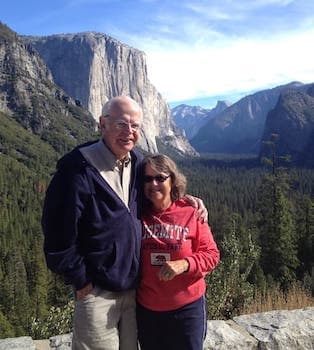
Curated with aloha by
Ted Mooney, P.E. RET
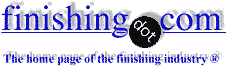
The authoritative public forum
for Metal Finishing 1989-2025
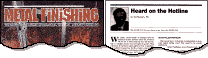
-----
Bromine is attacking architect's stainless natatorium
Q. Recently, we have completed a natatorium. In this humid space is a large pool which is treated with a bromine solution rather than a chlorine solution. We have begun noting many accessory items (hinges, pulley wheels, etc.) have begun to rust. While this is not surprising on surfaces where protective coatings have failed, it was surprising to see all stainless and chrome items have begun to corrode. With a little research, apparently bromine and other "halogens" take little or no notice of the protective oxidized layer of these metals. What should we have used in these instances? Note, most require some strength, so in many cases aluminum may not be feasible.
Rick HouseArchitecture - Pascagoula, Mississippi, USA
2003
A. What specific stainless steel alloys were used? Any weldments? As you have ascertained, not all stainless steel alloys are equally resistant to halogen containing environments. Type 316/316L probably is not sufficient for this application. Post again with more details, and we may be able to assist you.
Toby PadfieldAutomotive module supplier - Michigan
2003
Q. There are a variety of materials including a variety of stainless and chromes. The thrust of my question is primarily what SHOULD we have used. Specifically in the area of miscellaneous hardware (i.e. hinges, screws, etc.). Essentially, anything that can't be aluminum due to the stresses of installation and/or of the application. I suppose there are forms of titanium and such, but I was hoping someone had some ideas regarding metals which can be used in a "wet" halogen environment. Short of engineered plastics, I'm at a loss. I am willing to also hear any halogen protective finishes which could be appropriate (however, hinge actions may negate such). I have noted there may be a variety of nickel-copper alloy which may meet this scenario, but I haven't determined the exact alloy. Any thoughts are welcome.
Thanks,
Rick House [returning]Architecture - Pascagoula, Mississippi, US
2003
A. Rick,
First, I completely missed the reference to chrome in your first letter, because I would have commented separately about that. Chrome-plated steels will perform poorly in this type of environment, and really should not have been considered. If it needs to be shiny and metallic, a suitable stainless steel alloy should be the starting point.
Second, it is difficult to answer the question of what should have been used without sufficient details. It is possible that Type 316 stainless steels that have been electropolished and properly passivated would perform adequately in some applications. Others would likely require an austenitic alloy with greater Mo, such as Type 317, 904L, AL-6XN, etc. Duplex alloys like 2205 and 2507 also have enhanced resistance to pitting in halogenated environments. It is possible that some copper-based alloys would perform adequately, and therefore you would not have to go to higher performance (cost) alloys like titanium or nickel.
And third, it sounds like you would benefit from the expertise of a metallurgist with a background in corrosion. I would start by discussing the applications with engineers from producers like Carpenter, Allegheny Ludlum, AK Steel, etc., and then work my way to distributors like Rolled Alloys.
Good luck.
Toby PadfieldAutomotive module supplier - Michigan
2003
Toby,
Thank you very much. That is the type of information I was hoping for. This gives me an excellent starting point from which to begin searching for alternate materials and/or passivation. I like the idea that an electropolished and passivated 316 stainless could be used if executed properly.
That's the problem with architecture, being "Jack of all trades, Master of none". We tend to know just enough to get into trouble. And in such a wet bromine environment as this one, it is easy to overlook details as hinge material.
Rick HouseArchitecture - Pascagoula, Mississippi, US
2003
A. There is a family of chemicals called silanes that are very new. When applied over the top of a substance they become very difficult to remove. Since they are silicon based they reduce to SiO2 with heat. You may be able to put them over the top of the hardware before use and corrosion, then heat them to reduce the coating to SiO2. Once there the only chemical we have been able to remove them with is HF. Since HF is a halogen, you can expect that the bromine may eventually remove the coating, but we have not been able to remove it with HCl so it may be okay. A little goes a long way so a liter may be too much.
Dave Fairbourn- Sandy, Utah
2003
Q, A, or Comment on THIS thread -or- Start a NEW Thread