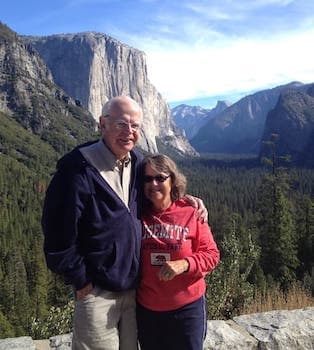
Curated with aloha by
Ted Mooney, P.E. RET
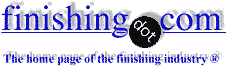
The authoritative public forum
for Metal Finishing 1989-2025
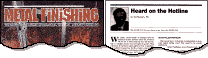
-----
Powder coat adhesion problem on zinc plate
Current question & answers:
Q. Can anyone help me out on an adhesion question? I currently powder coat over pre-galvanised tubes which are welded, then the welds are ground back smooth. Next the material is solvent wiped to degrease, then mechanically sanded with 80-grit paper. Then another solvent wipe, then an aerosol zinc rich primer is used prior to coating with epoxy powder primer, then a top coat of polyester powder.
I'm getting delamination over the welds occasionally. it's like the aerosol zinc isn't binding to the substrate even after mechanical sanding. Please help.
Brad HarrisonProduction manager - Perth Australia
January 18, 2022
A. I've seen similar "pretreatment" routes before for similar materials, but never seen long term consistently good performance from that.
I suggest an alkali degreaser, rinse, zinc phosphate, demin rinse (at minimum). It might be dip or spray. You might add an activator such as zirconia before the zinc phosphate.
The ZnP will help with corrosion over the bare exposed welds.
I'd skip the zinc rich primer, that seems superfluous with an epoxy primer, and being aerosol applied likely to ensure you get gassing and delamination in the epoxy primer / polyester top coat.
Do you cure between coats? Part cure? Or spray one powder on top of another and do a single cure?
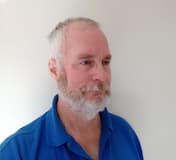
Geoff Crowley, galvanizing consultant
Crithwood Ltd.

Bathgate, Scotland, UK
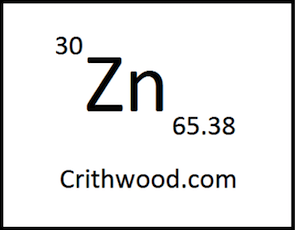
February 20, 2022
Some key quotes on this subject from this thread:
Closely related Q&A's, oldest first:
Q. We have a powder coat adhesion problem when applied over zinc plating. I see from reading your site that we are not the only people with this type of problem. Some batches of plated parts powder coat fine. And on some it falls off in great patches. I have spoken to the platers but they offer little help. We only have 2 operators in our area to choose from and I have tried both. I personally know little about the zinc plating process so I need to know what questions to ask when I next meet with them.
Mike OwensSheetmetal Engineering/Powder coating - Christchurch, Canterbury, New Zealand
2003
A. The curing of powder paint over zinc electroplate outgasses and blows thru the partially cured powder. Organic additives in the zinc electroplate (worse with Acid Chloride formulations) explode thru the powder.
The same is true for the chromate conversion coating. The chromate should be very thin because the thicker films will separate from themselves.
Best case: Alkaline zinc with least amount of brightener held on the slightly less than bright side, then a very thin chromate, then ramp up the baking very slowly.
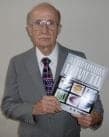
Robert H Probert
Robert H Probert Technical Services

Garner, North Carolina
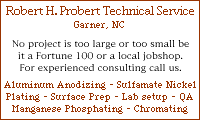
2003
A. First let me ask you why you used zinc plating in your product and then give it powder coating? Surely you will face many problems by this method. The adhesion of powder coating after curing with zinc plate surface is very poor and the surface finish not good because some gas and organic additive will be evaporate during curing of powder. So you must change the finish of surface before you paint it powder like steel and make phosphate for it before powder coating by these method you will increase the adhesion and improve the finish of surface after curing. If it is very difficult so, you must accept alkaline zinc plate with least amount of brightener may be not bad.
Aly Gomaa- Cairo, Egypt
2003
A. The key to getting adhesion of powder coating on galvanizing or Zn plate (we do both here), is the PC pretreatment. Degreaser Acid etch Zinc phosphate Lots of rinses in between. We get excellent adhesion on Zn plate and on hot dip galvanized. For thick HDG coatings, degassing is required (heat to 210 °C for about 10 mins) then pretreat.
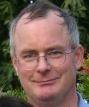
Geoff Crowley
Crithwood Ltd.
Westfield, Scotland, UK
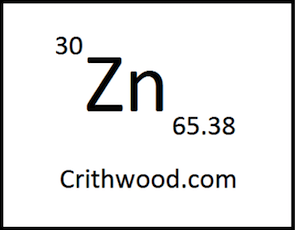
2003
Dear Sirs,
If you can find a local metal finisher who will develop a waterborne primer, then you may find that adhesion and corrosion resistance will be an improvement over a one coat powder system. We have finished such a product for 4 years now and it shows no sign of failure as a system primer/powder (galvanized crash barriers after 4 years in a hostile environment).
Birmingham, United Kingdom
2003
Multiple threads merged: please forgive chronology errors and repetition 🙂
Q. We have been told by our chemical supplier, that "Chem Treated" zinc plated steel with cause us to have powder coat adhesion failures.
