coating is smooth and is a light gray. It is not galvanized or galvannealed but I believe it is a secondary operation to one of these coatings. This material shows up in copiers, laser printers, and other machines. What is it and how do I spec. it?
David M. DezsePrinter manufacturer - Lewis Center, Ohio, USA
2003
A. Electroless Nickel Teflon co-deposit?
Todd Osmolski- Charlotte, North Carolina, USA
2003
A. There are several kinds of zinc rich coatings that can be applied to coil steel prior to forming. There is ZINCROMETAL from MCII and some others by Akzo Nobel. The coatings are applied by way of reverse roll coating and can be done very quickly (500 feet/minute). These types of coatings were very prevalent in Automotive 20 years ago; now most of the activity is in the appliance market. The coatings are formable, weldable and have excellent corrosion resistance.
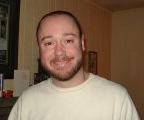
David J. Wolf
Medina, Ohio
2003
A. You might be looking at a co-deposit of Electroless-Nickel with particles of P.T.F.E.(Teflon). The Nickel provides excellent corrosion resistance and the Teflon provides self-lubricity for wear protection. It is utilized often in copy machines and printer components.
Charlie Camenzind- Phoenix, Arizona, USA
2003
Q, A, or Comment on THIS thread -or- Start a NEW Thread