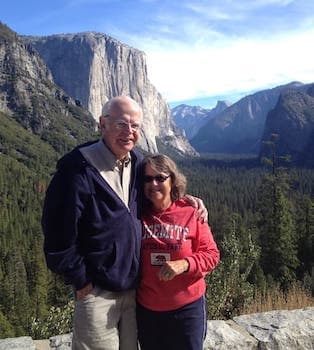
Curated with aloha by
Ted Mooney, P.E. RET
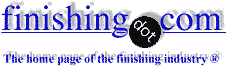
The authoritative public forum
for Metal Finishing 1989-2025
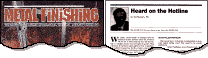
-----
Tin Plating Tellurium Copper
Q. Does anyone know of a specific cleaning process for Tellurium Copper CDA145 that enables it to be tin plated? Currently having problems getting tin to adhere.
Tony Boninaelectrical connectors - Littleton, New Hampshire, USA
2003
A. Stay out of cyanide altogether. Alkaline clean (electro is optional), 5% Sulfuric Acid, copper sulphate ⇦ this on eBay or Amazon [affil links] electro-strike in any sulphate copper plating electrolyte WITHOUT ORGANIC ADDITIVES,. then go into tin (or anything else).
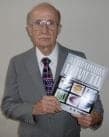
Robert H Probert
Robert H Probert Technical Services

Garner, North Carolina
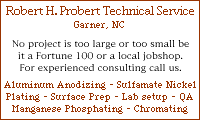
2003
A. This copper alloy is common used in the semiconductor industry (like Olin 7025). It requires activators that are preparatory. A procedure used in Japan for this alloy is to activate and cyanide copper strike. Then proceed to additional plating.
Louis HirbourAnaheim, California, USA
2003
Tin Plating is Peeling from Copper in Low Current Density Areas
Q. Hi,
I need some help. We plate tin over copper in a continuous plating line.
We have been having a plating peeling issue where the tin plating peels at the lower current density side. This only occurs at random portions at the lower current density side. The high current density side is not affected. I need to know what is the mechanism behind the peeling and how to prevent it from re-occuring. Thanks.
- Malaysia
October 28, 2014
A. Hi Bob. Plating problems are almost never easy, so we'll probably need to know the grade of copper and the complete plating cycle. But for a quick guess: does the cycle include electrocleaning? Is it possible the LCD area is getting little if any electrocleaning?
Regards,
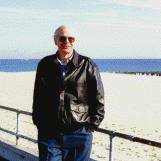
Ted Mooney, P.E.
Striving to live Aloha
finishing.com - Pine Beach, New Jersey
October 2014
Q. Hi Ted,
Yes, the cycle does include electrocleaning. This issue was intermittent which was only detected after peeling test was conducted. It did not peel off as plated.
Regards
Bob
- WP, Malaysia
October 30, 2014
![]() |
October 30, 2014 A. Hello Bob, Process Engineer - Phoenix, Arizona USA A. Soon after you fix the adhesion problem you are going to get to another problem. Tin plating solutions are extremely sensitive to copper contamination. For sure, the low current density area of your recesses is delivering a lot of copper into the tin plating solution. You need a tin strike solution to act as a sewer to cover the copper so that the real quality tin plating solution only "sees" tin. Until you can add a tin strike, then at least "go in hot". ![]() Robert H Probert Robert H Probert Technical Services ![]() Garner, North Carolina ![]() October 31, 2014 |
Q. Hi Mark and Robert,
Thanks for the reply. The problem was resolved after changing the pre cleaning chemicals and filtration of the plating bath.
The grade of the copper is C194. This process includes electrolytic cleaning and electrolytic deburring, it also has an activation.
One question now is how do we identify the faulty parts from the good parts. How do we identify which parts will peel (parts with the weak adhesions) compared o good parts.These parts will only peel after exposed to heat cycle. What is the best way of identifying the faulty parts from the good parts without going through the heat cycle.
Regards
Bob
- WP, Malaysia
November 1, 2014
by Jack Dini
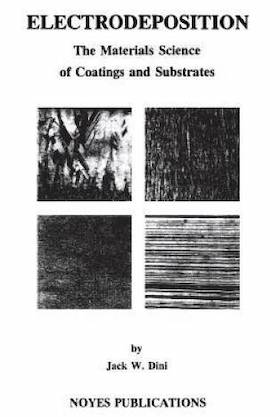
on eBay or
AbeBooks
or Amazon
(affil links)
A. Hi Bob. The thing is, the heating is not the problem, the lack of adhesion is. Even the parts that pass may have only marginally acceptable adhesion. Heating is just one of many "go / no-go" adhesion tests.
How to solve the problem depends on how much effort you want to put into it. If you have access to a copy of Jack Dini's "Electrodeposition: The Material Science of Coatings and Substrates".
it has a chapter entitled "Adhesion" of 44 pages with 74 references to help you understand the subject in great depth.
One problem is that you have a qualitative test for adhesion: "failed or didn't fail when heated" ... but you don't have a quantitative test to make sure you are holding the adhesion strength within limits so you can track the problem. There are tests such as the Modified Ollard Test that could allow you to quantify the adhesion at any spot on the coil under any deposition circumstances. Please see letter 18002, "Hard Chrome Plating Bond Strength and Test Methods: Modified Ollard Test". You might try a few tests to determine the maximum and minimum adhesion strengths you are getting. You could also run tests on various spots and various conditions (new cleaner/old cleaner, top side/bottom side, high amperage/low amperage, Monday morning/Friday night, etc.), but it would be a huge amount of work. Because quantitatively tracking adhesion strength is so much work, it may be more practical to just maintain pragmatic, empirical control over your deposition parameters.
But if the problem continues to manifest itself in LCD areas, and continues to be solved by refreshing the cleaners and pretreatment baths, I would look into whether you can reposition anodes & cathodes to get more electrocleaning action (gas bubble generation) in the LCD area. Good luck.
Regards,
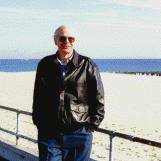
Ted Mooney, P.E.
Striving to live Aloha
finishing.com - Pine Beach, New Jersey
November 2014
Hi All,
Thanks for all the replies, the responses were insightful and helpful. We will look into all of the advice.
Thanks,
Regards,
Bob
- WP, Malaysia
November 3, 2014
Q, A, or Comment on THIS thread -or- Start a NEW Thread