Is there a problem powder coating Chem treat zinc plated steel?
Pentair - Des Plaines, Illinois, USA
2006
A. Some zinc plating and galvanising is chromate passivated, to protect against weathering corrosion. Unfortunately this also causes powder coating adhesion problems. You need to check with your material suppliers what they have applied after the zinc. A caustic & surfactant cleaner, and/or acid & surfactant cleaner should remove the problem. Be careful about immersion time when using an acid cleaner.
Dale Windridgearchitectural powder coaters - United Kingdom.
2006
A. Hi Rich. Zinc electroplating followed by the new RoHS-compliant chromate conversion coatings should be a good answer. The "thick film" complexed chromate versions are reportedly excellent because their very low water content makes them relatively immune to the dehydration problems that can occur during baking. In a career of 50 years I never saw zinc electroplated finishes that were not chromate conversion coated, so I doubt that that option will be available to you anyway.
If you are speaking of hot dip galvanized finishes, they should not be chromate quenched, but zinc phosphated before the powder coating. When possible, to avoid contract disputes, it's ideal if they are plated & powder coated, or galvanized & powder coated by the same shop.
There are several threads on each of those topics here. But understand that zinc electroplating and hot-dip galvanizing are different, so answers which apply to one should not be presumed to apply to the other. Good luck.
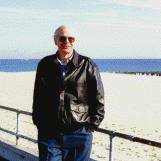
Ted Mooney, P.E.
Striving to live Aloha
finishing.com - Pine Beach, New Jersey
Q. Dear sir,
Can we do powder coating on galvanised components as we are facing internal corrosion if mild steel tubes are used. If yes, then what is the process?
Thanking you,
joshi
automobiles - honda sattari goa India
September 22, 2012
A. Hi y.b.
Geoff has described the traditional process for this situation: zinc phosphating in between the galvanizing and the powder coating. Good luck.
Regards,
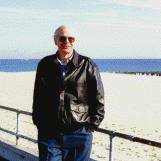
Ted Mooney, P.E.
Striving to live Aloha
finishing.com - Pine Beach, New Jersey
September 23, 2012
Q. Sir we were using electro galvanized steel. When we were applying powder coating process on that material most times we were facing peel off problem, so give me instruction to avoid this issue. We were using pretreatment solvent degreasing method; after SD, heating that component inside the oven for 20 mins at 180 °C temp. Please give me help
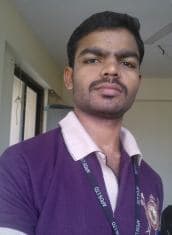
Gopi Nath
- Mumbai, maharastra, India
December 10, 2014
A. Hi Gopi. Sorry, solvent degreasing is not adequate pretreatment for any substrate, but certainly not zinc plating. You should probably do the zinc phosphating described by Geoff. Good luck.
Regards,
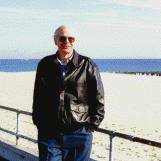
Ted Mooney, P.E.
Striving to live Aloha
finishing.com - Pine Beach, New Jersey
December 2014
Powdercoating pre-plated steel sheet
Q. Hi, I'm Frank and am working on an outdoor product. This is a sheet metal structure - raw material is zinc plated steel (pre-plated).
My powdercoating supplier is having problems passing adhesion test. I suspect this is a preparation issue. I'm looking for suggestions for the proper cleaning and preparation process, specifically for pre-plated sheet.
product designer - Santa Clara, California, USA
December 7, 2015
A. Hi Frank,
I assume that your pre-plated sheet is within use by date?
That is not a joke.
Most steel suppliers will have a specified date for very good reasons.
I also assume that you have ensured that there are no "white rust" preventative processes to which the sheet has been exposed?
If either of these conditions exist then your problem becomes complex.
So,Let us assume that neither complexity impinges?
That being the case then a multi stage Zinc Phosphate pre-treatment process prior to powder application should solve your problem.
Remember:Clean, Etch, Phosphate & multiple rinses finishing with DI.
Hope this helps,
Regards,
Bill
Trainer - Salamander Bay, Australia
Q. I'm trying to create a rough zinc plated surface to allow powder coating to stick better. Can you tell me what would be necessary to achieve that? Thank you.
Christopher GreenU.S. Rack - Madera, California, USA
August 1, 2018
A. Hi Christopher. If you reduced or left out the brighteners the plating would be larger grained and rougher. But this might leave you with two problems: first, the final powder coated surface might be too rough for good aesthetics; second, the adhesion might not be much, if any, better. And, of course, you'd have to find a plating shop willing to do it.
I think a better approach might be to find a shop which does both zinc plating and powder coating, and have the zinc plating zinc phosphated instead of chromated. Otherwise, as discussed above, a better zinc plating and trivalent chromating may offer sufficient adhesion.
Regards,
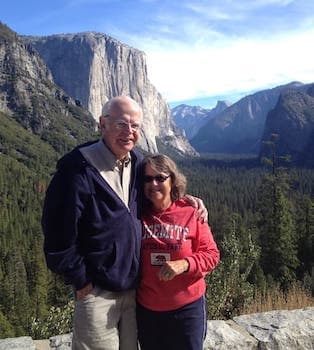
Ted Mooney, P.E. RET
Striving to live Aloha
finishing.com - Pine Beach, New Jersey
August 2018
Q, A, or Comment on THIS thread -or- Start a NEW Thread